Search Result for ventilation — 59 articles
Designing for Passive House and Accessibility Compliance: It’s All in the Details
July 8, 2024 | Peter Stratton
The number of multifamily residential projects targeting Passive House certification has been rising steadily over the past decade, bringing along many exciting challenges. This has been especially prevalent in New York City, where increasingly stringent energy standards and a desire for innovation have made designing to Passive House standards an attractive goal. As the number of Passive House projects passing through our offices in New York City; Washington, DC; Boston; and Norwalk, CT continues to grow, we have seen some important overlaps with one of our other consulting services: accessibility compliance. In the United States, multifamily new construction projects consisting of four or more dwelling units are subject to the Fair Housing Act, as well as state, city, and local accessibility laws and codes. Projects targeting Passive House certification must comply fully with all applicable accessibility requirements. In this blog post, we will focus on projects in NYC—although most newly constructed residential projects across the country will be subject to some variation of the criteria discussed below, for both Passive House and accessibility standards. (more…) Read More
Efficiency and Health: Prioritizing Occupant Health and Wellbeing in High-Performance Buildings
July 1, 2024 | Steven Winter Associates
We like to say that a building is not sustainable if it does not sustain the health and wellbeing of all its occupants. This includes considering how the materials, technologies, and building systems affect indoor air quality, comfort, and the physical and mental health of those utilizing the space. In our post-COVID world, it also includes how a building can protect its occupants from viruses and other airborne illnesses. We’re sharing real-world examples of how SWA consultants have helped to mitigate potential negative impacts on occupant health in high-performance buildings. (more…) Read More
Indoor AirPlus Version 2: What Changes Are Coming? [Updated]
May 15, 2024 | Steven Winter Associates
The US Environmental Protection Agency (EPA) began revising its Indoor AirPlus (IAP) specification for homes and residential buildings in early 2020. Since the first drafts of version 2, several factors have shaped the new standard, including the public’s hyper-awareness of indoor air quality (IAQ) during and post COVID, input from strategic partners, and considerations from multiple public comments. The goal to improve IAQ across new and existing housing while addressing affordability and expanding access to healthy housing among disadvantaged populations will not change. But a lot will change for building designers, developers, owners, and property managers that earn the Indoor AirPlus label for their buildings. For starters, the program will now be written as Indoor AirPlus (previously "airPLUS"), and there are two levels of certification: Certified and Gold. EPA anticipates that version 2 will be available for use in fall 2024, and version 1 will be sunset in January 2026. During this overlap period, partners may opt to use either version. Below, we've summarized the changes to expect from Indoor AirPlus version 2. (more…) Read More
To Your Health: What to Know About Cooking and Indoor Air Quality
December 19, 2023 | Steven Winter Associates
There's more to a healthy meal than what's on your plate. Cooking inside a home or apartment produces contaminants—those of primary concern are PM2.5 and nitrogen dioxide (NO2)—and without an exhaust strategy, these pollutants will remain inside and diminish indoor air quality. In addition, one of the biggest news stories of 2023 was the Canadian wildfires. These events had many on the East Coast thinking about outdoor air quality and how to keep their indoor air as healthy as possible. The primary pollutant of concern from smoke is PM2.5. There are numerous ways to keep polluted outdoor air outside, but what about the additional exposure to PM2.5 that can happen indoors? Homeowners and renters can create a ventilation strategy to maintain safe levels of PM2.5 in their living space—whether there are outdoor air quality warnings or not. Keep reading to find out how. (more…) Read More
What Can Go Wrong with Passive House Ventilation Systems—and How to Prevent It
October 24, 2023 | Steven Winter Associates
The envelope of a Passive House building is designed to be significantly airtight. Mechanical ventilation systems introduce fresh, filtered air and exhaust stale, contaminated air 24 hours a day—which is extremely important in maintaining optimal indoor air quality and occupant comfort. As the saying goes, build tight and ventilate right. When ventilation systems are designed correctly, but installed, commissioned, or operated incorrectly, the system ends up being leaky and inefficient and uses more energy than expected. Project teams for Passive House buildings must find solutions for these implementation and commissioning hurdles, or the potential energy penalty can adversely effect the building’s high-performance design intent. What happens when a Passive House construction expert and a commissioning engineer collaborate to find a solution to common ventilation system issues that cause excess energy use? We, the authors of this blog post, did just that! Keep reading to learn about common construction issues with Passive House ventilation systems and five lessons learned based on our experiences in the field. (more…) Read More
5 Strategies to Create Sustainable and Affordable Housing with Enterprise Green Communities (EGC)
August 4, 2023 | Steven Winter Associates
Access to sustainable and healthy buildings should be a universal right. Unfortunately, underserved communities and low-income families often face significant barriers to living in buildings that are efficient, supportive, and resilient. The Enterprise Green Communities (EGC) certification program provides criteria to create sustainable, healthy, and affordable housing and offers a pathway our industry can use to advance equity in the built environment. Thirty-one states, plus Washington, DC, require or encourage developers seeking affordable housing funding to follow the Enterprise Green Communities Criteria. However, any housing development in the U.S. with affordable homes can earn the Enterprise Green Communities certification. (Projects that achieve the 2020 EGC certification also receive WELL certification.) In this blog post, we’re sharing the strategies we use most often as EGC consultants, along with a common challenge and solution, to achieve certification and create more sustainable communities. (more…) Read More
Sustainable Buildings Are Healthy Buildings: How to Design and Maintain a Healthy Built Environment
October 24, 2022 | Steven Winter Associates
What is a sustainable building? We know it must be an energy-efficient, high-performance building and emit as little carbon as possible to protect the environment. But a sustainable building must also be a healthy building that protects people and communities. A building can’t be considered sustainable if it doesn’t sustain the physical and mental health of all its intended occupants and sustain the community around it. Healthy buildings require a holistic approach that accounts for how every building material, system, and technology affects the wellbeing of occupants. This is an important topic at SWA, so we asked our interns to explore it! They talked to our experienced building systems, sustainability, and Passive House consultants and put together this blog post as a resource on designing and maintaining a healthy built environment. Keep reading to learn more about the following considerations for healthy buildings:
- Occupant comfort and productivity
- Optimal indoor air quality (IAQ)
- Ventilation system upgrades in existing buildings
- Healthy building certifications (Fitwel, WELL, etc.)
