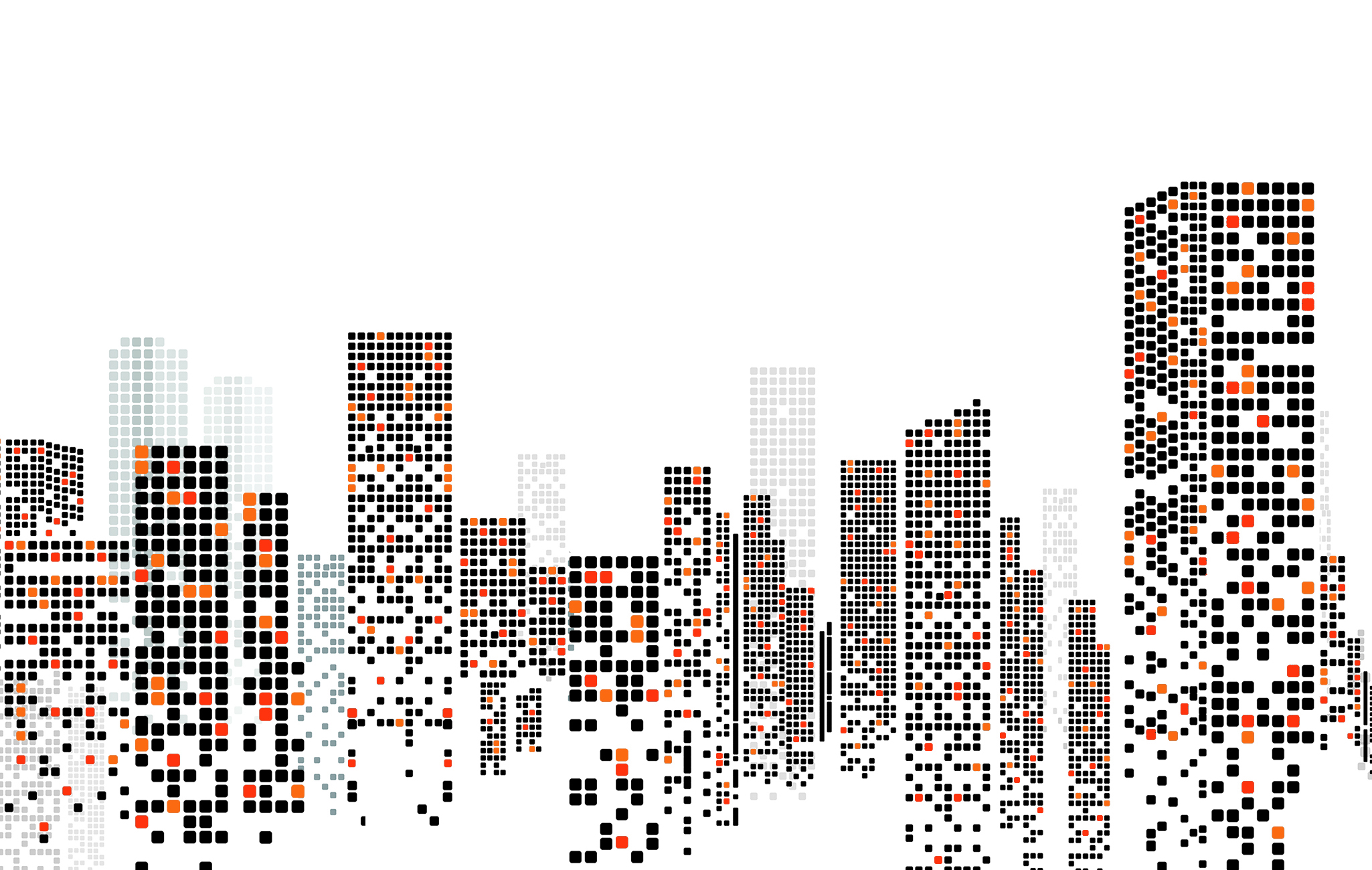
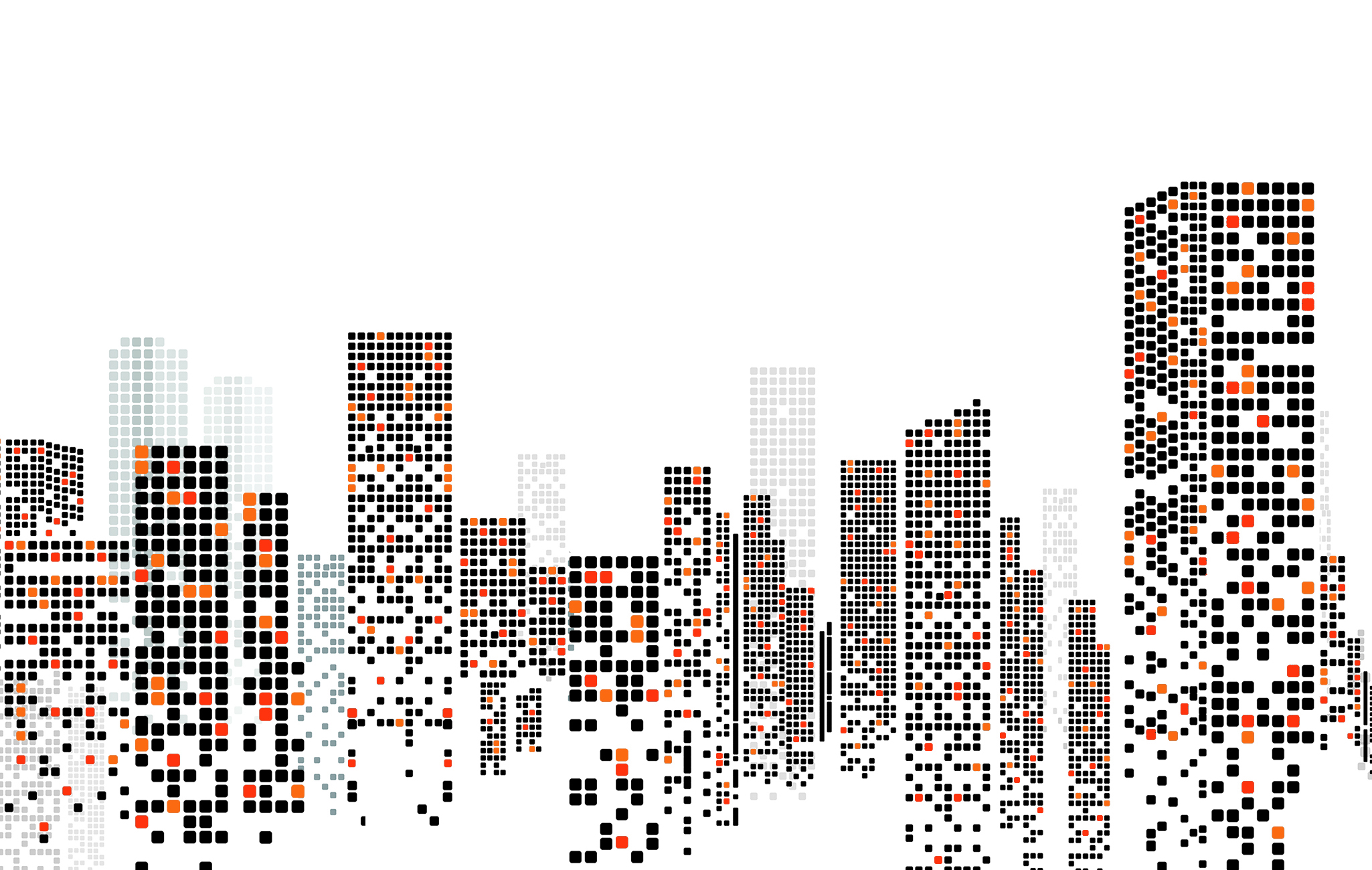
Buildings + Beyond Podcast
Podcast: Play in new window | Download
Kai Starn
Kai Starn is a Senior Sustainability Consultant at SWA on the Sustainable Building Services team. He is a green building advocate, serves on the board of the CT Green Building Chapter, and combines his enthusiasm for zero energy design with Whole Building Life Cycle Assessment.
