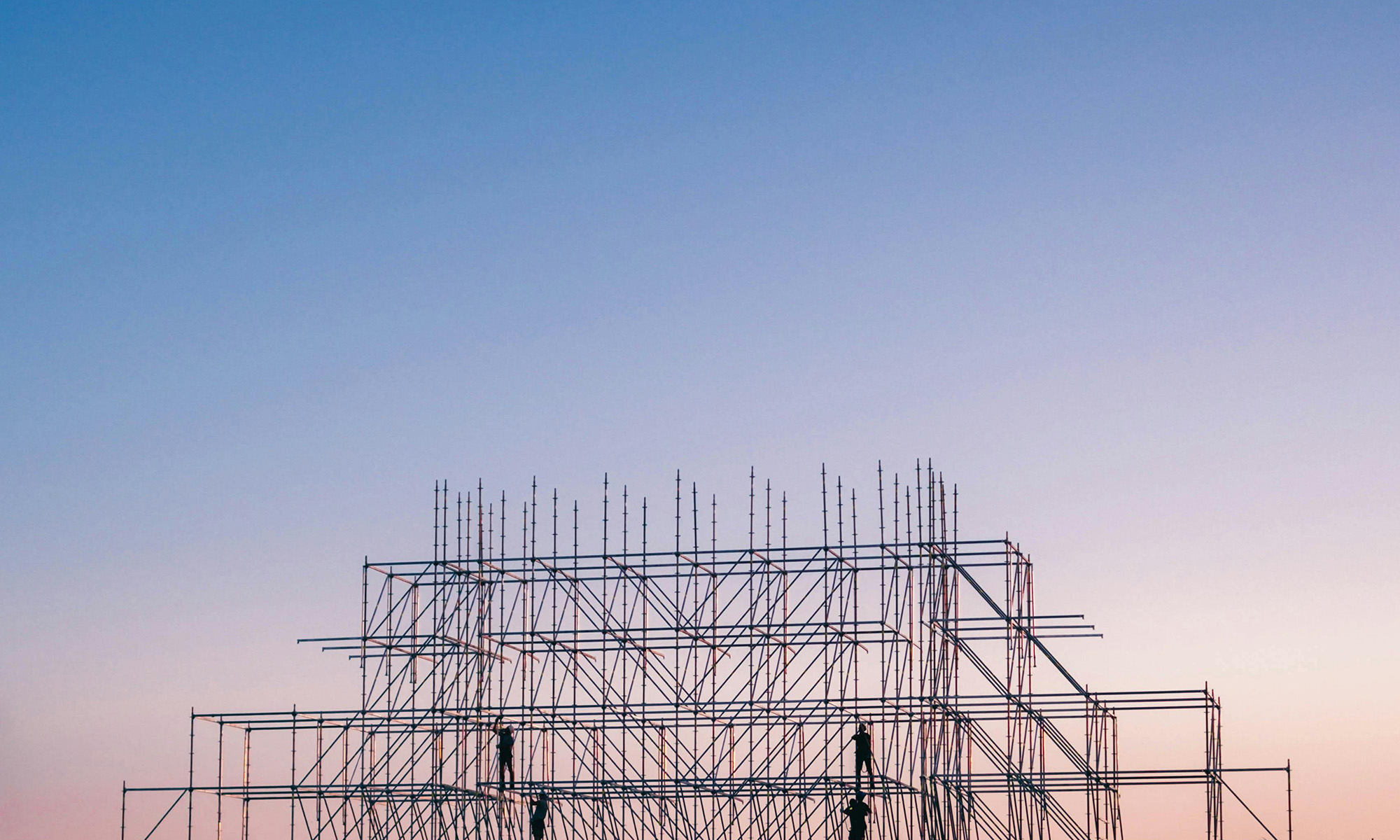
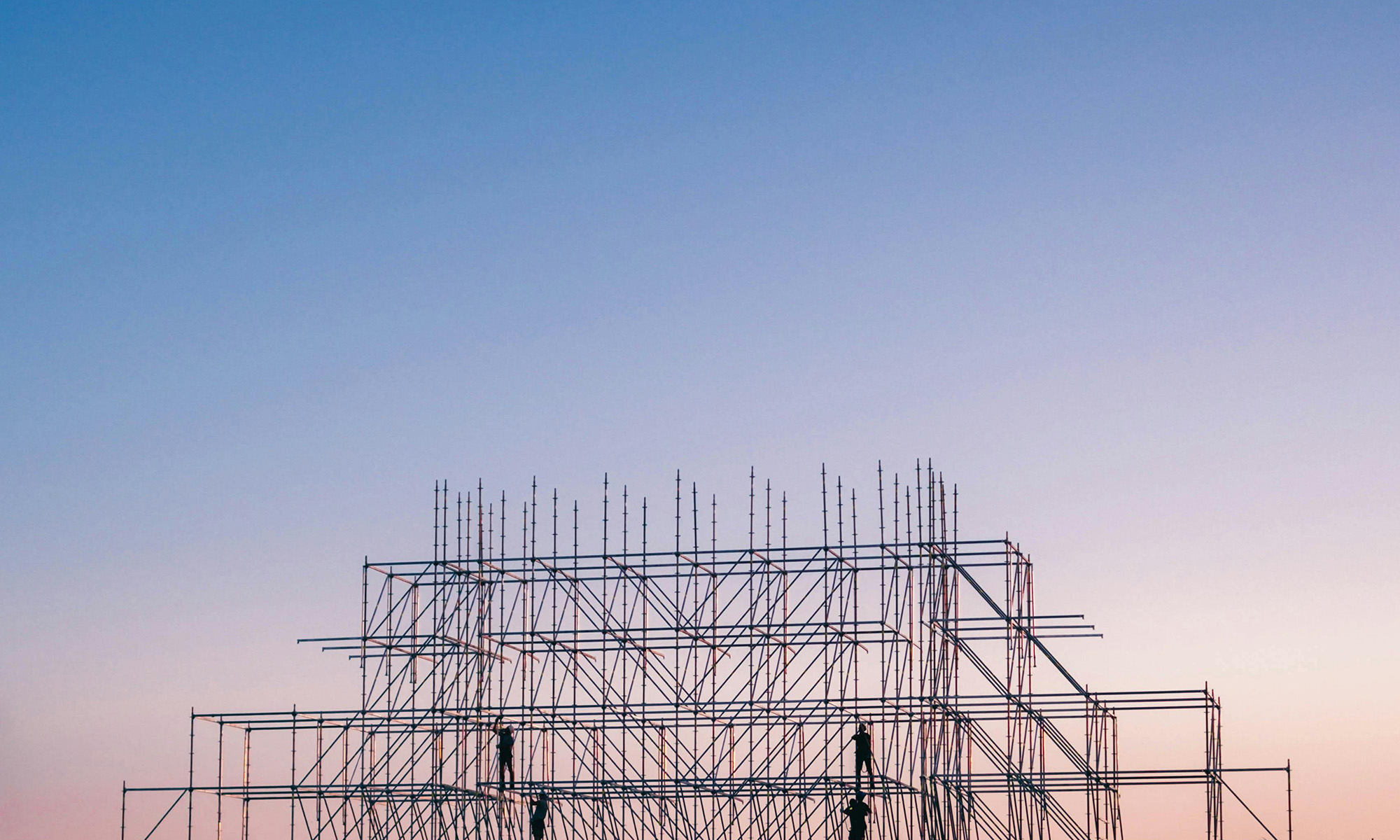
LEED v5 & Embodied Carbon: All About the New Requirements
The sustainable building industry is buzzing with anticipation for the release of LEED version 5. This update to the world’s most widely used green building rating system promises to bring significant changes, particularly in the realm of embodied carbon reduction.
Read