- Building operations and maintenance staff training
What Would a Passive House New York City Look Like?
February 2, 2022 | Steven Winter Associates
New York City: the city that never sleeps—and where buildings account for approximately two-thirds of greenhouse gas emissions. In 2019, New York City Council passed Local Law 97 (LL97) to hold building owners responsible for carbon emissions. The goal is to reduce over time, eventually reducing emissions 80% by 2050. As it stands, the law applies to most buildings over 25,000 square feet, which is roughly 50,000 residential and commercial properties across the five boroughs. One pathway to decarbonize New York City’s buildings is using the Passive House standard: a high-performance building standard that significantly reduces whole building energy consumption by up to 60-70% while providing superior comfort and indoor air quality. When coupled with renewable energy systems, Passive House makes net zero energy buildings more feasible. (more…) Read More
Choose Your Adventure: Constructing New vs. Adapting Old
August 20, 2021 | Steven Winter Associates
To meet the goals of the Paris Climate Agreement, we must make decisions that will result in the greatest near-term carbon savings. This means taking into account both embodied carbon—those upfront emissions associated with the extraction, manufacture, transportation, and assembly of building materials—as well as the carbon that’s emitted over the course of the building’s operational phase.
We can build a high-performance building with very low operational emissions, but if its embodied emissions are so high that even if it’s a net-zero energy building (meaning it has net-zero operational energy consumption) it would take decades for the building to reach net-zero carbon (meaning it has net zero whole-building lifetime carbon emissions), we’re not actually helping to solve the critical issue of near-term carbon.
(more…) Read More
Best Practices for Designing & Installing VRF Systems in Commercial and Multifamily Applications (Part 1)
July 7, 2021 | Steven Winter Associates
With LL97 fines around the corner, building owners and managers are looking to reduce greenhouse gas emissions. To do so, building systems will need to rely on an increasingly green electric grid rather than fossil fuels. And as we look to electrify our buildings’ heating and cooling systems, Variable Refrigerant Flow (VRF) systems have emerged as one solution. With buildings increasingly turning to this technology, we are sharing our current best practices for designing, installing, and operating VRF systems to help everyone — from design engineers and developers to installers and building operators — learn more about the nuances of VRF. These best practices are based on manufacturers’ literature, ASHRAE and IECC standards, conversations with field technicians, design engineers, building operators, and manufacturers’ representatives, as well as Steven Winter Associates’ extensive functional testing experience. While the focus is intended to be large VRF systems ( >5 tons), many of the best practices are also applicable to smaller mini-split or multi-split systems. Common terms used throughout this post are defined for those new to the topic and can be found by scrolling to the bottom of the blog. (more…) Read More
Designing for a Post-COVID World with Passive House
March 17, 2021 | Steven Winter Associates
Passive House design for large multi-family buildings aligns with and builds upon industry guidance for mitigating the spread of infectious diseases.
As the world continues to be turned on its head by the impacts of COVID-19, the building industry has been scrambling to respond, encouraging designers and building operators to learn about how their buildings are being ventilated. Industry experts have produced an array of documents and reports outlining guidelines for reopening buildings safely while minimizing the risk of transferring infectious disease. Much of the focus of this guidance has been on using mechanical ventilation and proper air distribution to dilute contaminant levels in spaces and minimize the spread of viruses. The American Society of Heating, Refrigeration and Air-conditioning Engineers (ASHRAE) has produced a significant amount of guidance for designers. One of their main documents, produced in April, is the “ASHRAE Position Document on Infectious Aerosols,” which provides useful information for how buildings should be designed and operated in response to a pandemic. However, it has prompted questions from design teams about how this might conflict with the goals of very low energy buildings, such as Passive House (PH). This blogpost is written as a response to some of these questions and to highlight the benefits of Passive House design in light of recent recommendations by groups like ASHRAE.
Benefits of Passive House for Mitigating COVID Transmission
The following are some of the benefits of Passive House design for multi-family buildings compared to code requirements as well as some additional guidance for how to design to mitigate virus transmission. (more…) Read MoreIt’s Beginning to Look a Lot Like …. Cold Season
December 10, 2020 | Steven Winter Associates
Imagine it’s Christmas morning. You wake up from a nice sleep eager to spend time with family and open presents. You can’t wait to get out of bed but know that the warmth you have under the covers will soon escape into your cold, drafty apartment. The window doesn’t close that well, and the baseboard heater can never quite get up to the desired temperature. Now you’re cold. Your body is working harder to warm you, so now you’re tired too. Your only comfort is the idea of sitting by a fire soon with a cup of hot cocoa… except it’s not actually Christmas. It’s just a normal day, and you’re cold…again. For most of us, feeling cold is simply just uncomfortable and may decrease our productivity. However, for the elderly being cold can lead to health problems, organ failure, and even hypothermia. Seniors who are chronically cold during the winter may not even know the toll their discomfort is causing to their health, and they may require a more adequate living environment to keep them safe. When preparing for the development of a new senior residence, it is important to take into consideration the needs of the senior demographic during the design phase. Keeping our seniors safe is one of the biggest priorities for senior living facilities, not only when it comes to ADA compliant and accessible living conditions, but also regarding tenant comfort and health. (more…) Read More
Electrifying Central Ventilation Systems in Multifamily Buildings
August 21, 2020 | Steven Winter Associates
A common strategy to provide ventilation in multifamily buildings is to design a central roof-top air handler that distributes outdoor air to each unit. The energy cost for this system, which commonly uses natural gas for heating for either a gas furnace unit or hot water from a central boiler is paid for by the building owner. However, there is another option – VRF[1]. With the unprecedented rise of VRF technology in the last decade combined with regulations such as New York City’s Local Law 97 of 2019[2] (carbon emission penalty), the industry is taking a giant leap towards building electrification. There are always questions and concerns raised against building electrification ranging from initial cost to operating cost to reliability of the VRF technology. From the owner’s perspective, the biggest question is usually surrounding the operating cost of an electric system compared to a natural gas system for heating, but the cost of ownership must consider multiple energy metrics. I was curious to understand the impact on various building energy profile metrics associated with a Dedicated Outdoor Air System (DOAS) using the conventional gas fuel source vs. the latest VRF heat pump technology using electricity in a multifamily building. The findings of this investigation challenge the deep-rooted notion that electricity, being more expensive than natural gas per BTU, will always cost more to operate. (more…) Read More
