- April 11, 2017
- 0 Comments
- In Existing Building Performance
- By Steven Winter Associates
New York City has established high goals for CO2 reductions as part of the 80 x 50 plan enacted under Mayor de Blasio’s administration. In short, NYC aims to reduce its CO2 production by at least 80% by 2050 (from a 2005 baseline). This requires vast energy conservation and renewable energy production proliferation across the city’s energy, transportation, waste management, and building sectors. Buildings themselves account for 68% of current CO2 production in the City, and as such have the largest reduction targets1. Goals can only be met by implementing repeatable and scalable scopes of work in coordination with policy updates and improvements in other energy sectors. To better understand the efficacy of these moderate improvements on overall energy consumption, we’ve analyzed the results from a recent portfolio rehabilitation. These findings help us to create a map of where we need to go in order to approach 80 X 50.
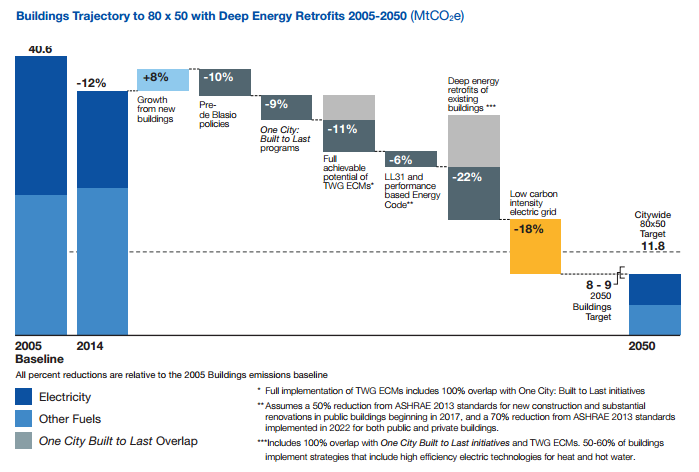
Figure 1: 80 x 50 NYC Buildings CO2 Reduction Goals, NYC Mayors Office of Sustainability, Roadmap to 80 x 50 Report
Portfolio Background
The analyzed portfolio consists of 18 affordable multifamily residences in the Morrisania and Morris Heights neighborhoods of the Bronx. The buildings had not received upgrades since undergoing gut renovations in the early 90s. The building typology is one common to the outer boroughs – four to five story walk-ups, which have undergone modest rehabs in the past, such as batt insulation in exterior cavities, but are in need of comprehensive rehabilitation in order to meet energy efficiency goals.
The year and one-half long moderate rehab project sought to greatly improve the quality of life for residents, while improving the energy efficiency and resiliency of the properties. A broad scope of energy efficiency measures was implemented in each building in concert with NYSERDA’s Multifamily Performance Program (MPP). The scope included high efficiency sealed combustion boiler plants, variable speed pumps for space heating hot water distribution, innovative outboard closed cell spray foam to bring the roof up to energy code while providing air sealing, ENERGY STAR® appliances, and building wide air-sealing. Additional energy efficiency measures, such as LED lighting, thermostatic radiator valves (TRVs) for apartment baseboard convectors, and low-flow water fixtures were installed through Con Edison’s direct install program.
Targeted energy savings ranged from 15% to 25%, but how did they actually perform?
Post-Retrofit Utility Analysis
Steven Winter Associates (SWA) compared 2012 and 2016 owner-paid utility data to see how well the buildings are performing after the rehab. (Resident electrical data was not included in this analysis as residents are direct metered for electricity.) The primary point of comparison is weather normalized energy used for space heating and domestic hot water. Fuel usage intensity (FUI) is measured in kBTU per square foot of building floor area used for space heating and domestic hot water since management pays for space heating and domestic hot water (DHW). Figure 2 shows the 2012 and 2016 FUI for each building in the portfolio. FUI improved by 35% on average, and it is worth noting that each building converged quite closely on an average post-retrofit 57.5 kBTU/SF.
