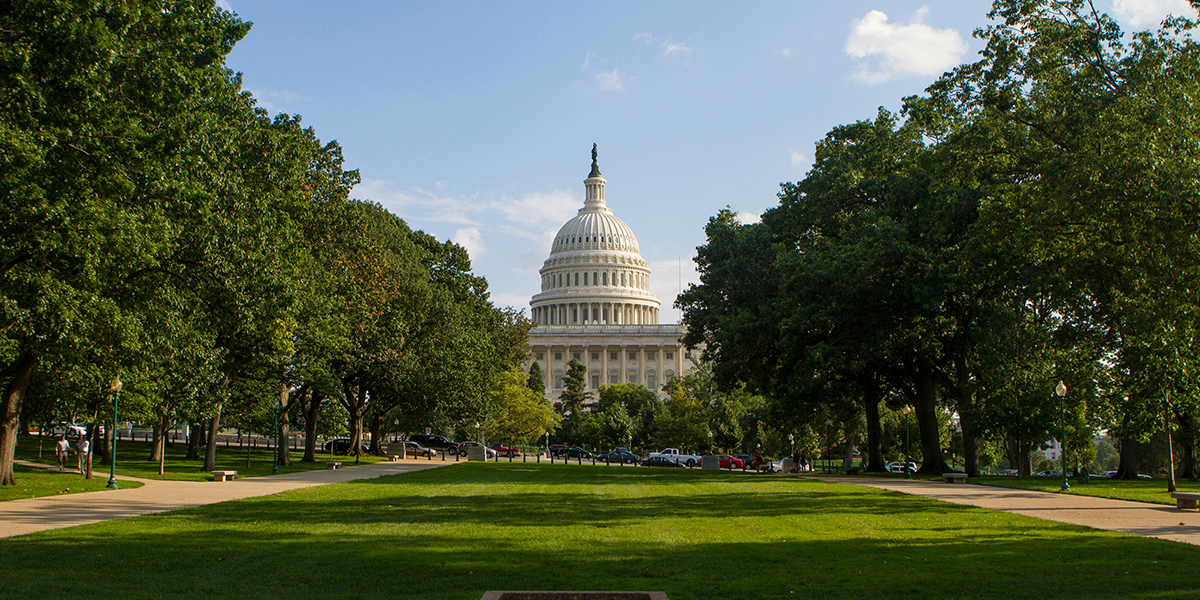
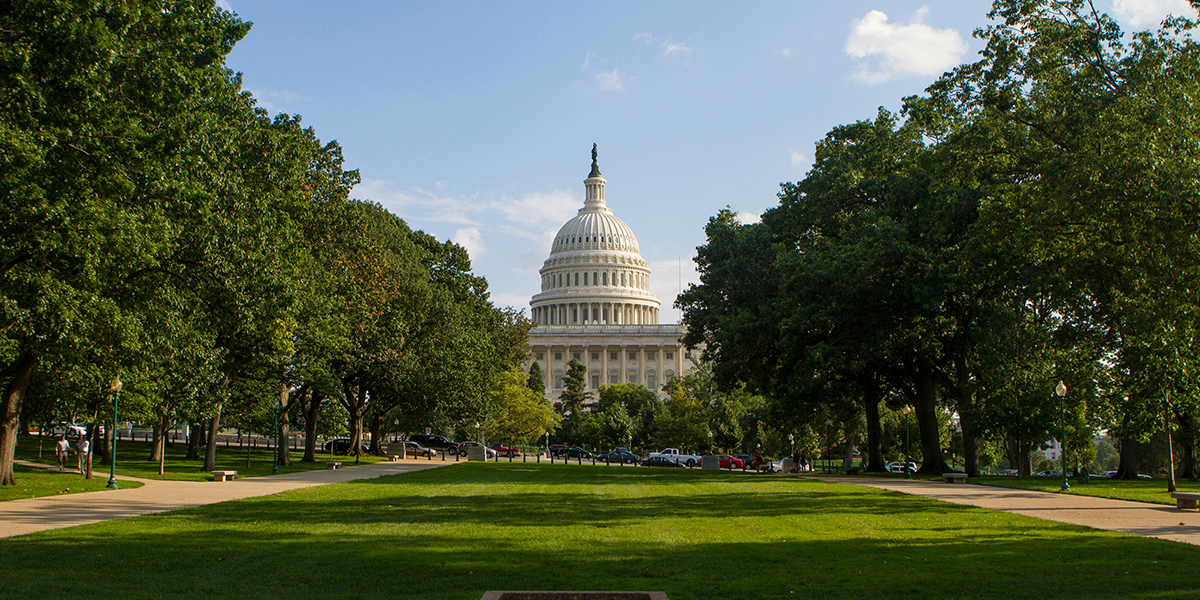
Blog
AeroBarrier is touted as the best route to never fail another blower door test. The technology, which involves pressurizing a space with a blower door fan while misting a water-based glue into the air from multiple points throughout the space, is most often being used on new multifamily buildings after drywall is installed.