Leveraging LEED for New Construction Post-COVID Part 2
June 26, 2020 | Steven Winter Associates
LEED: Toolkit for a Healthy and Resilient Post-COVID Built Environment
At SWA, we have used LEED across a wide range of projects and contexts. We have seen firsthand its strength as an adaptable toolkit for guiding high performance building design, construction, and operation. The intent of each LEED credit category takes on a particular meaning, both locally and globally, in response to the emergence of such factors as global climate change and its associated consequences—including pandemics. In the post-COVID context, these intents will take on new meaning and new urgency. Read Part 1 of this blog here! The overall goal of the LEED rating system is to reduce the negative impacts of the built environment on environmental and human health. Ideally, this focus contributes to our general, overall resilience to public health crises such as the COVID-19 pandemic by reducing and mitigating various factors that make us more vulnerable to diseases. For example, we know that long-term exposure to air pollution and poor air quality dramatically increases the chances of dying from COVID-19 and that most of the same pre-existing conditions that increase the risk of death for COVID-19 are the same diseases exacerbated by exposure to air pollution. Anything we can do to improve air quality will also improve our resilience to disease. Most significantly, we need to move away from fossil fuel-based energy and toward clean, renewable energy—and a large portion of LEED is focused on doing just that. As researchers have noted, many of the root causes behind climate change also contribute to a greater risk of pandemics. An example is deforestation and associated habitat loss, which forces wildlife to migrate, bringing novel viruses into closer contact with livestock and humans, and increasing the odds of disease transmission. On top of that, by altering temperature and rainfall patterns, climate change has created conditions that are more conducive to the spread of disease in general. So, the strategies we need to enact now to address the climate crisis—many of which are addressed in LEED credits—can also mitigate the occurrence, scale, and impacts of future disease outbreaks. (more…) Read MoreAccessibility Tech Notes: Automatic Doors
June 16, 2020 | Peter Stratton
As the country continues to confront the realities of the COVID-19 pandemic, the way we navigate spaces is changing. One of these changes is the way we interact with common use objects that traditionally require hand-operation, like doors. While automatic doors have always been a good option for providing greater access to people with disabilities, hygiene concerns associated with the spread of disease have presented another argument for their use. The rise of touchless technology as a result of this pandemic will increase the use of automatic doors not just for accessibility or convenience, but for public health as well. For anyone considering incorporating automatic doors into their designs, either for new construction or as a retrofit, here are some important things to consider:
(more…) Read More
Leveraging LEED for New Construction Post-COVID Part 1
June 11, 2020 | Steven Winter Associates
In the post-COVID world, there needs to be a greater awareness that the built environment can protect and promote human and environmental health. Buildings can, and must, play a critical role in delivering a stronger, more resilient public health infrastructure that can help prevent and mitigate crises such as the SARS-CoV-2 pandemic. The good news is that we already have effective tools for designing, constructing, and operating such buildings—chief among them LEED and the WELL Building Standard. We believe people are now more conscious of how the built environment affects their health. As a result, we’re likely to see an increase in investment in sustainable building design, construction, and operation and a corresponding increase in demand for green building rating systems such as LEED and WELL. We may also see the green and healthy building concepts that are included in these systems increasingly integrated into building codes. Certification programs (e.g., LEED and WELL) have been developed though collective effort. They are extremely effective and adaptable tools that project teams can use to ensure that their buildings achieve the best possible performance in terms of protecting environmental and human health. Importantly, these programs continue to evolve, offering ever more effective strategies for improving the built environment, ensuring that buildings adapt to whatever circumstances may arise in uncertain times. But right now, project teams can make immediate use of LEED and WELL, and similar tools, to start preparing for the new reality ushered in by the COVID-19 pandemic. How can project teams leverage LEED now? In this series, we’ve highlighted the LEED credits that can be used to guide efforts to make our buildings safe, healthy, and resilient. (In a follow-up series we’ll discuss the WELL features that can be used to guide our post-COVID building work.) (more…) Read More
Interesting Elements: A Modeling View on Net Zero Homes
May 22, 2020 | Steven Winter Associates
I recently performed some net zero energy modeling on a single-family home for work. Around the same time, I got to chatting with my neighbor (mindful of social distancing) and when I mentioned net zero, he said, “Is that even possible?” AH! Get the word out. We have the means to offset our home energy use. What follows are the basics to consider when trying to fully offset home energy along with a breakdown of how different upgrades can affect energy use. There are lots of resources available on how to reduce home energy use. You can look at program requirements and guidelines like the Zero Energy Ready Program or Passive House. Through modeling I will demonstrate how the energy use numbers change and describe what we have seen in real-world examples of net zero homes. Net zero is not new and we’ll be looking at some specific pieces of single family home modeling. (more…) Read More
The Great Indoors: Creating a Healthier and Safer Built Environment
April 16, 2020 | Jayd Alvarez
As humans, we spend a lot of time indoors. Studies by the U.S. Environmental Protection Agency indicate that under normal circumstances the average American spends over 90% of their life indoors. With the spread of COVID-19 and widespread voluntary and involuntary quarantine, the rise of work from home policies and new direction to social distance has resulted in a further increase to the amount of time we spend indoors. Now more than ever, people are cognizant of the air they’re breathing and the surfaces they’re touching. The buildings that we live, work and play in impact our physical and mental health. With certain building and design considerations, we can make these impacts beneficial.
We recruited some experts at SWA to fill us in on the various considerations when it comes to the health and comfort of a building, as well as some certifications that assure these considerations are met.
(more…) Read More
The 3 Most Important Design and Construction Considerations for Senior Living Facilities
February 26, 2020 | Jayd Alvarez
Last year, a young New Zealand lawmaker shut down a fellow member of parliament who was heckling her climate change speech with two words: “OK, Boomer.” This simple phrase started an online wildfire and ignited a conversation about the generation known as “baby boomers.” Born just after World War II, this demographic represents a period of growth, hope, and prosperity. The building, real estate, and senior housing industry has been thinking about the boomer generation for a while now. Between the years 1946 and 1964, 76 million babies were born. Every day until 2030, 10,000 of these individuals will turn 65, which means they will likely be retiring, and eventually considering how and where they want to age. This poses the question: how are we going to meet the growing demand for housing and care for this population?
