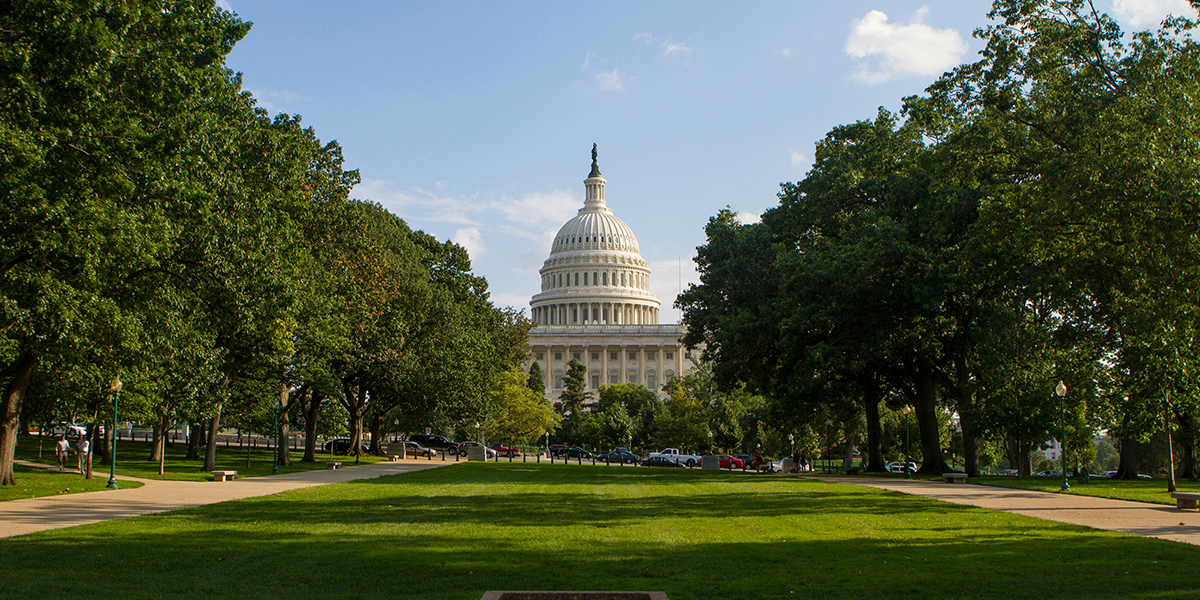
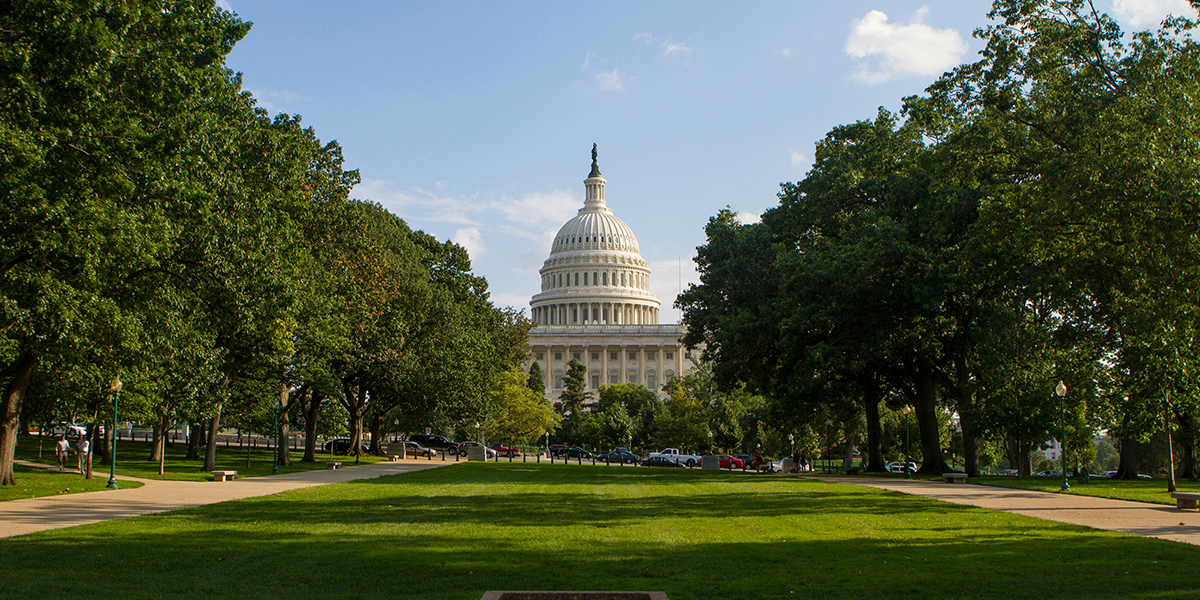
Blog
When ventilation systems are designed correctly, but installed, commissioned, and operated incorrectly, the system ends up being leaky and inefficient and uses more energy than expected.
