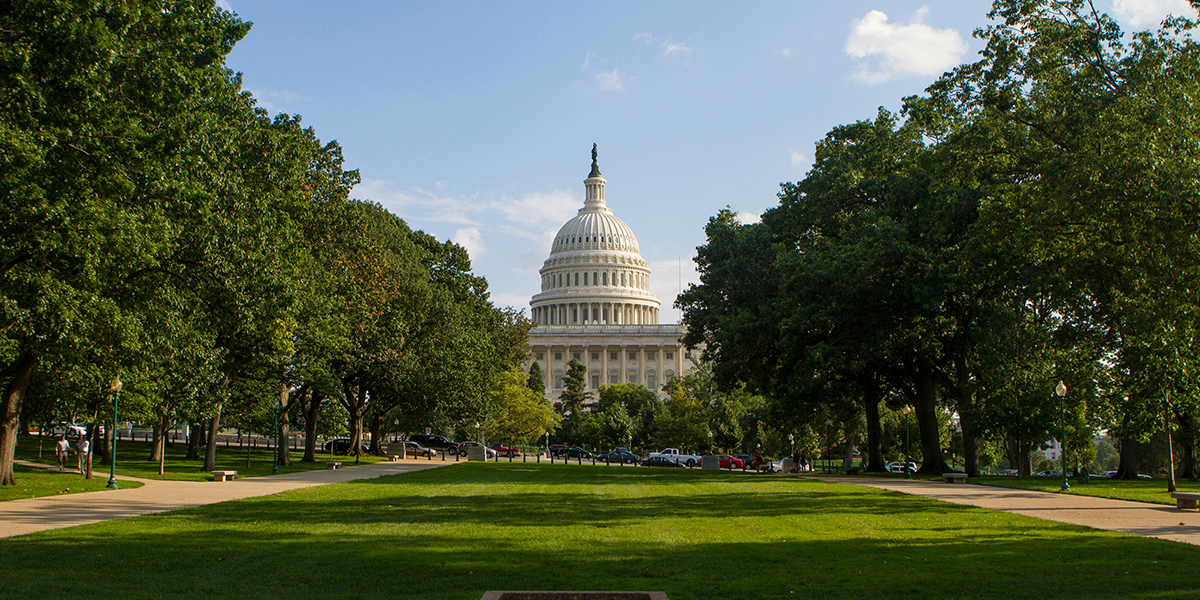
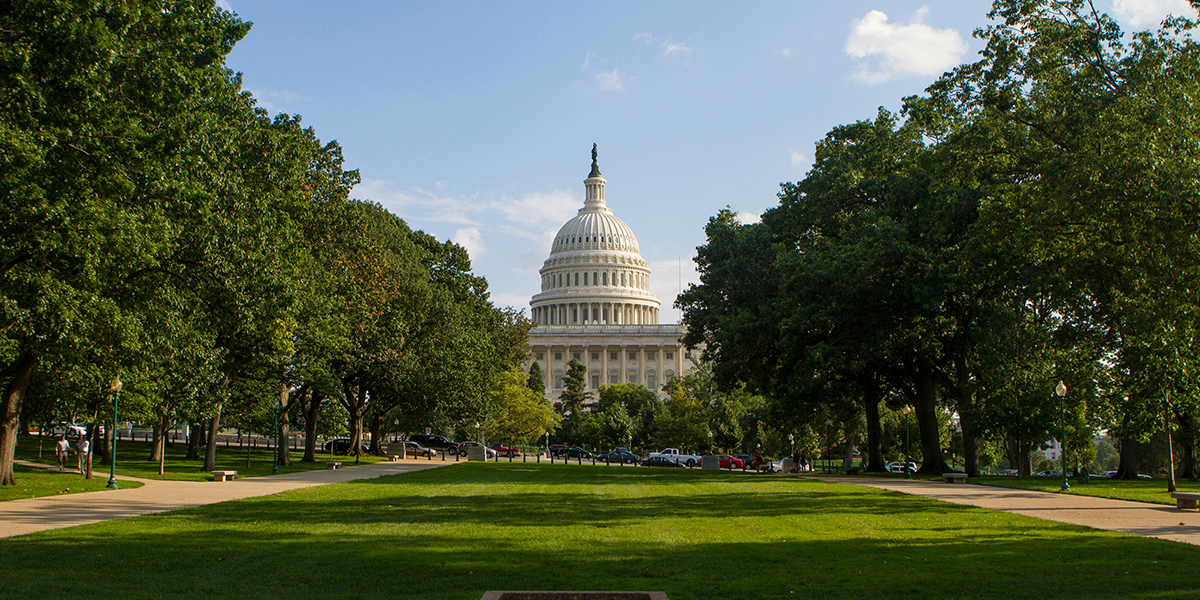
Blog
A whole-system upgrade can fix overheating issues and result in 15-35% energy savings. But what does it take to upgrade an entire steam heating system?