Catherine Paplin
Catherine Paplin is a Senior Building Enclosure Consultant at SWA. She adheres to the twin precepts that preservation and restoration are inherently sustainable practices, and that designing for climate is an essential spur of good design.
For the past 30 years or more, when we’ve been talking about the carbon emissions of buildings, we’ve usually been talking about operational emissions – the carbon put in the atmosphere after the building is built. We now know that 30-50% of a building’s total carbon emissions are already in the atmosphere before the lights are even turned on. These emissions are referred to as embodied carbon. There is an enormous, industry-wide effort underway to incorporate accounting for embodied carbon in construction, because the realization has dawned that you can’t build ‘green’ without it.
On this episode, Robb sits down with SWA’s Kai Starn, Senior Sustainability Consultant, and Catherine Paplin, Senior Building Enclosure Consultant to hear about WHY embodied carbon is becoming a larger part of the conversation.
Free:
For purchase:
Send your feedback and questions to podcast@swinter.com
Buildings and Beyond is the podcast that explores how we can create a more sustainable built environment by focusing on efficiency, accessibility, and health.
Buildings and Beyond is a production of Steven Winter Associates. We provide energy, green building, and accessibility consulting services to improve the built environment. For more information, visit swinter.com.
Hosts: Robb Aldrich | Kelly Westby
Production Team: Heather Breslin | Alex Mirabile | Dylan Martello | Jayd Alvarez
Kelly: 00:06
Welcome to buildings and beyond
Robb: 00:06
the podcast that explores how we can create a more sustainable built environment.
Kelly: 00:13
By focusing on efficiency, accessibility, and health.
Robb: 00:18
I’m Robb Aldrich.
Kelly: 00:19
And I’m Kelly Westby.
Robb: 00:23
For this episode I talked with Kai Starn and Catherine Paplin. They’re my colleagues here at Steven winter associates. Kai focuses mostly on green building certification for larger commercial buildings and Catherine works on high performance building enclosures, also for bigger buildings. and we’re talking about embodied carbon and this is an issue we’re seeing more and more, in more and more different places. When youre talking about carbon, we’re talking about greenhouse gas emissions, carbon dioxide is the biggie, but there’s also methane, nitrous oxide and halogenated hydrocarbon gases, HFCs, refrigerants, blowing agents, etc. When we talked about carbon until fairly recently, most people were talking about operational carbon – a building uses energy, a lot of energy is generated by fossil fuels. Burning fossil fuels gives off CO2 and that was what we’re trying to reduce. When we’re talking about embodied carbon, we’re talking about the materials themselves and the building itself, the material extraction, processing, transportation, construction. When you analyze the whole carbon picture, people who do it rigorously do lifecycle assessments or LCAs, which is a pretty rigorous analysis. We’re not getting too deep in this discussion, but this is a quick conversation to talk about why and how and where we’re seeing this embodied carbon issue come up more and more. We’re all seeing it more and more. If you want to learn more, check out our show notes. Katherine and Kai linked to some great resources. And if you can make it to Boston later in March, I encourage you to check out NESEA’s BuildingEnergy conference. NESEA is the Northeast Sustainable Energy Association, March 23rd and 24th at the Westin Boston waterfront. I think I’ve missed one of these BuildingEnergy Boston conferences over the past 20 years. I’ve gone for quite a while. I’m looking forward to this year. A colleague and I, Nicole Ceci and I, are doing a session on building electrification called”To Electrify or Not to Electrify,” it’s a discussion or perhaps a debate on prioritizing electrification efforts, building electrification efforts. I’m looking forward to that. And also I just looked at the program and there are three sessions focused on embodied carbon. This has been a hot topic at NESEA BuildingEnergy Boston for the past few years. So come check that out. March 23rd and 24th, 2020 Western Boston waterfront, go to nesea.org N E S E A .org for more info. In this conversation with Catherine and Kai, we started discussing why we’re hearing more about body carbon these days.