AeroBarrier is touted as the best route to never fail another blower door test. The technology, which involves pressurizing a space with a blower door fan while misting a water-based glue into the air from multiple points throughout the space, is most often being used on new multifamily buildings after drywall is installed. SWA first experimented with the technique on the Cornell Tech high-rise building. Back in March, I reached out to Yudah Schwartz at SuperSeal Insulation, Inc. about a personal project, the gut rehab of a 2,500 SF detached single family home. While renovations aren’t something they normally do, Yudah and his team agreed to try a demo. Here’s what happened.
Built in 1924, the home has 2×4 balloon framed walls on top of a rubble foundation. With my husband and fellow SWA staffer Steve Klocke, we did a full renovation targeting an all-electric, LEED Platinum, and (hopefully) near-zero home. We moved in on July 6. The renovation included gutting the home from inside and out, leaving the framing, exterior wall sheathing, and foundation in place. After wrapping the house in 1” of continuous rigid insulation with taped seams, installing U-0.23 ENERGY STAR windows from Paradigm, and replacing roofs and siding, we did our best to address air sealing at critical junctures, such as the connection between the framing, sheathing, and rubble foundation, with sealants applied by hand. Steve lined the basement with poly, creating a “bathtub” and sealing the edges to the framing above. We were a little disappointed to find that our blower door numbers at that stage were 5 ACH50 with the interior still gutted.
We used spray foam in the roofs, rim joists, and a small crawlspace because it seemed like the best solution due to space considerations and moisture management. For the walls, though, we were hoping to do something with a smaller material footprint. For health and carbon reasons, we preferred low-emitting mineral wool batts in wall cavities; but how to fix the leakage? At this point, we started exploring the possibility of an AeroBarrier application.
The technology uses a water-based acrylic “glue” that is Greenguard Gold rated for low emissions, and mechanical fan pressure as the “propellant.” Over a period of time (usually 1-3 hours), the fans drive the misted sealant toward the leaks, sealing up openings from the size of a human hair up to ½ inch. The process is automated, and watchers can see the rate of application and the reduction in cfm of leakage in real time. The technicians monitor the pressure and other factors while the software automatically adjusts to the building conditions, including humidity, to make sure the glue can dry sufficiently.
The AeroBarrier product ticked our boxes for low embodied carbon and healthy materials, but there are limitations to the fan-driven application. Specifically, Mr. Schwartz and his team typically won’t touch a renovation project, because they are mostly too leaky to achieve enough pressure to drive the sealant into the nooks and crannies. In our case, because we had done a blower door test and established our home as not overly leaky, they were confident the pressure would be sufficient to fill the gaps.
Over 20 people (including many from the CT Passive House community) came out to watch a live demo on March 5th. The SuperSeal insulation team prepped the home the day before, taping off all windows (to avoid the sealant finding a tiny pathway and gumming things up) and setting up the misting devices (about 2-3 per floor). After answering questions and letting everyone view the setup, the doors were sealed, and we retired to the garage to watch the action on the monitors. It took about 15 minutes just to build up enough “fog” for the numbers to start changing. Then we started to see the numbers slowly dropping as the sealing happened. We started at 3.32 ACH50 leakage (with windows and mechanical openings taped) and after just over two hours, had reduced the numbers by 50.9% to 1.63 ACH50. We used a little less than four gallons of the sealant. During the process we walked around the outside, feeling for leakage and watching for any telltale vapor escaping. Despite our careful efforts to manually seal the basement, we found the rubble foundation had lots of small leaks. Other hard-to-address junctures: the space where the chimney meets the house; porch roofs connecting to adjacent walls; and the bottom and top of the exterior walls, where the rigid sheathing intersected with the foundation or fascia.
Now that the mineral wool is installed, the gypsum board is sealed, and the trim is on, we are feeling pretty happy to be sitting at 776 CFM50, which is equivalent to 1.6 ACH50. Would we recommend AeroBarrier again? Most definitely. It works well for new construction applications where teams are aiming for code-compliance, but it can also be a crucial tool for renovations to address the tricky intersection of old and new materials. The technology isn’t one-size-fits all, but there may be a place for it in your toolkit whether you are aiming for a one-stop shop to meet code-minimum tightness, or a multi-layered air sealing strategy to get things super tight.
And in case the thought crossed your mind, unfortunately you can NOT attempt AeroBarrier on an occupied home. The sealant leaves a (water washable) film on the floor, which is easily dealt with in new construction but could be a real bear to get out of any textiles in a home. Furthermore, Mr. Schwartz knows of at least one professional in the industry who tried this himself, and ruined his washer and dryer in the process
Contributor: Maureen Mahle, Managing Director, Sustainable Housing Services
Steven Winter Associates