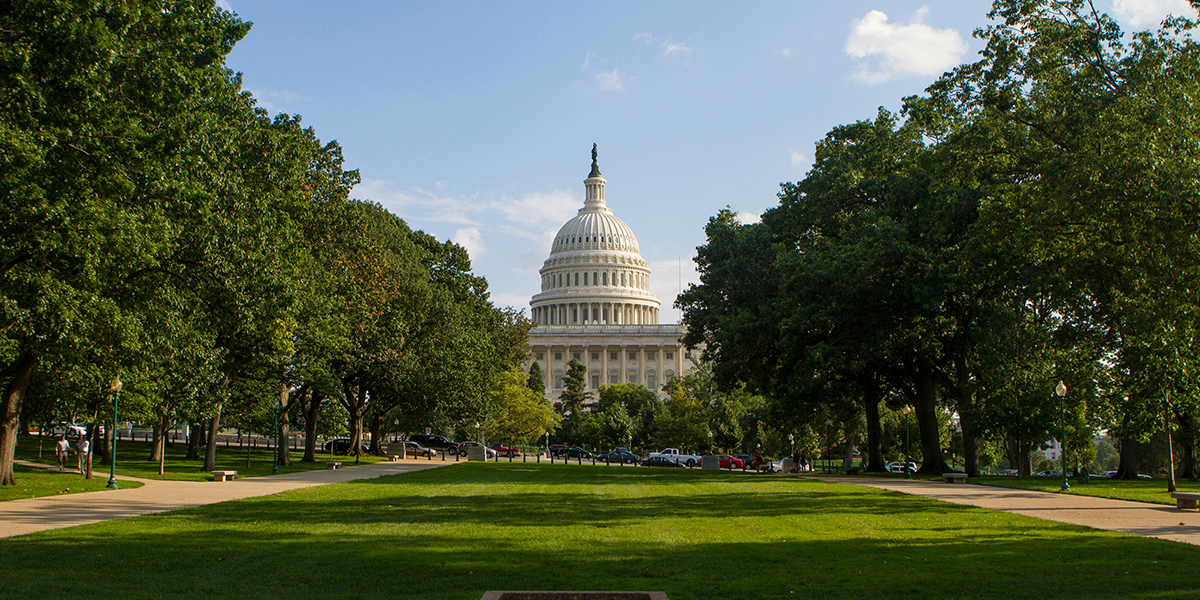
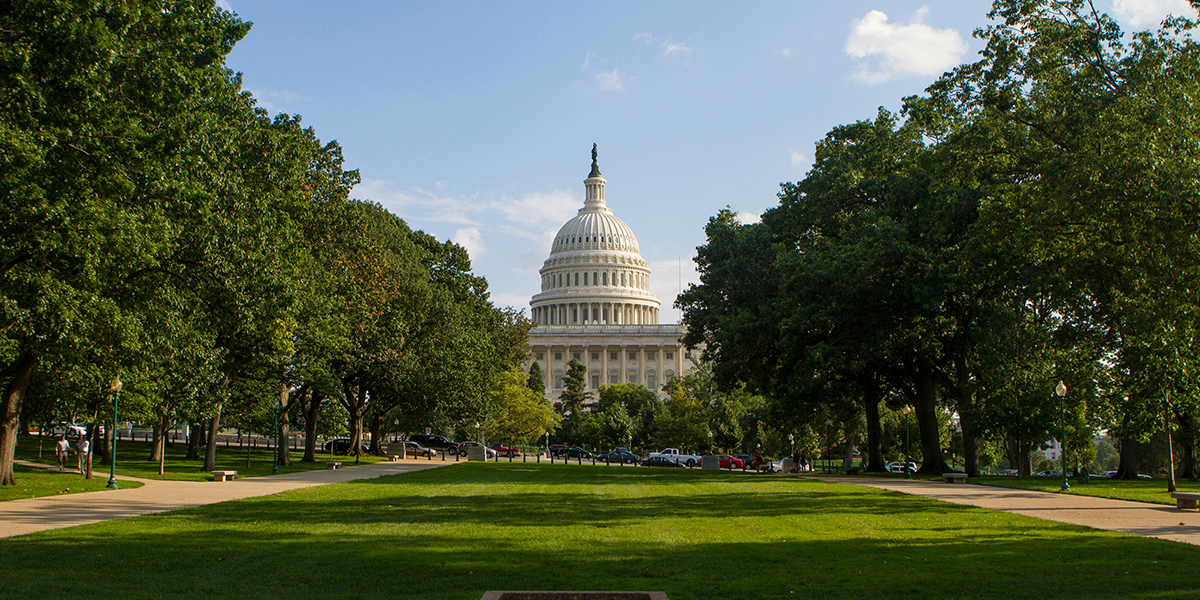
Blog
Passive House design for large multi-family buildings aligns with and builds upon industry guidance for mitigating the spread of infectious diseases.
Passive House design for large multi-family buildings aligns with and builds upon industry guidance for mitigating the spread of infectious diseases.