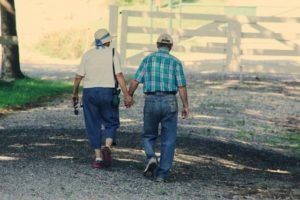
Important Considerations for Senior Living
Whether you or someone you love is considering staying in their home as they age or moving into a senior living facility, there are a few important factors to keep in mind. SWA services for senior living revolve around the following three factors:
(more…) Read MoreNet Zero and Electrification
February 5, 2020 | Steven Winter Associates
“Net zero” can mean a lot of different things depending on what you choose to measure – zero energy usage, zero carbon emitted, zero lifecycle impact, etc.
At Steven Winter Associates, Inc. (SWA), we work with clients who are approaching net zero from different angles: driven by institutional goals, climate concerns, marketing campaigns, and connecting with municipal emissions targets. One thing we see over and over is that super high performance is difficult to achieve, but with a key simplification – there are not many ways to do it. All roads may lead to Rome but the closer you get, the fewer roads there are to take.
(more…) Read More
Passive House: An Alternative Compliance Path to Toronto Green Standard Tier 3
January 9, 2020 | Steven Winter Associates
It is clear to see that the Passive House (PH) standard is here to stay! Across North America, more States, Provinces, and Municipalities are integrating PH into their building standards. One of the more recent adopters is the City of Toronto. In the most recent version of the Toronto Green Standard (TGS), the PH standard is offered as an alternative compliance path to TGS Tier 3, and with this alternative compliance path one obvious question comes to mind: What is the major difference in required component efficiency for a multifamily building in Toronto that is looking to meet either the PH standard or TGS Tier 3?
The PH standard is performance-based and is focused on decreasing whole building energy demand, improving building durability, providing optimal occupant thermal comfort, improving indoor air quality, and reducing carbon emissions. The PH standard reduces building operation costs, decreases carbon emissions, and supports an improved indoor environmental quality for building occupants. The TGS has similar goals and benefits when compared to the PH standard, and there are some obvious synergies in the program design between TGS and PH. The tiered energy category in the TGS takes a similar approach to PH by offering an annual budget for three different categories. For PH you must comply with a total energy budget for annual heating demand, annual cooling demand, and total source energy use intensity. Similarly, but slightly differently, the TGS offers a budget for total site energy use intensity (TEUI), annual heating demand or Thermal Energy Demand Intensity (TEDI), and the additional category of Greenhouse Gas Intensity (GHGI). In both standards, the path to compliance is non-prescriptive and designers can implement a variety of component efficiencies and system options. See table 1 and 2 below:
(more…) Read MoreWhole Building Blower Door Testing – Big Buildings Passing the Test
November 15, 2019 | Steven Winter Associates
The residential energy efficiency industry has been using blower door testing since the mid 1980’s to measure the air tightness of homes. Since then, we’ve evolved from testing single family homes, to testing entire apartment buildings. The Passive House standard requires whole-building testing, as will many local energy codes, along with assembly testing. While the concept of – taking a powerful fan, temporarily mounting it into the door frame of a building, and either pulling air out (depressurize) or pushing air into it (pressurize) – is the same for buildings both large and small, the execution is quite different for the latter. Commonly called a whole-building blower door test, we use multiple blower doors to create a pressure difference on the exterior surfaces of the entire building. The amount of air moving through the fans is recorded in cubic feet per minute (CFM) along with the pressure difference from inside to out in pascals. Since the amount of air moving through the fans is equal to the amount of air moving through the gaps, cracks, and holes of the building’s enclosure, it is used to determine the buildings air tightness. Taking additional measurements at various pressure differences increases the measurement accuracy and is required in standards that govern infiltration testing. Larger buildings usually test at a higher-pressure difference and express the leakage rate as cubic feet per minute at 75 pascals or CFM75. (more…) Read More
Climate Week NYC: Seven Days of Climate Action and Discussion
September 6, 2019 | Jayd Alvarez
Last week, as I was writing this blog, I came across a New York Times article: “The Amazon, Siberia, Indonesia: a World of Fire.” By now, I’m sure most of us are aware that the Amazon Rainforest has been burning for weeks, but this deliberate act of environmental destruction will contribute to a feedback loop. These fires release carbon dioxide and kill the trees and species that not only remove greenhouse gasses from the air but are part of vital fragile ecosystems. As more climate-warming gasses fill the air, extreme weather patterns, drought, species loss, and global warming are exacerbated. These effects then accelerate the spread of infectious disease, global poverty, and human health defects. Overall, climate change and environmental degradation negatively affect both humans and the planet, which makes us less resilient and allows for climate change to accelerate even more aggressively. And the cycle continues.
So, for the sake of our (really wonderful) natural planet, and humankind, it is crucial that we try to hinder this feedback loop and make climate action a priority around the world. And, although individually we can try to have a more reciprocal relationship with the planet, our actions and voices carry more weight collectively, which is where Climate Week NYC comes in.
What is Climate Week NYC?
Organized by The Climate Group, Climate Week NYC is an annual week-long gathering for citizens and global leaders to join forces and take action to mitigate environmental harm caused by human activity. There will be a number of public events each day from September 23-29, including tours, film screenings, conferences, and more. Fun fact: Swedish teenager and activist Greta Thunberg sailed across the Atlantic all the way from England to meet with UN Secretary-General Antonio Guterres, and to attend the United Nations Climate Action Summit, scheduled on the first day of Climate Week NYC! (more…) Read MoreWhat the Climate Mobilization Act Means for Developers, Designers, and Construction Teams
August 7, 2019 | Steven Winter Associates
The construction industry has been increasingly focused on meeting ever-tightening codes and achieving higher ratings in sustainability certification programs (e.g., LEED, Passive House, etc.). These standards do a good job of raising the bar, but there is a new bar in town and we’re not talking about whiskey.