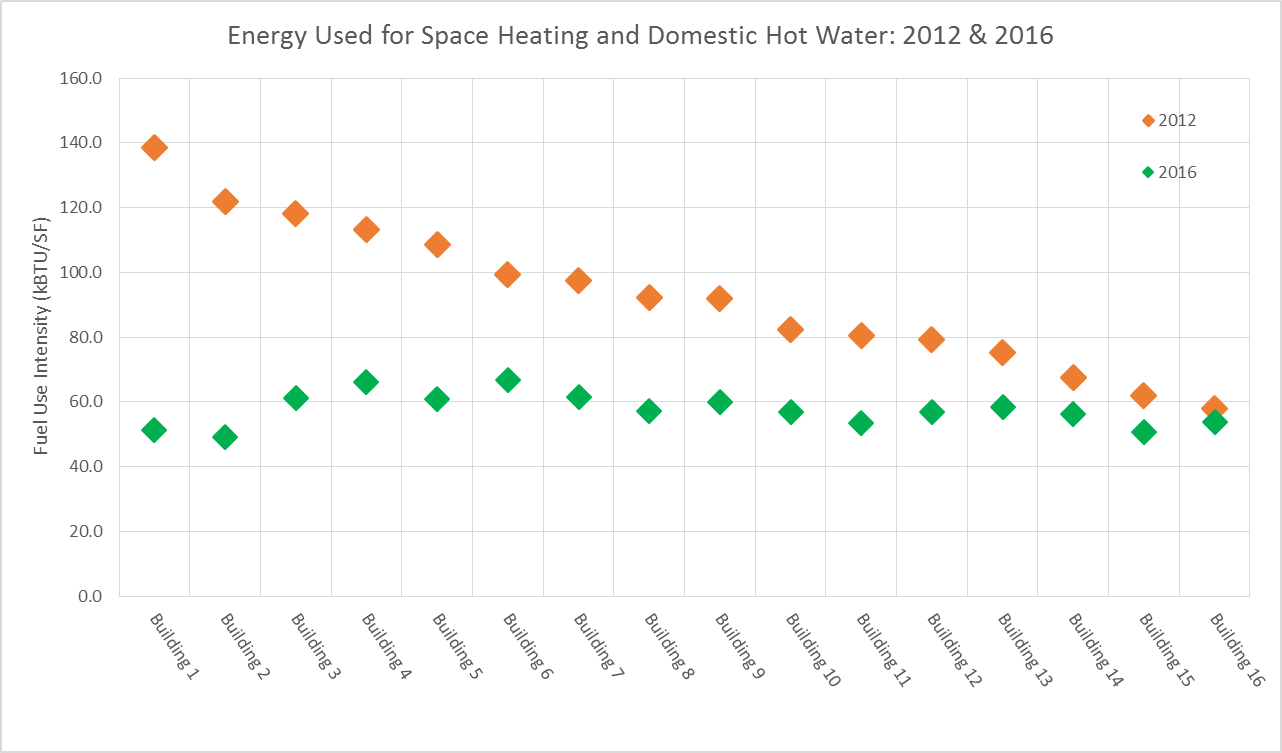
Figure 2: Energy Used for Space Heating and Domestic Hot Water, 2012 and 2016, Year 15 Portfolio
Note: Three buildings were combined into one heating plant, thus 16 buildings are shown instead of 18
What Does This Mean?
As we can see, the savings for these buildings are impressive given the modest scope and broad application. What is most intriguing is the precision with which these buildings approach similar FUIs.
It is encouraging that moderate rehabs can incorporate energy efficiency at a portfolio-wide scale and see 35% energy reductions based on a mix of standard retrofits (in the case of sealed combustion boilers) and new technologies (in the case of the closed cell spray foam roof insulation). Designers and contractors understand how to implement these technologies, and are doing so consistently. The next step is to incorporate next level technologies for energy efficiency as identified by the Mayor’s One City Built to Last Technical Working Group in order to approach our 80 x 50 goals.
Written by Bryan Simpson, Mechanical Engineer