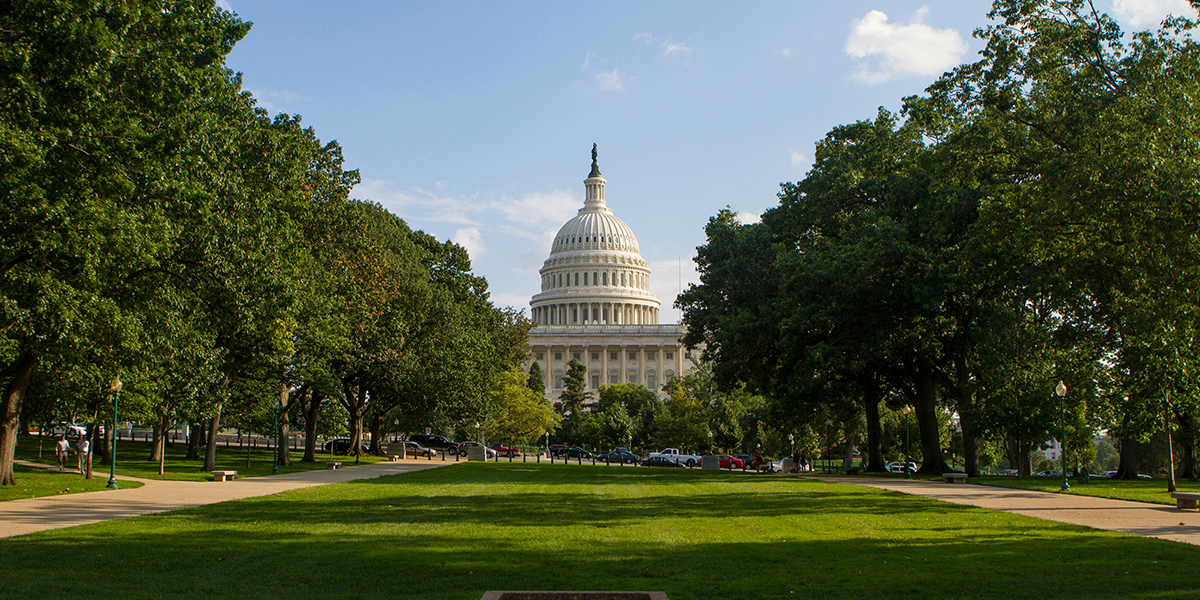
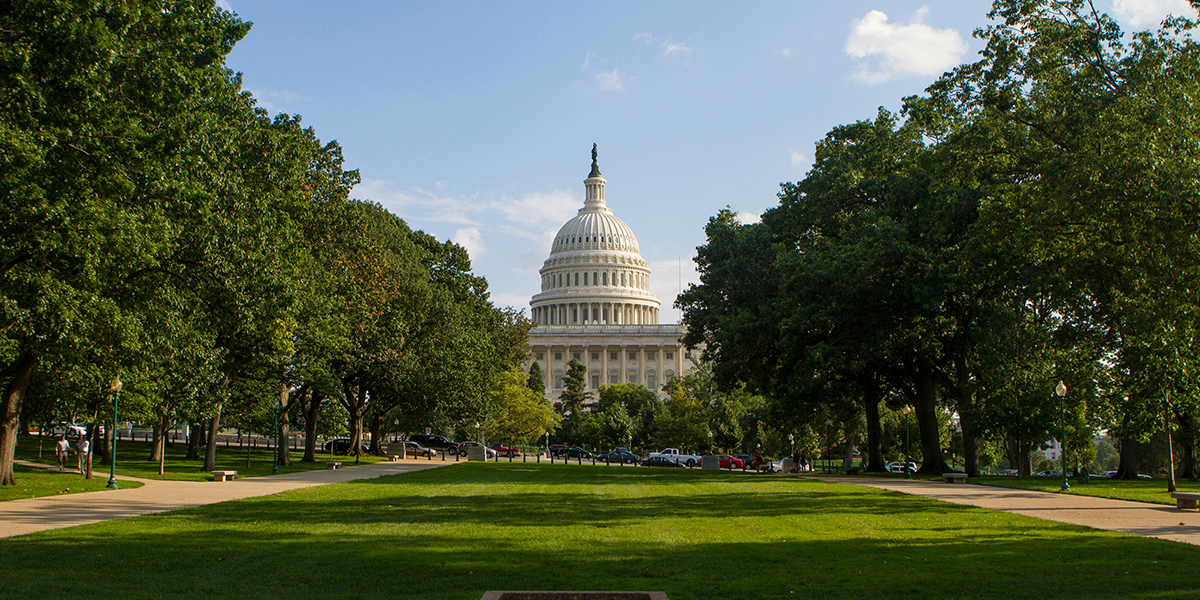
Blog
We like to say that a building is not sustainable if it does not sustain the health and wellbeing of all its occupants. This includes considering how the materials, technologies, and building systems affect indoor air quality, comfort, and the physical and mental health of those utilizing the space.