Local Law 97
NYC’s Local Law 97 of 2019 establishes carbon emissions limits for buildings 25,000 square feet and larger. These emissions limits, which are based on current building performance data, will begin in 2024 and will rachet down in 2030 and beyond. While we continue to work with building owners and portfolio managers of existing buildings (“What Does the Climate Mobilization Act Mean for Building Owners?”), we need to make sure that new buildings and major renovations are set up for success. Developers, designers, and construction teams must take LL97 into account during design, construction and turnover to protect the value of these new assets. A developer or asset manager’s least favorite word is probably uncertainty, and now there’s a whole new host of uncertainties to think about: (more…) Read MoreIt’s Time to Focus on Our Schools
July 26, 2019 |
If you are a parent like me, I am sure you cherish your kids and seek to offer them the best opportunities in life. I even moved to a different school district. And, while the education is top-notch in my town, I have come to realize that it really doesn’t matter what school district you are in…all our schools need help. I am not talking about smaller class sizes, better pay for teachers, after-school programs, and more school supplies, although those are important. School buildings need attention. With budgetary pressures, a lot of maintenance and repairs are being deferred and schools are not aging well. Whether it is repairing existing systems, replacing systems at the end of their useful life, renovating, or building a brand-new school to service your community for future generations, advocate for your Board of Education (BoE) to think holistically about improving the conditions for our children.
Why My Call to Action?
This year I was asked to join our elementary school’s Tools for Schools committee, which is tasked with implementing an indoor air quality (IAQ) management plan. This experience gave me an opportunity to get involved and provided me insight into the school’s systems and the operations and maintenance (O&M) processes that were in place. Unfortunately, at the start of the 2018 school year, mold issues were identified in our local middle school and the building was closed. In fairness, I quickly realized that buildings were outside the BoE members’ knowledge base. Afterall, they are educators, not facility managers or building scientists. They sought outside consultants but didn’t know the right questions to ask. After some time, the BoE decided to get input from local experts in the community. Fortunately, we have several experts (including me) who were willing to volunteer their time. As part of a task force, we laid out a strategy to remediate the mold issues in the school and to implement short- and long-term repairs to minimize/eliminate water incursion and elevated moisture issues within the building. I am not saying you must get involved at this level, but I do encourage you to attend a BoE meeting and start asking questions related to IAQ. Ask if the school has deferred maintenance needs and if/when these are being addressed in the annual budget. Ask when (if) comprehensive physical needs assessments and energy audits were performed on all school buildings. Educate yourselves; then help educate your BoE and your community on IAQ guidelines for schools. Here are some great resources:- EPA’s Indoor Air Quality Guidelines for School Building Upgrades
- Operations & Maintenance Tools from the New York City Department of Citywide Administrative Services (DCAS) Division of Energy Management (DEM)
- EPA’s Indoor Air Quality Master Class Professional Training Webinar Series
- ASHRAE’s Advanced Energy Design Guide for K-12 School Buildings
- EPA’s School IAQ Assessment Mobile App
- USGBC’s The Center for Green Schools
- NIOSH’s Dampness and Mold Assessment Tool – School Buildings
How Can SWA Help?
In working with schools, I have learned that one of the greatest challenges school decision-makers face is not knowing where to turn for support and guidance. Steven Winter Associates, Inc. (SWA) has been working to improve educational facilities for decades. Whether you have questions related to mold, moisture, comfort, absenteeism, accessibility, high utility bills…on up to zero energy design and progressive learning environments, SWA can support you. Here is just a sample of past school projects that SWA has worked on: (more…) Read MoreFive Steps to Get Started with Net Zero Energy Buildings
July 17, 2019 | Dylan Martello
Net zero buildings are becoming increasingly mainstream, with many jurisdictions adopting policies to move towards net zero new construction codes. A good overview of advanced energy codes is available on the Getting to Zero Forum, which includes a snapshot of activity around the country including Washington, DC, New York and Massachusetts.
What Does it Mean to be Net Zero?
The term “net zero” commonly refers to zero-energy buildings. In simple terms, a zero-energy building is one that produces as much energy as it consumes on an annual basis. There can be nuances and caveats to this definition, but for now, we want to bring you up to speed on five key net zero energy strategies to consider if you’re interested in developing a net zero building. 1. Maximize space for on-site renewable energy. How tall is your building?- Any building over five stories will be challenging, if not impossible, to achieve net zero with on-site renewable energy production alone because building energy demand will likely exceed available site area. Maximize your solar with a smart layout and consider if other renewables, such as geothermal, are possible.
- Your development may have a separate parking garage or parking lot on site. These are great places to install a PV system, which can significantly increase the amount of on-site renewable energy production and help make achieving net zero more of a reality.
- If you don’t have enough room for on-site renewables, you can look into purchasing off-site renewable energy options, such as community solar, power purchase agreements, or renewable energy credits.
The First Certified Passive House in Southeast Asia – Star Garments Innovation Center
June 6, 2019 | Dylan Martello
Following up on our blog post in August 2018 – Just Your Typical Blower Door Test… in Sri Lanka – Star Garment Innovation Center – we have exciting news coming out of Sri Lanka. The Star Garments Innovation Center is now officially certified as a Pilot EnerPHit building, the building retrofit standard under the Passive House Institute (PHI).
EnerPHit certification for this project is a milestone achievement on many levels. The Innovation Center is now the first certified Passive House in Southeast Asia and one of only a handful of certified PH projects in tropical climates. PHI deemed the project “a milestone in industrial energy efficient retrofitting in a tropical monsoon climate.” Many of the passive measures employed at the Innovation Center, including continuous exterior insulation, highly efficienct windows, variable refrigerant flow heat pumps for cooling with wrap around heat pipe for enhanced dehumidification capacity, and balanced ventilation with heat recovery can be utilized across all future construction projects in tropical climates. The Passive House team here at SWA is excited to see the potential growth in tropical-climate Passive House construction as a result of the Innovation Center’s success.
But what good is certification if the building doesn’t perform as well as the energy model predicts? Well, we have exciting news on this front too!
At the very start of SWA’s involvement in the project back in the summer of 2016, SWA conducted a utility analysis of the base building prior to any renovations to predict and later verify the energy savings of the Innovation Center by designing to the PH standard. Once the energy model was developed, SWA predicted approximately 50% in energy savings when compared to the previous building’s energy bills.
Fast forward to Fall of 2018 and the building has now been occupied for a full year. The two inevitable questions are:
- How much energy is the Innovation Center saving as compared to the previous building?
- How does the modeled energy use for the Innovation Center compare to what it is actually using after a full year of occupancy?