The envelope of a Passive House building is designed to be significantly airtight. Mechanical ventilation systems introduce fresh, filtered air and exhaust stale, contaminated air 24 hours a day—which is extremely important in maintaining optimal indoor air quality and occupant comfort.
As the saying goes, build tight and ventilate right.
When ventilation systems are designed correctly, but installed, commissioned, or operated incorrectly, the system ends up being leaky and inefficient and uses more energy than expected.
Project teams for Passive House buildings must find solutions for these implementation and commissioning hurdles, or the potential energy penalty can adversely effect the building’s high-performance design intent.
What happens when a Passive House construction expert and a commissioning engineer collaborate to find a solution to common ventilation system issues that cause excess energy use? We, the authors of this blog post, did just that!
Keep reading to learn about common construction issues with Passive House ventilation systems and five lessons learned based on our experiences in the field.
Passive House requirements do a great job of reducing space conditioning demands. Heating and cooling are drastically reduced because of the continuous airtight and well-insulated envelope of these buildings.
As our buildings become increasingly airtight, it becomes ever more critical to introduce fresh air and exhaust stale or contaminated indoor air. Passive House energy recovery ventilator (ERV) units are required to have high filtration with MERV 8 filters on the air supply stream and MERV 13 on the exhaust air stream. (At SWA, we typically see and recommend MERV 13 filters on both.)
We don’t have to look far for evidence supporting the need for high filtration in our buildings. The orange skies of New York City in June 2023 due to the smoke and particulates from the Canadian wildfires demonstrate why supply air is filtered.
Further, the COVID-19 pandemic brought to light the need for high filtration to reduce the respiratory spread of the virus. MERV 13 filters have demonstrated effectiveness in removing airborne respiratory droplets known to spread the virus.
Removing moisture, mold, bacteria, dander, allergens, odors and emissions from cooking, and other pollutants from the exhaust enables the improved indoor air quality benefits touted by the Passive House standard.
Without a correctly functioning ventilation system, the indoor air quality and energy performance of the building will suffer.
Typical new-construction buildings can have duct leakage upwards of 25-40%. In our view, this is unacceptable for our high-performance Passive House buildings, especially when the technology to seal ducts down to <3% leakage is readily available and cost-effective.
The chart below shows the projected energy modeling results for a small residential building with about 30 units. The design and construction models were exactly the same; the only inputs that changed were on the ventilation side.
This project had excessive duct leakage due to poorly constructed ductwork, leading to an increase in ventilation flow rates and fan power on the energy recovery ventilator (ERV) unit—thus driving up the ventilation energy and space heating demand to condition the incoming air during heating season. This contributed to about a 2.5 energy use intensity (EUI) increase.
System Leakage Impacts on PHIUS WUFI Energy Model Predictions:
In a Passive House building, the largest pieces of the energy usage pie are typically domestic hot water and miscellaneous loads (think: plug loads and occupant loads). But in this case, the commissioned ventilation flow rates and fan power have a greater impact on building energy usage than expected.
This impacted the building owner’s bottom line. They pay about $3,000 more per year to ventilate this building.
There are three different forms of leakage found in typical mechanical ventilation systems:
All of these contribute to the system’s overall leakage.
Systems thinking is essential when approaching this commissioning issue. Leakage can be attributed to various facets of a project’s implementation, including unresolved design issues, lack of clarity in the integration of the components, and constructability.
It may also cross the scope of work of numerous subcontractors. Oftentimes, it is not solely the mechanical contractor’s responsibility to mitigate system leakage but requires a team effort and clear scope of work.
Our approach at SWA is to include clarity in the design and submittal review, reinforce the design during contractor training and site inspections, and hold subcontractors accountable for meeting the project’s design intent typically demonstrated with duct tightness testing data.
“My ducts can hold water” or “duct leakage has never been an issue on any of my jobs” are common phrases when discussing leakage with mechanical contractors. But high-performance buildings, including Passive Houses, should limit duct leakage to very small fractions of the system’s air volume.