We like to say that a building is not sustainable if it does not sustain the health and wellbeing of all its occupants. This includes considering how the materials, technologies, and building systems affect indoor air quality, comfort, and the physical and mental health of those utilizing the space.
In our post-COVID world, it also includes how a building can protect its occupants from viruses and other airborne illnesses.
We’re sharing real-world examples of how SWA consultants have helped to mitigate potential negative impacts on occupant health in high-performance buildings.
Keep reading to learn about:
RELATED POST: Sustainable Buildings Are Healthy Buildings: How to Design and Maintain a Healthy Built Environment
When we work on projects with sustainability and efficiency goals, we encourage the developer, architect, and other members of the project team to consider how their choices will impact building occupants. If there are any potential negative impacts, these issues should be addressed as early as possible.
In Passive House buildings, the envelope is designed to be airtight and mechanical ventilation systems introduce fresh air and exhaust stale or contaminated indoor air.
Without a correctly functioning ventilation system, energy performance of the building as well as indoor air quality and occupant comfort all suffer.
Commissioning engineers ensure that a building’s energy-related systems perform efficiently, reliably, and maintain occupant comfort. They advocate for building operators and incorporate lessons learned from other buildings so that a building maintains its performance over its lifetime.
The following are common issues that our commissioning engineers must address in Passive House ventilation systems.
Key ERV Setpoints: Airflow, Static Pressure, and Supply Air Temperature
If there are central energy recovery ventilators (ERVs) that run 24 hours a day or at a constant volume, it’s the installation that takes care of everything. They can easily be installed properly and run smoothly depending on what other interlocks they may have. But if they need to interlock with say, a heat pump, that adds another layer of complexity.
For variable air volume ERVs, at design phase, the engineer must include the key set points needed by the installer and the testing and balancing contractor such as the minimum and maximum airflow, the duct static pressure (and its sensor location), and the supply air temperature set point.
Other ERV Setpoints: CO2 Concentration and Schedules
If it’s a variable volume ERV, chances are it’s serving different variable air volume (VAV) boxes or ZRT boxes, for example, in amenity spaces within a residential building that are not supposed to have ventilation 24/7.
The sequence of how those VAVs modulate needs to be clearly communicated in the drawings and the specs and confirmed during the submittal review phase. If a VAV box is going to be controlled by a CO2 sensor, what’s the CO2 level that triggers it? What is the CFM level that the VAV is going to modulate to? And based on those changes, what’s the static pressure that the ERV needs to maintain?
If it’s a time clock that will control the VAV, that needs to be shown in the mechanical drawings and electrical drawings, and it’s critical to identify the responsible trade. Because it’s in the mechanical drawings, is the HVAC subcontractor responsible for installing that? Or is it the electrician? Or is it a split of both?
ERV Sensor and Controller
Another common issue with variable ERV systems is that if they are variable volume and they need to maintain a duct pressure set point, the sensor must be installed in the right location and wired to the controller. The controller must also be set up to maintain that duct pressure.
Prior to final testing of these units, we request the Testing, Adjusting, and Balancing (TAB) reports. When it’s a variable air volume ERV and there’s no static pressure set point noted in the TAB report, that’s a red flag. We can tell right away that it was not balanced correctly. The balancer and HVAC contractor need to return and make the adjustments prior to testing.
Other times, there is a static pressure set point noted on the TAB report, but when we show up on-site and the controller looks like the image below on the left, both supply and exhaust fans are working to maintain an airflow, but there is no duct static pressure sensor installed, whatsoever! And no one knows how that set point made it into the report.
Read more: What Can Go Wrong with Passive House Ventilation Systems—and How to Prevent It
Not only has the 2021 International Energy Conservation Code (IECC) made significant progress with reducing carbon emissions, it also requires mechanical ventilation and air infiltration testing—which means that air coming in and out is quantified and controlled for optimal indoor air quality.
In most cases, building code sets the bar for new construction and renovation projects. The problem is that states can be slow to adopt progressive codes.
Industry professionals who embrace voluntary sustainable building programs, such as ENERGY STAR®, LEED, NGBS, and Passive House are ahead of the code curve. But how does the rest of the industry get there?
Step 1: Install a continuous air barrier that aligns with the thermal barrier (insulation). Pay attention to air sealing, including compartmentalization in multifamily buildings (i.e., unit to unit, unit to corridor, etc.). Engage an energy rater early in the design process and perform preliminary testing during construction to inform where air sealing needs to improve before things are closed-up.
Step 2: After choosing high-efficiency heating and cooling (HAC) equipment, focus on the delivery system. If ducted, keep the runs simple, short, and fully duct the return side to the air handler.