Catherine: 03:34
We now have evidence that the amount of carbon emissions from a building during its whole life cycle, on average, 30% of that is from embodied carbon – is from building the thing. And if you’re looking at a 30 year projection, the first 30 years of the building’s life, then you’re looking at 50% of the emissions that will be due to that building being the result of embodied carbon. And all of those emissions are going in before the building even begins to be used. So it’s already there in reality by the time that you’re starting to use that building. And that is a huge thing to think about when you start looking at the horizons that are projected for climate change acceleration and possible tipping point.
Robb: 04:54
Yeah. So if reducing carbon emissions, carbon dioxide equivalent emissions is a priority, this is definitely something you should be looking at. I mean that’s huge. So basically constructing a building results in as much emissions as the building operating over the first 30 years does. Very generally speaking.
Catherine: 05:23
Yeah. And this is based upon the 2018 report on climate change and emissions. So this is top scientists in the world coming to a consensus about about this number.
Robb: 05:47
Gotcha. So that’s worldwide number?
Catherine: 05:50
Yes it is.
Robb: 05:50
Okay. And Catherine, you wrote a blog post on our website a while back about embodied carbon associated with different insulation materials. And that’s kind of eye opening. Cause obviously a key way to reduce operational carbon is to add more insulation. But some insulations have really big embodied carbon implications. Can you talk about that a little bit?
Catherine: 06:22
When you’re talking insulation, it turns out that more is not always better. Because there are types of insulation which are extremely commonly used. Namely plastic foams. And there’s a rigid plastic foam board commonly called XPS for extruded polystyrene. and there is a spray foam plastic insulation, closed cell, which is also used all over. And both of these are manufactured, and in the case of the spray foam, installed with a hydrofluorocarbon blowing agent, and that blowing agent has something like 1200, 1400, there are different estimates, but they’re all in the well over a thousand range, times the global warming potential of carbon dioxide. So when we talked about those those equivalent gases to carbon dioxide, this is one of that 2% of, of emissions gases that are completely out of proportion in terms of the amount of carbon emissions they actually represent. So what that really means is that when you go and put something like this, if you put just one inch of this insulation into your building, it’s going to be 36 to 40 years before you pay off, before you have saved all of the emissions that you just spent in putting that in there, and one inch is not enough insulation. So in reality, it’s decades and decades before you have made up for what you spent putting that in.
Robb: 08:47
No, that’s great. And it’s a huge number it’s kind of jaw-dropping. And cellulose comes to mind as what I would think would be the lowest, one of the lowest embodied carbon insulation. But is that accurate first of all?
Catherine: 09:09
It is certainly among the lowest. What you get into with insulation, and with all materials, is there’s a reason why we’re using these things. There is a reason why this is the most common commonly used material, or one of the most commonly used materials for insulation. And that is because it does so much so well – those two insulations give you among the highest R-value, that is thermal resistance value per inch of any insulation. And they have other qualities that make them extremely useful, even sometimes indispensable for particular uses. The spray foam is a vapor barrier. It’s an air barrier. It conforms to any irregularities and on and on.
Robb: 10:05
No, like you say, foam insulation is so appealing for so many reasons and it has been the Go To for many different applications for people on the leading edge of high performance buildings. And now maybe that will change a little bit and we’ll put a link to your blog post and and some of your sources for that in the show notes. But yeah things are changing.