Establishing Moisture Control in Multifamily Buildings
February 28, 2019 | Dylan Martello
Most of us are familiar with the feeling of a humid apartment after taking a hot shower. Some of us kick on an exhaust fan, perhaps un-fog the bathroom mirror, or even open a window to get the moisture out. Domestic moisture generation—moisture from human activity—is a major factor driving the humidity levels in our residential buildings, especially in super air-tight, Passive House construction. Before diving into just how much of an impact domestic moisture has in our buildings, let’s first look at average daily moisture generation rates of a typical family of three[1]:
- breathing and transpiration—6 to 9 pounds of water vapor/day;
- 10-minute shower in the morning for each individual—3.6 pounds of water vapor;
- cooking fried eggs and bacon for breakfast—0.5 pounds of water vapor;
- cooking steamed vegetables with pasta for dinner—0.5 to 1.0 pounds of water vapor; and
- one small dog and a few plants around the house—0.5 pounds of water vapor/day
There are two basic types of cores:
- Heat recovery ventilator (HRV) in which a certain percentage of sensible heat is recovered (transferred from the exhaust air stream to the supply air stream) while no moisture is recovered.
- Energy recovery ventilator (ERV) in which a certain percentage of sensible heat and a certain percentage of moisture in the air is recovered.
ERV | HRV | |
Pros | Summer – prevents high exterior air moisture load from being supplied to interior air; cooling loads are minimized | Winter – flushes high internal moisture load out of building; humidity levels reduced |
Cons | Winter – if internal moisture generation is high, interior moisture load is not flushed out of apartment; humidity levels increase | Summer – allows exterior air moisture load to be supplied to interior air: cooling loads increase |
Figure 1. Moisture related pros and cons with ERVs and HRVs in high efficiency, airtight construction
Traditionally, the key factor in deciding between an ERV or HRV for a high-efficiency building has been the project’s climate. However, as internal moisture loads begin to exceed exterior moisture loads in high-density projects, the decision between ERV or HRV must be looked at more closely for each project regardless of climate. (more…) Read MoreERV + AHU?
February 7, 2019 | Robb Aldrich
Everyone pretty much gets that continuous (or very frequent) ventilation is necessary in high-performance homes. And – at least in theory – most people get why balanced, heat recovery ventilation is better (than unbalanced and/or without heat recovery). But the devil’s in the details. A couple years ago we started an R&D project with funding from DOE’s Building America program, and one of the first steps was interviewing several developers about ventilation (single- and multi-family residential, mostly on the East Coast). For none of these developers were HRVs or ERVs standard.[i] They all had some experience with ERVs, however, and when asked about these experiences the word “nightmare” came up shockingly often. The ERVs on the market now can certainly work well in the right application, but we see problems more often than not. One of the biggest challenges is trying to add ERVs on to central heating/cooling systems in homes. Most ERVs aren’t really designed for this, and here’s what we see:
- Ducts connected to the wrong places! Outlet and inlet ducts get reversed, or the supply air from the AHU getting exhausted (sad how often this happens).
- ERVs are attached to supply and/or return trunks of the AHU. Unless the AHU fan is running constantly (or whenever the ERV is turned on), outdoor air comes into the AHU and is sucked right back out the ERV exhaust.
- If the AHU fan is turned on, the relatively small fans in the ERV can’t successfully compete with the big AHU fan. People don’t get the ventilation flow rates they want and/or the flows are very unbalanced.
- AHU fans can use A LOT of electricity. Hundreds of Watts is common - I’ve measured over 1 kW (though this is changing - more below).
Does Your Exhaust Fan Suck? Part 2
February 6, 2019 |
If you recall from Part 1 of this article written back in September, we discussed why exhaust fans often don’t operate as they are intended. Now, let’s discuss how to rectify these issues. First, we need to understand that all fans are not created equal. To do this, SWA participated in a “blind” study that analyzed a number of today’s common exhaust fans. The study emphasizes the importance of fan selection. With this understanding, we will then discuss solutions and best practices for installing bathroom exhaust ventilation.
The “Blind” Study
To get a comprehensive performance dataset for a number of exhaust fans, the Riverside Energy Efficiency Laboratory (REEL) was engaged for a “blind” study. REEL is the HVI/ESTAR neutral, third-party testing facility. In total, 7 multi-speed fans, 7 single speed fans, and 6 low-profile fans from six manufacturers were sent to REEL without manufacturer markings. In general, ten-point airflow tests were conducted on each fan. Testing adhered to standards used in the industry, namely, ANSI/AMCA Standard 210 and HVI Publications 916 and 920, where applicable. While the dataset is extensive, this paper focuses on the 50, 80, and 110 cfm ventilation rates, as these are the most common specified fan speeds for bathrooms. These fan curves show the relationship of airflow that will be delivered at various static pressures of the duct system. Figure 1 shows fan curves for single speed fans that were tested. The units are rated for 80 cfm unless noted otherwise in the legend (two are rated for 70 cfm and one for 90 cfm). While all of these fans performed in a similar manner, would it surprise you that two of the fan curves in Figure 1 are for exhaust fans that use DC motors? People often assume that all fans using DC motors are the same and result in constant airflow for a range of static pressures (let’s say up to 0.4” w.g.). It is clear in this data (Figure 1) that flow rates decrease rapidly when static pressure rises over 0.3” w.g., as it often does in real world installations. Oh, are you still wondering which two fans have DC motors? It is actually SS-05 and SS-06. A bit surprising, isn’t it? (more…) Read MoreHere’s to Our Buildings, Our Health! SWA’s Top 10 Tips for a Healthier Indoor Environment – Part 2
January 11, 2019 | Steven Winter Associates
Quick pulse survey: in the last three months, since we published our Part I blog on tips for healthier indoor environments, how many of you have either incorporated some of our healthy recommendations into your home, or informed your clients on the most effective ways to address health risks in buildings (hint: if you need a refresher, please visit Part I)? As previously discussed, there is overwhelming evidence for the business case for healthier buildings, from greater employee productivity and reduced sick days in the workplace to reduced asthma incidents and ER visits for children living in green housing. Leading organizations know that improved wellbeing helps employees to be healthier and lowers healthcare costs. It also helps employees to be more productive, creative and innovative, and less likely to leave for a competitor. The same concept can be applied to tenants in rental buildings and condos. Before we dive into health tips #6-10, here are some fun (and not so fun) facts to keep in mind while we spend winter days INSIDE our workplaces, schools and homes:
In the winter, school-aged children ages 11-17 will spend 60 minutes a day outdoors, compared to 175 minutes in the summer. (Source: Schools for Health by the Harvard TH Chan School of Public Health.)