Squeezing a heat pump into a ceiling cavity almost always leads to construction sequencing issues and poor installation. For example, the return duct to this heat pump was designed to be fully ducted. Return air should pass through the return grill and filter, then directly to the equipment.
Unfortunately, that didn’t happen here. The drywall was completed before the mechanical rough-in was done, so by the time the installer tried to finish the sheet metal return, the space was too tight. Instead of a nice clean return duct, the air path is through a cavity full of dust and debris.
This often also results in the drywaller becoming a duct installer too, as the drywall is used for much (or all) of the return air pathway. This almost always introduces additional duct leakage into the system, which is never a good thing.
Another issue with this design is that we commonly see the heat pump in the ceiling cavity of the bathroom. While this makes sense if the unit has any moisture leaks (the units are commonly installed above a bathtub, or at least a tiled floor), it means that every time an occupant takes a shower there is a considerable amount of humidity introduced to the HAC unit.
During the summer when cooler temperatures are desired, condensation can form on the units and the access panels during operation, which can be a nuisance at best or an on-going maintenance issue and resident complaint that can be very difficult to solve.
Installing non-ducted HAC systems is one way to avoid these issues. However, some options, such as mini-splits, lack good filtration. Better filters will only go so far in providing a healthy living environment. Non-ducted and partially ducted returns will continue to introduce contaminants (insects, rodents, and the air pollutants they produce, etc.) into HAC systems, decreasing indoor environmental quality, reducing efficiency, and potentially causing maintenance issues.
When it comes to healthy buildings, it is easy to get lost in overly technical solutions to providing clean air. However, one of the most overlooked issues when it comes to maintaining healthy buildings is also one of the simplest: maintenance access.
It may seem like a quick fix, but many of the access issues identified by our commissioning team remain unresolved by the end of the project. It is not uncommon for us to hear from teams, “Who cares if it’s difficult to access a filter if it can be accessed?” But it is not enough for access to just be possible; it needs to be easy. The more barriers a piece of equipment has to maintain, the less likely it is to be regularly serviced—and that can have significant impact on energy usage and overall air quality.
Good intentions to provide a healthy building can easily be thwarted by poor maintenance access. This was exactly the case with a large new construction senior housing development in SWA’s commissioning portfolio.
This project placed a high emphasis on providing a healthy building for their residents in design, including accessories for their HVAC equipment, such as air purifiers and steam generators to maintain healthy air quality and comfort levels throughout the year.
While the design team focused on technical healthy building solutions, they failed to recognize that there was limited rooftop space, making placement of the equipment on the roof difficult.
Several large rooftop units serving ventilation air, kitchen exhaust, and temperature control for shared spaces had to be placed on shared roof space. Each one of these units has an outdoor air filter that needs to be changed regularly by maintenance once the building turns over.
Access to these filters requires a door to be opened and maintenance staff be able to pull the dirty filter out completely, and then insert the new filter without bending or damaging it.
During testing, our team found around half of the units on this project had very limited to no access to the filter. Access issues ranged from mild obstructions, such as condensate drain piping limiting the door from opening completely, to more severe limitations due to ductwork routing.
In both scenarios pictured, the filter is technically accessible. In theory, the cabinet door could be taken off its hinges to replace the filter. This is often the solution that is posed to us by project teams in lieu of moving equipment or rerouting ductwork.
In practice, we know that it is much more likely that the filter will never get changed than it is for a building super to take 20 minutes to unscrew a door just to change a filter.
For this project in particular, the inability to change the outside air filters negates all the effort (and money) that went into acquiring the air purifier and humidifier accessories for these rooftop units.
We know from warranty walkthroughs and our experience in existing buildings that access issues in new construction turn into maintenance issues during building operations. It is crucial to stress maintenance access early on to prevent costly and sometimes impossible fixes.
To create a sustainable and healthy building, consider occupant health, wellbeing, comfort, and safety at every step of the design and construction process. Human health should never be an afterthought.
Click here to learn about 550 Madison Avenue, New York, NY—a project prioritizing health and pursuing WELL Gold certification. SWA is proud to be part of the project team as the WELL consultant.
Click here to contact SWA and connect with a healthy buildings expert.
Contributors:
Commissioning Passive House Ventilation Systems
Luis Aragon, Senior Building Systems Engineer on SWA’s Building Operations, Decarbonization, and Efficiency Team; Michael Schmidt, Senior Building Systems Consultant on SWA’s High-Performance Building Solutions Team
Installing Heating and Cooling (HAC) Systems with a Fully Ducted Return
Karla Butterfield, Sustainability Director on SWA’s Sustainable Building Services Team; Alex Guerrieri, Sustainability Consultant on SWA’s Sustainable Building Services Team
Removing Barriers to Maintenance Access
Rachel Harrington, Senior Building Systems Consultant on SWA’s Building Operations, Decarbonization, and Efficiency Team
Steven Winter Associates