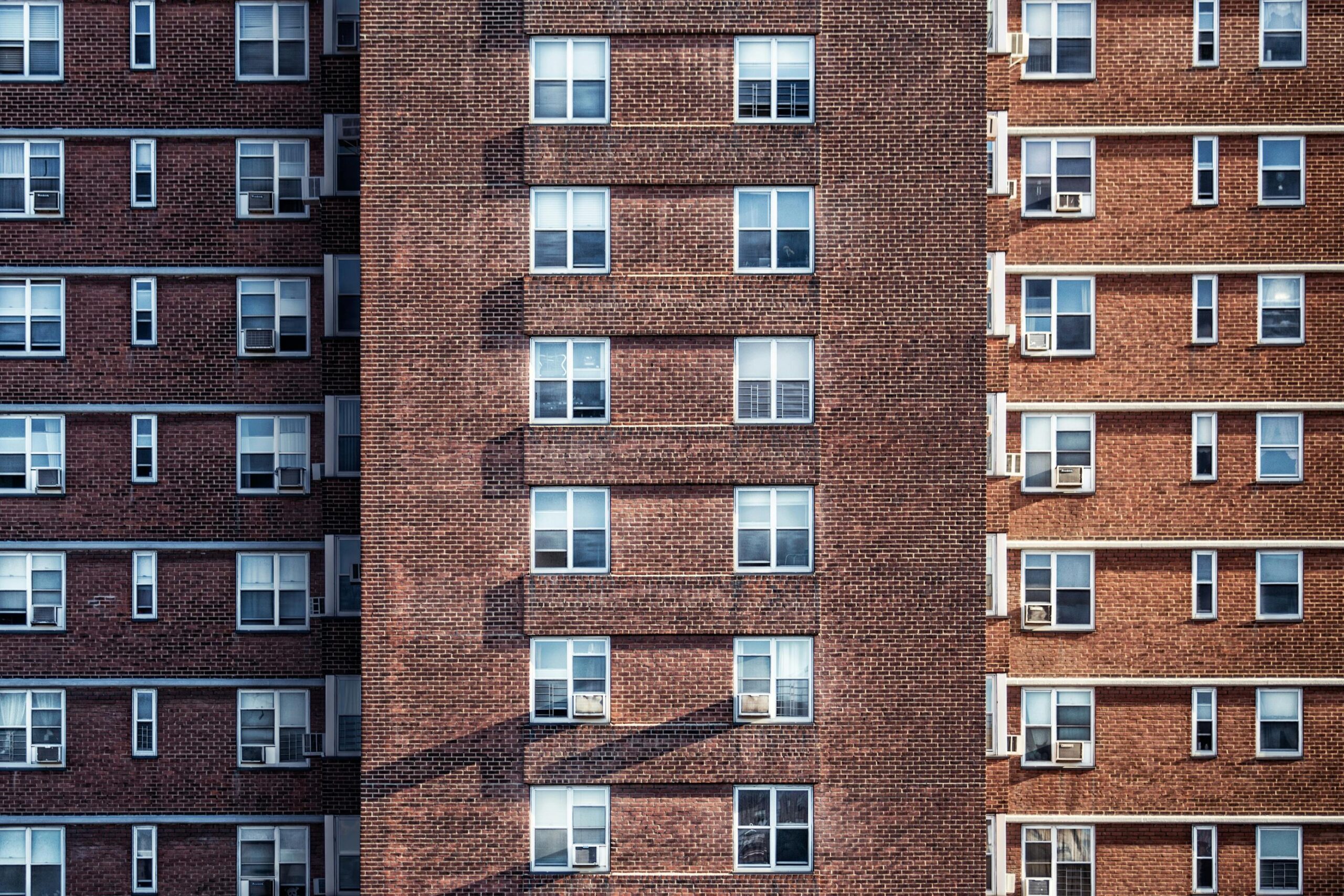
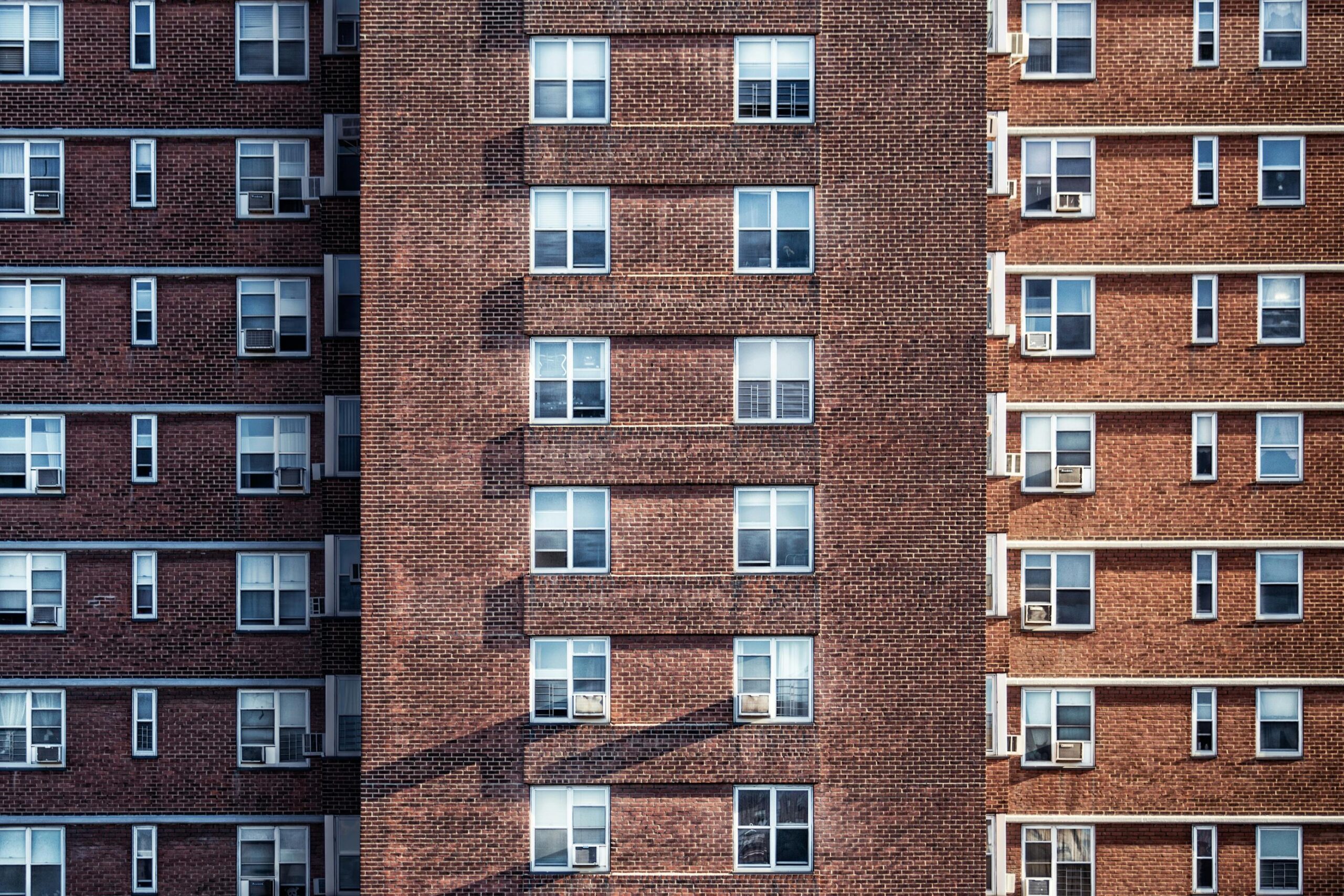
News
Three members of the Steven Winter Associates staff were selected to help draft extensive revisions to New York City’s Construction Codes. They volunteered their time to help advance building safety, sustainability, and accessibility in NYC.
The New York City Council approved extensive revisions to the city’s Construction Codes, including 600 major updates and thousands of smaller changes.
The New York City Department of Buildings (DOB) organized numerous Code Revision Committees to draft these updates. The technical committees included engineers, architects, attorneys, planners, tradespeople, and representatives of the construction industry, labor, real estate industry, and utility companies.
Three members of the Steven Winter Associates, Inc. (SWA) staff were selected to join Code Revision Committees and volunteered their time to help advance building safety, sustainability, and accessibility in New York City:
“Being a part of these code updates allowed me not only to contribute to increasing the safety and performance of new buildings and renovation projects in the city, but also enabled me to learn a lot from the knowledgeable people I worked alongside.” —Jason Block
“It was great to collaborate with other industry leaders to help make New York City one of the most accessible cities in the world. The code revisions will help improve the built environment by increasing access to all New York City spaces.” —Harold Bravo
“Participating in the UOCE committee provided an excellent opportunity for SWA to improve the built environment, citywide, by ensuring that all newly constructed buildings provide safe egress for people with disabilities, consistent with that provided on the national level.” —Mark Jackson
New York City’s construction code is one of the nation’s earliest and most comprehensive set of rules regarding construction in both new and existing buildings, according to the DOB. The approved code revisions are the first holistic update to the entire set of NYC Administrative, Plumbing, Building, Mechanical, and Fuel Gas Codes since 2014.
New code requirements will go into effect next year, including some taking effect on January 1, 2022.
Click here for more information about the Construction Code revisions, and click here to learn more about how SWA is improving the built environment.
Jason Block is the Director of the Building Operations, Decarbonization, and Efficiency team. Jason focuses on developing design and operation strategies to reduce energy use and improve occupant comfort for residential, commercial, and mixed-use buildings.
Harold Bravo is an Accessibility Consulting Director. Harold oversees consulting services for large multifamily and mixed-use projects throughout the North and Southeast for compliance with all applicable accessibility design and construction requirements. Harold also served on several local, national, and international committees.
Mark S. Jackson is an Accessibility Consulting Director overseeing SWA’s consulting services provided to the commercial sector including, but not limited to, plan reviews, field inspections, existing condition audits, due diligence and barrier removal surveys, remediation development, design assistance, litigation consulting, and expert witness services, among others.