As the world continues to be turned on its head by the impacts of COVID-19, the building industry has been scrambling to respond, encouraging designers and building operators to learn about how their buildings are being ventilated. Industry experts have produced an array of documents and reports outlining guidelines for reopening buildings safely while minimizing the risk of transferring infectious disease. Much of the focus of this guidance has been on using mechanical ventilation and proper air distribution to dilute contaminant levels in spaces and minimize the spread of viruses. The American Society of Heating, Refrigeration and Air-conditioning Engineers (ASHRAE) has produced a significant amount of guidance for designers. One of their main documents, produced in April, is the “ASHRAE Position Document on Infectious Aerosols,” which provides useful information for how buildings should be designed and operated in response to a pandemic. However, it has prompted questions from design teams about how this might conflict with the goals of very low energy buildings, such as Passive House (PH). This blogpost is written as a response to some of these questions and to highlight the benefits of Passive House design in light of recent recommendations by groups like ASHRAE.
The following are some of the benefits of Passive House design for multi-family buildings compared to code requirements as well as some additional guidance for how to design to mitigate virus transmission.
1. Fresh air minimum filtration requirement
Passive House design requires that all incoming air pass through a MERV 13 filter and that all exhaust air exits through a MERV 8 filter before entering the energy recovery device. ASHRAE has recommended that MERV 13 minimum be used to mitigate the transmission of viruses, so it may be beneficial to design for a MERV 13 filter on both sides of the ERV if cross contamination is a concern. This filtration requirement ensures that only fresh, filtered air with minimal risk of contamination is provided to occupants.
Since the main heating and cooling systems are typically separated from the ventilation system in a Passive House, the filtration on the heating and cooling systems in the common areas in particular is of great importance. This should also be a minimum of MERV-13 per ASHRAE recommendations, although this is not specifically a Passive House requirement.
2. Required fresh air delivery to all living spaces and bedrooms 24 hours a day, 365 days a year
Even when designing a new ventilation system compliant with code and ASHRAE 62.2, it is not required to deliver fresh air directly to bedrooms. Since Passive House certification is focused on both energy efficiency and occupant health and comfort, it requires that fresh air be ducted directly to each bedroom (e.g., not through transfer grilles or undercuts) and remain constant throughout the year. Combining this with the filtration requirement (MERV 13 minimum) and the envelope airtightness, all occupants are provided with fresh, filtered air at all times and do not need to rely on mixed air transferred from adjacent apartments. This strategy is explained further in the following two images. The first image shows a mechanical floorplan in a Passive House apartment building. The duct layout shows fresh air being delivered directly to the bedrooms and exhaust air being pulled from the bathroom and kitchen. The second image shows how this strategy operates in section view, with the use of a proper transfer route so that air can travel within an apartment from the supply to the exhaust spaces.
Additionally, ASHRAE recommends that ventilation systems run 24/7 during a pandemic, which is already a requirement of Passive House design. Since bathrooms and kitchens require a minimum amount of exhaust at all times, PH systems ensure that contaminated air is constantly removed from the building.
3. High level of duct airtightness and tempered fresh air
Passive House design requires that projects design fully balanced ventilation systems (exhaust and supply within 10% of each other) and utilize efficient, highly airtight duct systems to reduce fan energy and maximize effective fresh air delivery to all spaces. To properly balance the system, the ductwork must be airtight and typically requires the use of an injected, aerosolized sealant to fully seal the ducts. This process can be seen in the following image.
It is also common in large scale multi-family dwellings to temper the air leaving the ERV core before it enters the space. This ensures that all spaces receive the correct outdoor air flowrate and that this air arrives at the specified temperature and relative humidity. Controlling indoor relative humidity is extremely important with respect to limiting COVID infections.
It is mentioned in ASHRAE’s position paper (PDF) that viruses are significantly less dangerous when relative humidity is between 40% and 60%. Quoting the paper, “immunobiologists have correlated mid-range humidity levels with improved mammalian immunity against respiratory infections (Taylor and Tasi 2018). Mousavi, Et. Al. (2019) report that the scientific literature generally reflects the most unfavorable survival for microorganisms is when the RH is between 40% and 60%.”An effective air distribution system, combined with an efficient energy recovery core, as is required by Passive House, allows for consistent control of the building’s relative humidity within this range.
4. Increased ventilation system commissioning
Due to the focus on effective ventilation system design and delivery in a Passive House, enhanced commissioning of the ventilation system is required for certification. This means that the final testing and balancing of the system is rigorous to ensure all spaces are receiving the required amount of fresh air, the system is not experiencing excess leakage, and the energy recovery system is functioning as designed. The use of adjustable constant airflow regulation (CAR) dampers is typically required, allowing for airflows to be accurately dialed in and adjusted in all spaces. Additionally, proper sealing between ductwork and drywall is inspected to make sure air is not dumping into walls or ceiling cavities. An example of this properly sealed condition and a CAR damper can be seen in the following images.
If issues are revealed during the commissioning process, they must be corrected before occupants move in or the project will not achieve certification. Therefore, Passive House design offers a degree of confidence in the ventilation systems that most building certification programs do not.
