- March 17, 2016
- 0 Comments
- In Existing Building Performance
- By
In our first entry of this three-part series, we described advanced controls for electrically heated buildings, combined heat and power systems, and upgraded atmospheric boilers. This time around, we’ll examine the ins-and-outs of exhaust ventilation in multifamily buildings.
Why Ventilate?
Many multifamily buildings do not consistently provide tenants with adequate fresh-air. Nearly all buildings require mechanical ventilation and fans to effectively exhaust pollutants generated from bathrooms, kitchens, and material off-gassing. At the same time, pulling in and filtering outside air reduces contaminates and allergens in homes which improves occupant health and comfort by limiting exposure to mold and moisture. However, many systems are noteworthy for rampant inefficiencies in their operation resulting in sub-optimal performance. Below, we introduce three measurement tools, discuss methods of duct sealing, and explore the economics of full cleaning, sealing, and balancing systems, and alternate low-cost solutions.
Velocity Traverse
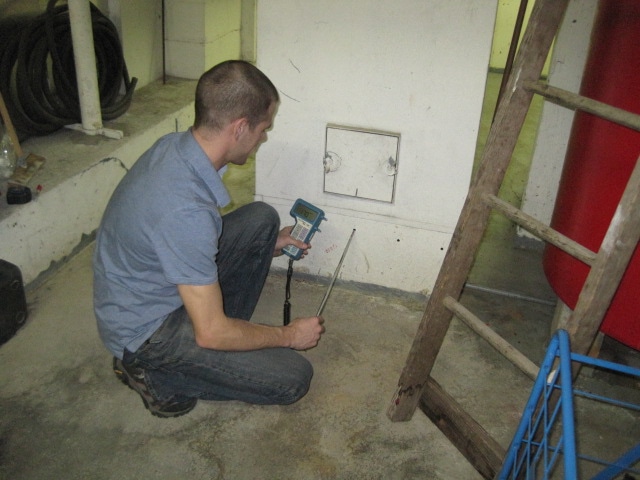
Velocity Traverse
In some multifamily buildings, a plenum, mechanical room, or attic on the top floor allows access to a straight section of ventilation duct near the roof. There, one can directly measure total duct airflow using a velocity traverse. This test measures airflow at multiple points on a cross section of duct, with the average multiplied by total duct area to calculate the total flow rate at that point. Since the 2008 implementation of modern mechanical codes, many buildings originally designed to 1968 code standards are substantially over-ventilated, providing a strong opportunity to right-size ventilation loads for improved energy efficiency and optimized air quality.

Duct Leakage Tester
Duct Leakage Tester
A powered duct leakage tester is a common piece of testing equipment that simulates the performance of the existing fan for flow measurements. If the ducts are airtight, the static pressure created by the tester should be equivalent to the amount of pressure that the fan typically exerts.
Capture Hood Method
The powered flow hood uses a large, air-impermeable tent to corral airflow and a calibrated blower fan to measure airflow. Air blowing out of the roof fan will inflate this tent, then the blower is run until the tent deflates and there is zero pressure difference from inside to outside the tent. Airflow coming out of a roof fan, which is normally extremely difficult to measure directly due to its swirling, uneven pattern, is allowed to organize and enter the blower for a relatively straightforward measurement. The advantages of this method include:
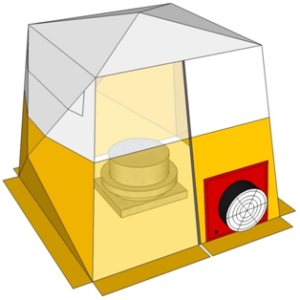
SWA’s Hood Capture Method
1. A faster and simpler set up than other methods, requiring minimal equipment.
2. Very large fans can be tested, limited practically to the capacity of the blower fans used.
3. No access to either mechanical rooms or apartments is required for this method, and fans can remain in place and operational during the entire procedure.
Of these methods, SWA prefers the roof fan tent for quick and easy exhaust flow estimations on a large multifamily building. We have used this tool to assess the total airflow coming from 20+ roof fans on a 17-story building within three hours with two staff. Within that timeframe, most auditors can make a valuable economic assessment of any ventilation retrofit. Measuring exhaust flow efficiency and duct leakage in tandem allows for whole system optimization and synergistic operational benefits.
Duct Sealing Methods
Typical ventilation retrofits require duct sealing. Methods range from manually applying mastic, mastic-backed tape, and other sealants, to using remote-controlled robot mastic sprayers and automated processes such as AEROSEAL, a proprietary process that consists of applying particles of sealant suspended in air and injected into pressurized ducts. Often, a retrofit will use a combination of several methods.
Economics of Whole Building Exhaust Ventilation
The economics of ventilation retrofits are not always straightforward and are best approached conservatively. Estimated ventilation retrofit costs for the New York market range from $350-$700 per register for materials and labor, with larger and more complicated buildings representing the higher-end. Getting to high performance can mean a substantial investment for some systems, and justifying the retrofit on the basis of energy savings alone will probably work only in significantly overventilated buildings in cold climates with expensive fuel.
Low-cost Alternatives
While a full cleaning, sealing, and balancing approach may be beyond a project’s budget, there are less expensive options. Short of a full retrofit, here are the things that every auditor should consider, in rough order of importance:
1. Fix the biggest problems first. Target poor connections at the roof curb, duct disconnects, and faulty workmanship from past duct repairs
2. Seal every crack or gap in the system. Focus on eliminating gaps at the final connection between register boot and apartment drywall.
3. Reassess the size of fans. It’s often possible to find out what ventilation rate they were designed for by looking up the fan and motor nameplate info, and consider replacing the fans if they are oversized for current needs.
For more on this topic, read the article by Sean Maxwell and SWA’s Marc Zuluaga in the August 2015 edition of Home Energy Magazine.
In the final post of this series, we will cover energy storage and low-flow fixtures. If there’s something in particular that you’d like to hear about, leave us a suggestion in the comments below!