- In a study of 73 elementary schools in Florida, students in schools cooling with the noisiest types of HVAC systems were found to underperform on achievement tests compared with students taking tests in schools with quieter systems.
- According to a recent survey released by the U.S. Green Building Council (USGBC), employees who work in LEED certified green buildings are happier, healthier and more productive than employees in conventional and non-LEED buildings:
- More than 90 percent of respondents in LEED certified green buildings say they are satisfied on the job and 79 percent say they would choose a job in a LEED certified building over a non-LEED building.
- More than 80 percent of respondents say that being productive on the job and having access to clean, high-quality indoor air contributes to their overall workplace happiness.
- 85 percent of employees in LEED certified buildings also say their access to quality outdoor views and natural sunlight boosts their overall productivity and happiness, and 80 percent say the enhanced air quality improves their physical health and comfort.
The Top 10 Party Walls Posts of 2018!
December 20, 2018 | Steven Winter Associates
2018 has been a year to remember for SWA’s Party Walls blog. Our consultants have shared their passion for high performance buildings by recounting stories from the field and providing information, new findings, and best practices to improve the built environment.
Whether discussing topics based in New York City or Southeast Asia, here are our fan favorites from 2018...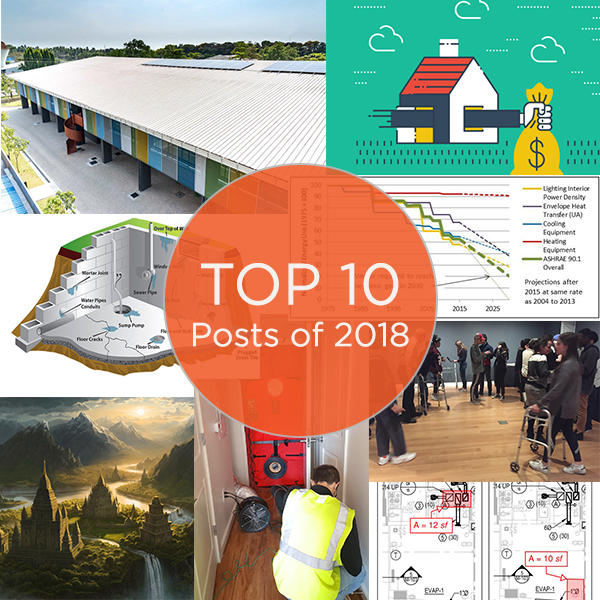
Here’s to Our Buildings, Our Health! SWA’s Top 10 Tips for a Healthier Indoor Environment – Part 1
October 17, 2018 | Steven Winter Associates
How many of you out there would say you are happy at your place of work? Are you having a hard time concentrating? Now, take a pulse on your surroundings. Are the lights too bright? Are you too cold? Too hot? Do you hear constant humming from the HVAC equipment in the background? How much sleep are you getting at night? How many plants are in your view? Do you even have a view? I’m sure many of you have heard the statistics that we spend nearly 90% of our days indoors. BUT, did you know that:
- 75% of deaths are caused by chronic disease, up from 13% in 1800;
- Today’s children are the first generation expected to have a shorter life expectancy than their parents;
- 85% of the 82,000 chemicals in use are lacking in available health data.
Does Your Exhaust Fan Suck? Part 1
September 14, 2018 |
You most likely don’t even think about it when using the bathroom. Flip the switch, hear the exhaust fan, and everything is working as it is intended…right? Far too often, the answer is NO, and it is no fault of the user. Sure, homeowners should take a minute each year to vacuum the inside of the exhaust fan housing, but otherwise, these fans should just work. So why don't they? Hint…it all depends on how it was sized and installed.
Background
The purpose of exhaust ventilation is to remove contaminants (including moisture) that can compromise health, comfort, and durability. Exhaust fans are amongst the simplest mechanical systems in your home, but decades of experience working in homes has shown us that even the easiest things can get screwed up. Far too often, exhaust fans rated for 50 or 80 cubic feet per minute (cfm) of air removal are actually operating at less than 20 cfm. In theory, the exhaust fan should be installed in a suitable location and then ducted to the outside via the most direct path possible. However, the installation of an exhaust fan can involve up to three trades: an electrician typically installs and wires the unit; an HVAC contractor supplies the ductwork; and, the builder/sider/roofer may install the end cap termination. What could go wrong? As energy efficiency standards and construction techniques have improved over time, new and retrofitted buildings have become more and more air-tight. If not properly addressed, this air-tightness can lead to moisture issues. Quickly removing moisture generated from showers is a key component of any moisture management strategy. While manufacturers have made significant advancements in the performance, durability, and controls of exhaust fans, these improvements can all be side-stepped by a poor installation. So how do you correct this issue? (more…) Read MoreJust Your Typical Blower Door Test… in Sri Lanka – Star Garment Innovation Center
August 9, 2018 | Steven Winter Associates
As the number of projects pursuing Passive House certification increases, so does the demand for whole building blower door tests. And so, performance of recent blower door tests took us to uncharted territory, not only for SWA, but for the Passive House Standard.
Working remotely with a project team across the globe, the Passive House team at SWA was tasked with retrofitting an outdated factory in Katunayake, Sri Lanka, into a Passive House certified garment manufacturing facility. Jordan Parnass Digital Architecture (JPDA) recruited SWA to provide technical assistance to the project team. Responsibilities for this project included Passive House design analysis and recommendations, mechanical design review, energy and thermal bridging modeling, and the testing and verification necessary to achieve certification from the Passive House Institute (PHI).
(more…) Read More
Reducing Air Leaks in Multifamily Buildings (and why you should care)
June 15, 2018 | Andrea Foss
If there was ever a silver bullet when it comes to best practices in multifamily buildings, air sealing would be it. Compartmentalization – or air sealing each unit to prevent infiltration between units and to the exterior – addresses many major issues we see in buildings. Better HEALTH
- Air sealing is the best strategy to keep pests out and limit their movement within a building.
- Air carries a lot of moisture, so eliminating air leaks helps keep buildings dry and reduces the risks of mold and water damage.
