Star Garment Innovation Center
Katunayake, Sri Lanka
Sri Lanka’s first Passive House building
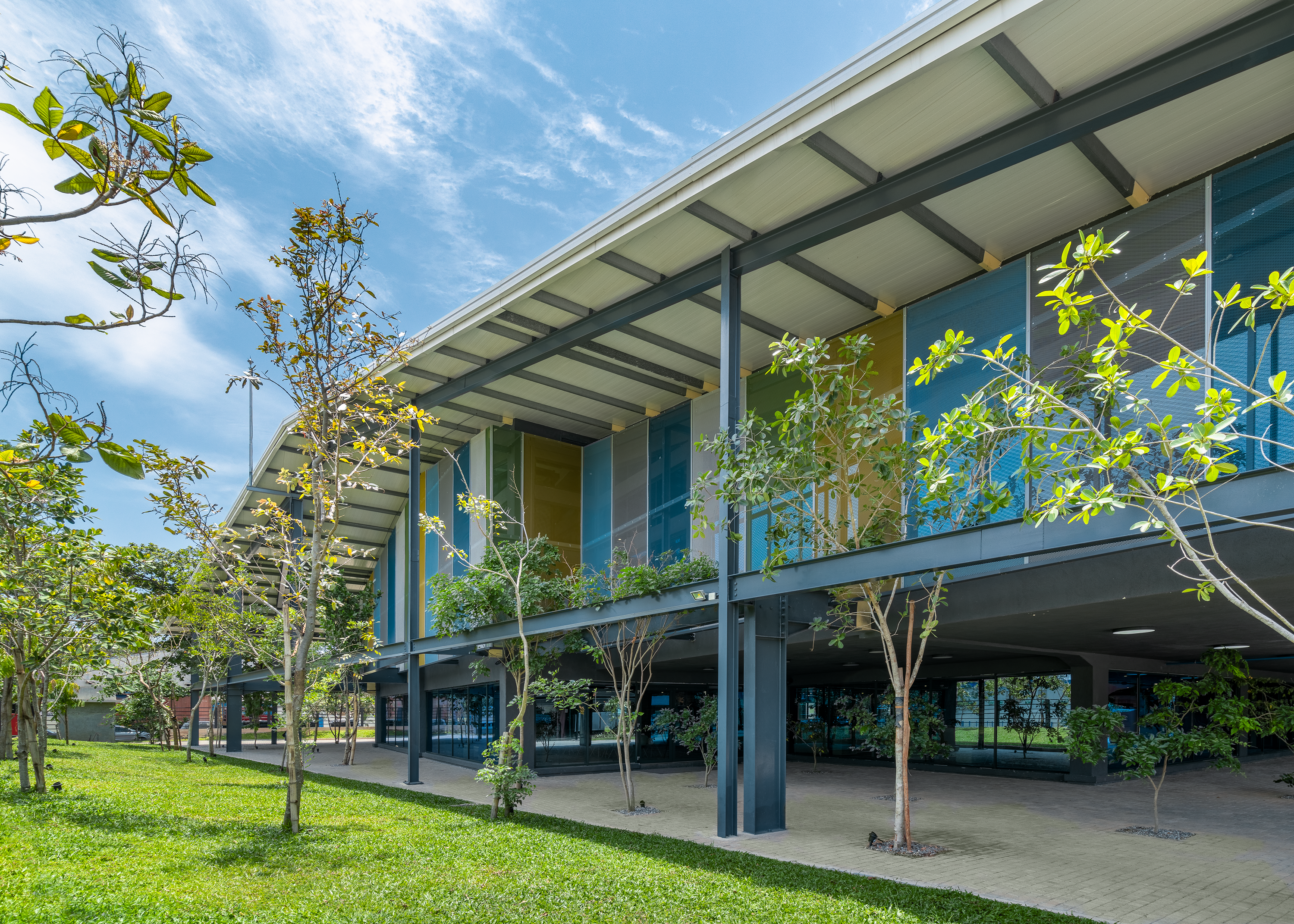
Project Overview
SWA worked remotely with a project team across the world to retrofit an outdated factory in Katunayake, Sri Lanka, and turn it into an EnerPHit Passive House certified garment manufacturing facility.
The team enlisted the guidance of the Passive House Institute (PHI) early in the project’s development to tackle the many complexities associated with the EnerPHit standard – a Passive House certification that was designed by PHI for the renovation of existing buildings.
The project’s location in a hot and humid climate, combined with its use as a manufacturing facility, resulted in a heightened focus on strategies to reduce gains from both the sun and from equipment and occupants in the space. Controlling the humidity in the space is not only essential for Passive House certification, but also for ensuring optimal thermal comfort for the workers.
Building Details
- 111,000 GSF
Project Team
- Architect, Developer & Owner: Becker + Becker
Services Provided
- Energy & Thermal Bridging Modeling
- Mechanical Design Review
- Passive House Design Analysis & Recommendations
- Testing & Verification
Certifications
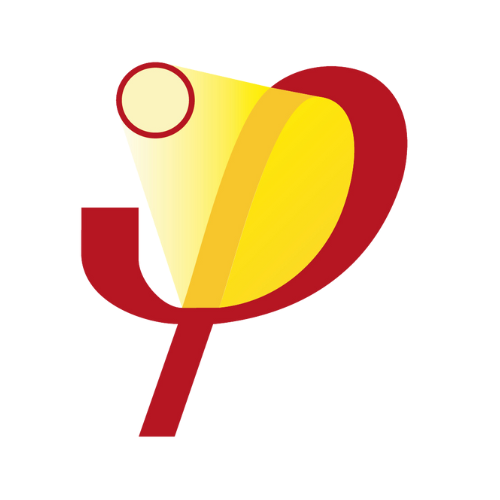
EnerPHit