Kai: 10:38
I just sort of want to reiterate sort of what we’ve been talking about. It’s really fascinating and it’s a really big deal talking about this carbon that’s front loaded into the buildings before we even move in. And you know, I think what we’re sort of talking about when we’re talking about these installations and stuff are high performance buildings – we want our buildings to operate at a low cost. And you know, that’s been the forefront of our minds since the 70s, you know, energy efficiency. And we’re starting to realize that these high performance buildings with these high embodied carbon materials release more total emissions then, you know, maybe a code minimum building with, you know, moderate body carbon emissions. And that’s a really big deal and sort of startling, and you know, we absolutely need these net zero energy buildings, we absolutely need those, and you know, we’re not disputing that. As Catherine said, these materials have properties that we need in areas. But just looking at the net zero by itself isn’t gonna get us to the goals to stabilize the temperature of the climate in the timeframe that we’re looking at.
Robb: 11:58
Yeah. So, in your work Kai are there a few materials – you’ve done a little bit of number crunching on building by building I think, and what are the big components where there are big problem areas or big opportunity areas to reduce embodied carbon?
Kai: 12:23
Yeah, yeah. I mean the, the short answer is to choose lower carbon materials and we could maybe get to that later how to do that. And maybe using carbon sequestering, natural materials. Also part of that short answer is just to use less material overall. You know, that’s one thing that we can look at early on, you know, different massing options, but in industrialized areas, the three main structural materials, concrete, steel and wood are the, are the drivers of embodied carbon by virtue of just how much fuel and energy it takes to create them, to bring them into existence.
Robb: 13:02 Yeah. Kai, maybe I’ll ask you, I mean programmatic wise, what are you seeing? How are you seeing your clients or programs starting to address embodied carbon?
Kai: 13:19
Yeah, so in my world, I work a lot with green certifications, building certifications primarily LEED. And the LEED version 4 building rating system really has been the biggest market driver. You know, up until now related to embodied carbon, in my view.
Robb: 13:41
So people are starting to pay attention in the context of programs? It’s just credits right now that people may or may not go after, but people are starting to look at it. Is that fair?
Kai: 14:00
I would say there’s a growing consensus that overall zero carbon needs to be our goal across the industry. And you know, we’ve heard that from architecture 2030 who stated that the construction industry needs to be net zero carbon by 2050. You know, sooner is better, but that’s sort of the outer goal
Robb: 14:24
And are those goals explicitly embodied and operational carbon?
Kai: 14:30
That’s right. Yeah. So we’ll be looking at both those pieces. Yeah.
Robb: 14:33
Okay, cool. Nice. And Catherine, what are you seeing on the policy side or among clients about interest in embodied carbon? Or what would you like to see maybe is another question that’s a different question.
Catherine: 14:52
One of the most Important things at this point that we could do when we really look at embodied carbon is to make a shift in our priorities from building new buildings as the first thing that we want to do all the time to renovating existing buildings as the first thing we want to do all the time. Because it’s a very simple and obvious thing, that if you don’t take down a building and build something else in its place, or even just build a new building, but especially if you, if you take an existing building and you dismantle it, and you destroy it and build something else, it’s obvious how exponentially more embodied carbon you are putting in the atmosphere at that point. It’s tremendous and we really can’t afford to do that anymore.
Robb: 15:55
Yeah. This is a huge issue on, I mean we’ve all run into that I’m sure with clients who want to build new rather than renovate and it’s much harder. I mean we were talking about insulations, Catherine with, you know, foam insulations having a lot of advantages. Starting from scratch with new construction makes it easier to, you know, get good efficiency, get accessibility, durability, resiliency, all of those are easier when you start from scratch. But this is a huge deal about the embodied carbon of that construction.
Catherine: 16:38
Well, I think one of the misconceptions that should be dispelled is that older buildings are automatically less efficient or have considerably less capacity to achieve high efficiency, high performance. I think that what we’re showing more and more now is that in fact, we can make older buildings high performance, high efficiency. And you have to get into also a discussion, which we don’t have time for here, about what age of buildings, because over the past hundred years, construction methods have changed Radically, scale has changed radically. And, and there, there’s a different approach for each era of building. But for example, you, you will find that it is often easier for pre-war buildings to be brought into a high performing status than some 50s through 70s buildings.