Ordinarily, traditional hand-applied sealants and mastic are not capable of reaching very low duct leakage targets. Instead, hand-applied sealants are used to reduce large leaks; then aerosolized sealant technology is used to reduce leakage to 3% of the system’s volume. This effort leads to a very energy-efficient system and allows for a straightforward air-balancing process.
Our Passive House consultants recommend an aerosol duct sealing technology that uses pressurized aerosolized sealant particles introduced into the duct system that are deposited and collected at the ductwork leakage sites. This is a highly effective process when implemented correctly utilizing the Fractional Leakage Specification provided by the manufacturer. This specification limits duct leakage to no more than 3% of the total volume of the system tested at the operating static pressure of the system.
Commissioning ventilation systems is necessary to ensure that ventilation rates are delivered and properly controlled within the spaces of the building. It’s important for the developer to bring on a commissioning engineer for Passive House projects (and every project!) as early as possible to prevent design flaws during system installation and prevent common issues early on.
Commissioning engineers ensure that a building’s energy-related systems perform efficiently, reliably, and maintain occupant comfort. They advocate for building operators and incorporate lessons learned from other buildings so that a building maintains its performance over its lifetime.
The following are the common issues that our commissioning engineers see in Passive House ventilation systems.
If there are central ERVs that run 24 hours a day or at a constant volume, it’s the installation that takes care of everything. They can easily be installed properly and run smoothly depending on what other interlocks they may have. (If they need to interlock with say, a heat pump, that adds a layer of complexity.)
But many times, there are variable air volume ERVs. Starting in the design phase, the design engineer must include the key set points needed by the installer and the testing and balancing contractor such as the minimum and maximum airflow, the duct static pressure (and its sensor location), and the supply air temperature set point.
If it’s a variable volume ERV, chances are it’s serving different variable air volume (VAV) boxes or ZRT boxes, for example, in amenity spaces in a residential building that are not supposed to have ventilation 24/7.
The sequence of how those VAVs modulate needs to be clear in the drawings and the specs and confirmed during the submittal review phase. If a VAV box is going to be controlled by a CO2 sensor, what’s the CO2 level that triggers that? What is the CFM level that the VAV is going to modulate to? And based on those changes, what’s the static pressure that the ERV needs to maintain?
If it’s a time clock that will control the VAV, that needs to be shown in the mechanical drawings and electrical drawings, and it’s crucial to indicate which trade is responsible for it. Because it’s in the mechanical drawings, is the HVAC subcontractor responsible for installing that? Or is it the electrician? Or is it a split of both?
Another common issue with variable ERV systems is that if they are variable volume and they need to maintain a duct pressure set point, the sensor must be installed in the right location and wired to the controller. And the controller needs to be set up to maintain that duct pressure.
Prior to testing on these units, one of the things we will request to receive is the testing and balancing report. When it’s a variable air volume ERV and there’s no static pressure set point noted in the TAB report, that’s a red flag. We can tell right away that it was not balanced correctly. The balancer and HVAC contractor need to return and make the adjustments prior to testing.
Other times, there is a static pressure set point noted on the TAB report, but we show up on-site and the controller looks like the image below on the left: Both supply and extract fans are working to maintain an airflow, and there is no duct static pressure sensor installed whatsoever. No one knows how that set point made it into the report.
In conclusion, here are the five most important lessons we’ve learned about Passive House certification, ventilation, and air leakage:
We have seen that the typical specifications engineers are using to assess duct leakage are not reaching the levels of performance we need to see in a low-energy building.
The process of reducing air leakage often crosses various trades, and there can be a lot of finger-pointing when this comes up on site—so project teams must approach leakage from a holistic standpoint.
Design and construction teams should understand project nuances from the start.
For developers with high-performance buildings, engaging a commissioning agent as early as possible will save time and money down the line.
Establish a good line of communication with the design engineer so there are clear sequences of operations at the installation, the testing phase, and in the future operation of the building. It’s crucial to provide training to O&M staff and have a clean transition so that the O&M team can operate the building as efficiently as possible.
This blog post is based on Tales from the Trenches— Passive House Ventilation Strategies, Common Construction Issues and How to Curb Them, March 2023, ASHRAE Cold Climate Conference.
Have a question about commissioning ventilation systems? Leave a comment below and one of the authors will respond as soon as they can!
Have questions for a Passive House consultant or commissioning engineers? Click here to contact us.
Contributors: Luis Aragon, Senior Building Systems Engineer on SWA’s Building Operations, Decarbonization, and Efficiency Team; Michael Schmidt, Senior Building Systems Consultant on SWA’s Passive House Team
Steven Winter Associates