Recent guidance from ASHRAE and other authorities have prompted some misconceptions about Passive House design and how it complies with industry guidance in a post-COVID world. We have noted a few and hope to provide some clarity.
Misconception: The stringent Passive House airtightness requirement will reduce the amount of fresh air occupants receive, which will be harmful during a pandemic.
Clarification: The Passive House airtightness requirement is significantly higher than required by code for multi-family buildings in NYC (at least 4x more airtight depending on the size of the project). This requirement measures the airtightness of the building envelope with all windows and doors closed. However, all living spaces in Passive House buildings must have operable windows and natural ventilation is highly encouraged to reduce energy use. The airtightness requirement does not mean you cannot have open windows. It simply reduces the leakage of air through places you would not want air to come from, i.e., small cracks around your windows and walls. This also helps to prevent condensation and mold growth resulting in a much healthier living environment. In a PH, fresh air is effectively delivered through your mechanical ventilation system where it can be controlled and filtered, reducing the transmission of airborne viruses and providing the much-needed dilution that health organizations are currently recommending.
Misconception: Using an Energy Recovery Ventilation (ERV) system will result in the mixing of exhaust air with fresh air, potentially leading to the contaminated air being spread throughout the building.
Clarification: In ASHRAE’s recent “Position Document on Infectious Aerosols” in response to COVID-19, mention is made that buildings should “bypass energy recovery ventilation systems that leak potentially contaminated exhaust air back into the outdoor air supply.” While this strategy may make sense to use in extreme situations, the danger of cross contamination is very low, especially in a Passive House compliant design. The reason is because the maximum cross-contamination leakage rate allowable for PH certified ERVs is very low and the filtration requirements for both return and outdoor air streams is higher than typically required.
To explain further, ERVs are designed to prevent incoming and outgoing air streams to mix, although a minor amount of leakage is unavoidable. For a Passive House certified ERV, this leakage must be less than 3%. In addition, Passive House requires that a minimum MERV 8 filter be installed on the return side of the ERV to filter exhaust air before it reaches the core, minimizing any potential transmission between the exhaust and supply streams at the unit. This may be increased to MERV 13, if desired and with the guidance of the MEP engineer. Additionally, if cross contamination is still a concern, most ERVs are available with a “bypass” capability, where the air stream can be directed around the heat exchanger. In fact, good Passive House design typically includes a system with bypass to take advantage of free cooling when outdoor conditions are favorable. Therefore, most Passive House projects already do a superb job of mitigating the mixing risk, but also have the ability to follow more extreme measures if necessary.
Misconception: Use of demand-control ventilation is counterproductive when trying to reduce virus transmission in a building.
Clarification: Since mechanical ventilation requires fan energy and increases your heating and cooling bills by introducing more outdoor air, good Passive House design pushes projects to reduce ventilation in large areas when it is not required. This means utilizing a system of controls and mechanical dampers to modulate the amount of ventilation supplied to areas with large occupancy swings (such as gyms, conference rooms, and assembly spaces). This strategy is called “demand-control ventilation” or DCV. ASHRAE recommends that building operators “disable demand-controlled ventilation” during a pandemic to allow for more fresh air flow, but this should not be understood as: demand-controlled ventilation is bad design for a COVID responsive design. In fact, if these controls are correctly designed, this type of system can be used to increase airflow when desired during an event such as the pandemic as well as restrict airflow when spaces are unoccupied to conserve energy during typical operation. The following image shows how demand-control ventilation is set up in a typical floorplan for a Passive House project, with CO2 sensors controlling mechanical dampers in both the exhaust and supply ductwork.
It should be noted that studies have shown that an increase in filtration can ultimately be more effective in mitigating risk and can be less costly than only increasing ventilation rates, so designers should not immediately jump to the conclusion that they need to account for massively over-sized ventilation systems as a response to COVID. In fact, a combination of both strategies should be used to achieve the desired reduction in particulate concentration. Additionally, the benefit from filtration tends to level out after MERV 13 filtration, which is why this level is typically cited by ASHRAE and is also the minimum for Passive House design. The following chart illustrates how increased filtration reduces infection risk and levels out after MERV 13. It also shows how increasing ventilation will ultimately result in significant cost increases to the building owner while only providing a minimal additional benefit over the use of filtration.
There is no question that the COVID-19 pandemic has changed how we look at a lot of things, and it is still yet to be seen how the pandemic will affect the way we design buildings in the future. If there is anything that is certain, it is that there is already a renewed focus on ventilation design that hopefully will not go away any time soon. This article points out that designing with Passive House principles reinforces the strategies that should be considered in response to the pandemic, and actually requires much of these recommendations. Therefore, Passive House certification does not conflict with industry guidelines from groups such as ASHRAE and should be seen as a powerful tool in your toolbox for providing a healthier, more comfortable, and safer building in our post-COVID world.
Contributor: Chris Hamm, PE, Senior Building Systems Engineer
Steven Winter Associates