Robb: 18:09
So pre-war we’re talking about New York city before world war II generally. Yup. Pretty clear demarcation in the city. Okay.
Catherine: 18:18
But at the same time there is now a lot of work afoot to figure out how to make those 50s through 70s buildings be retrofitted to perform well. One of them, there’s a lot of focus of course on curtain wall now because are going to have to deal with aging curtain walls. There is also options like a interior storm windows that people don’t necessarily know a lot about yet. But these can be operable and you can even have basically interior curtain wall replacement that that prolongs the life of your, your curtain wall building and gives you a huge bump in performance.
Kai: 19:15
Just sort of mulling over the existing building conversation, it’s real interesting. I’m thinking about why building owners may opt to keep the building instead of tearing it down and building new. And I imagined that one of the drivers is cost. It’s more cost effective to reuse these buildings in certain instances. And it makes me think of something that our clients often ask us is, you know, they ask for a life cycle assessment when they really want a life cycle cost analysis. And you know, I think what they’re looking at is, okay, well what materials are we going to use, how much is it going to cost us, how long are they gonna last, this sort of thing. And you know, both employ this like life cycle approach where the lifecycle cost, the LCC is the direct monetary costs for a product or service. Whereas the LCA is the environmental benefits and they actually can, if you’re doing lifecycle costing, you’re not so far off from doing a lifecycle assessment too. You’re collecting your materials, you know, how much material quantities you’re using. And it’s, it’s not so difficult to to transpose those into the environmental benefits. And I hope that more of our clients start asking for that.
Catherine: 20:48
We’re watching buildings get torn down every, every day. It’s it’s really time to start thinking about the fact that buildings aren’t disposable. We really have made this in our minds into a disposable product. And it’s not. And the poster child for this as far as I’m concerned would be 270 park Avenue, which is a high rise, international style commercial building, a skyscraper that is being torn down as we speak. It is the largest such demolition at least ever in New York City. And it may be in the nation or the world. I am honestly not sure, but it is being demolished in order to make way for a new larger skyscraper. And if somebody analyzes what kind of embodied carbon hit this represents, I think that this ought to become what the demolition of Penn station was to the historic preservation movement. It’s a wake up call that we can’t afford to think like this because we won’t achieve our goals if we continue to do this.
Robb: 22:37
Thanks to Catherine and Kai, and again, I urge you to visit the show notes page. There’s lots of resources. There’s links to the embodied carbon network, the relatively new EC3 tool, architecture 2030, several reports, blog posts about embodied carbon, about historic preservation. We decided to link to all these in the show notes rather than have Catherine and Kai rattle them off in the audio. Also go to nesea.org to Check out the building energy Boston conference if you can. March 23rd to 24th 2020. One may be sobering note since we recorded this, according to Wikipedia, at least we confirmed that 270 park AVE is indeed the tallest building ever to be voluntarily demolished in the history of the world. So sorry, we’re not ending on a high note.
Speaker 2: 23:38
Thank you for listening. Buildings and beyond is produced by Steven Winter Associates. Visit Swinter.com for more info on us, visit swiner.com/podcasts to get to all our episodes and to see the show notes and visit [inaudible] dot com slash careers to see job openings. We have quite a few across all our offices, Connecticut, New York city, Washington, D C and a new office in Boston. I’ve been here for just about 20 years now and it’s pretty amazing working with brilliant people who really care about making great buildings, improving sustainability, accessibility, health, affordability, durability. It’s a pretty fantastic crew. Thanks to the podcast team here. Alex Mirabile. Heather Breslin, Dylan Martello, Jayd Alvarez, Kelly Westby, and I’m Robb Aldrich. Thanks for listening.