Most people who have lived or worked in a steam-heated building are familiar with the typical occurrences of uneven heat (underheating/overheating), banging pipes, and having to open windows all winter long. Not only are occupants uncomfortable, but the heating bills are high as well.
Balancing these systems is a huge opportunity for energy savings. It is important to point out that the root of the issue is in the distribution system, and it’s that distribution system that needs to be fixed. The steam traps are the weakest link, and when they fail, residents lose the ability to control the amount of heat delivered. This in turn makes the space uncomfortable and results in the necessity to open windows and waste fuel.
The steam traps are supposed to be replaced building-wide every three years to catch broken traps, but due to the expense and logistics of such a task, this is rarely done.
We need to take a holistic approach to fixing and upgrading the steam heating system. This whole-building approach can be broken open into the following components:
In buildings where only part of the above work is completed, results are poor, energy savings is minimal, and comfort issues often persist. The greatest savings and increases in comfort are realized when the entire package of work is installed together.
Systems that SWA targets for optimization are as follows:
Much of the steam heating system imbalance originates with delicate steam traps. The solution is to install orifice plates at all of the heaters which make the traps redundant.
An orifice plate is about the size and shape of a bottle cap and fits snugly into a heater’s hand valve (see figure below). A small hole in the plate restricts the flow of steam so that it all condenses into water and no steam can pass through the heater into the returns.
In addition, orifice plates help balance the system. And once a building has converted to an orifice plate system, the heaters’ output can be reduced by turning down the steam pressure during periods of mild weather. When the heaters’ output more closely matches the building’s actual needs, the system doesn’t need to cycle on and off as frequently and residents experience a more gradual and comfortable heat flow.
TRVs should be installed onto each heater in place of the existing hand valve. TRVs sense room air temperature and restrict the flow of steam as needed to maintain comfort. Each room can be maintained at a different temperature so that every resident sets their own heat.
TRVs work poorly when installed into systems with broken traps, so they have unfairly gained a mixed reputation. When used in conjunction with orifice plates, however, they work extremely well and greatly increase comfort and efficiency.
Air fills the pipes and radiators when a steam cycle ends. When the boiler starts again, the expanding steam must push the air out so that steam can reach the radiators. Air in the main and riser piping blocks the passage of steam and improper venting traps it in place. The farther an apartment is from the boiler, the longer it takes the air to be vented from the supply piping, which results in underheating. This localized underheating causes overheating and opened windows in apartments closer to the boiler.
The solution is to install very high-capacity air vents at the ends of the mains and at the tops of the risers. In addition, any steam traps in the distribution piping must be maintained on a regular basis to remain functional.
All steam heating systems need dry steam—water vapor with few entrained water droplets—to operate optimally. Wet steam causes water hammer (clanging pipes), squirting vents, and water accumulations at the ends of steam mains. Water accumulation blocks steam from reaching apartments; tenants complain, the heat gets turned up, and most of the building becomes overheated.
When the heater and distribution work is complete, detergent-clean or boil out the boiler. Other dry steam measures include limiting the burner’s firing rate, keeping chemical water treatment to the very minimum (or eliminate with anode bars), and lowering the boiler’s water level as much as possible.
Most existing steam heating controls respond only to outside temperature. They have no idea if the apartments are hot or cold, and they overheat the buildings in mild weather. A new modern control that monitors the indoor temperature in multiple apartments and supplies heat only as needed must be installed as well. This results in more stable temperatures, improving the residents’ comfort and maximizing energy savings.
Based on previous experience, the projected energy savings for steam heating upgrades is 15%-35%. The range of savings is dependent upon factors such as pre-retrofit energy use, scope of work details, and post-retrofit building operation.
Construction costs range between $700-$1,500 per apartment. The main variables affecting project cost include the use of in-house building staff labor versus an outside contractor (for apartment work), as well as the extent of the basement distribution work required.
New York City’s Local Law 87 effectively requires steam traps to be replaced at least once every 10 years in order to demonstrate compliance. These comprehensive steam heating upgrades eliminate the need for steam traps at the radiators, allowing LL87 compliance in the simplest and most durable manner.
In addition, this scope of work can support compliance with the upcoming Local Law 97 carbon caps, whether working to minimize on-site emissions to reduce fines or to comply with the prescriptive pathway allowed for rent-regulated buildings.
Contributor: Cathal Gleeson, Principal Mechanical Engineer
Steven Winter Associates