- Compartmentalization prevents contaminated air from garages, basements, attics, and other undesirable sources from entering living spaces.
- Air sealing reduces drafts and eliminates hot and cold spots.
- Limiting air transfer from one unit to the next reduces transmission of noise, smoke, and odor between units.
- Air sealing lowers heating and cooling bills maintaining a more consistent indoor temperature.
- Compartmentalization improves the performance of ventilation and mechanical systems by limiting pathways for stack effect – the force of warm air from low to high – to occur in larger buildings.
How to Air Seal Multifamily Units
It’s important to remember to create a complete air barrier around the entire cube of a multifamily unit, not just to the exterior – any and all penetrations need to be sealed. (more…) Read MoreMultifamily Passive House Ventilation Design Part 2: HRV or ERV?
March 14, 2018 | Steven Winter Associates
*click here to read Part 1 of this blog In climates with significant heating and/or cooling seasons, Passive House projects must have a balanced heat or energy recovery ventilation system. These systems use a heat exchanger to transfer heat and moisture between the outgoing return and incoming outdoor airstreams. The operation of recovery ventilators reduces the energy required to heat and cool decreasing the building’s carbon footprint. Project teams can select either:
- Heat Recovery Ventilators (HRV) that transfer heat from the return air stream to the outside air stream; or,
- Energy Recovery Ventilators (ERV) that transfer heat and moisture from the return air stream to the outside air stream.
Summer Condition – HRV
An HRV operating in the summer (hot-humid exterior air and cool-dry interior air) introduces additional moisture to the building through ventilation. Heat is transferred from the incoming outside airstream to the return airstream leaving the building which cools supply air, but exterior moisture is not removed from the incoming air. The building’s dehumidification load increases as a consequence of additional moisture from the outdoor air.*CON*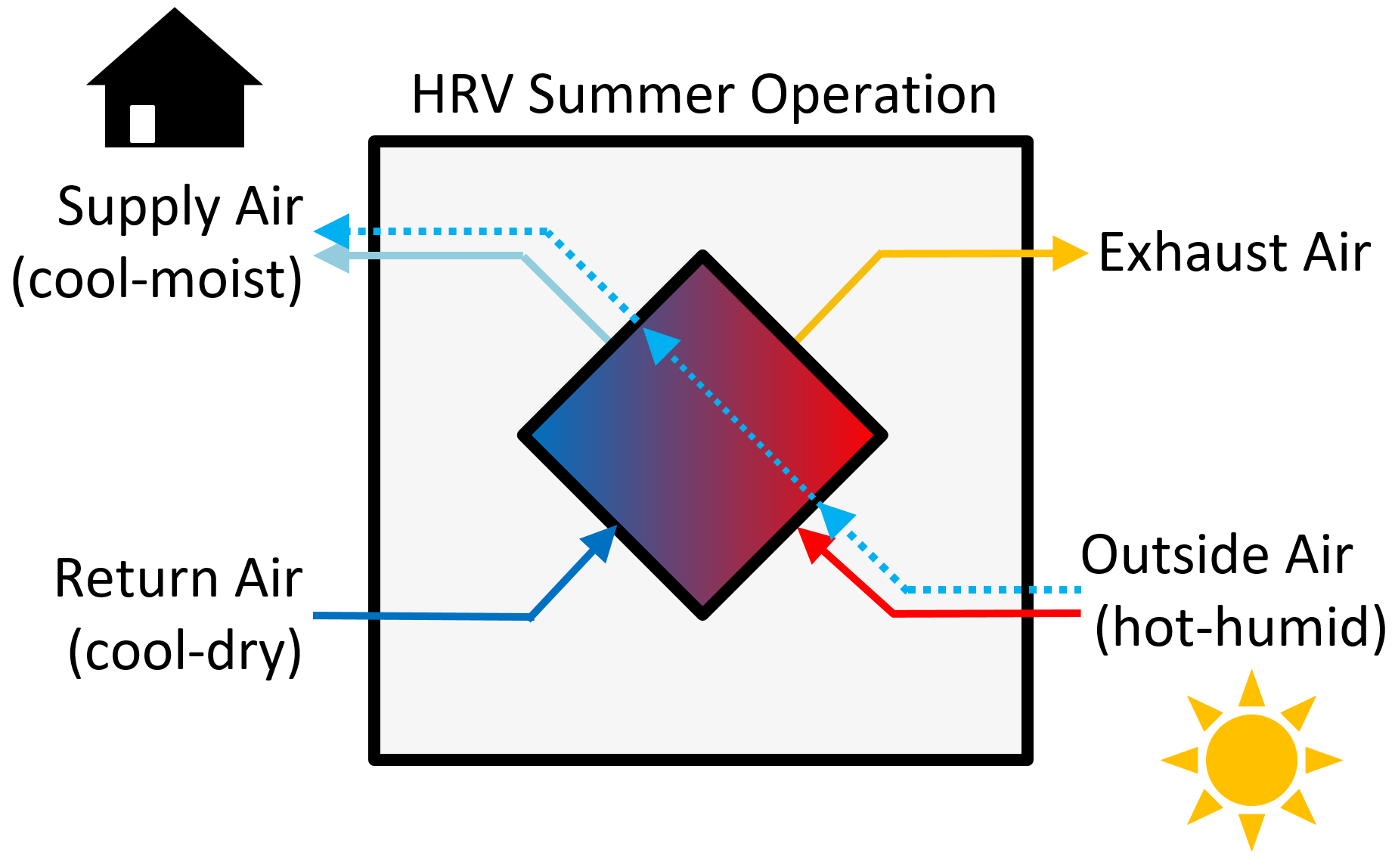
Multifamily Passive House Ventilation Design Part 1: Unitized or Centralized HRV/ERV?
February 6, 2018 | Steven Winter Associates
*click here to read Part 2 of this blog Project teams pursuing Passive House frequently ask, “Where do we locate the HRV/ERV?” The answer is complex when the Passive House concept is scaled to a multifamily program. While there are two primary arrangements for HRV/ERV systems, the trade-off is dynamic and needs to be carefully considered as multifamily Passive House projects begin to scale. A low volume HRV/ERV unit ventilating an individual apartment is a unitized HRV/ERV. High volume HRV/ERV units ventilating multiple apartments and often servicing several floors, is referred to as centralized HRV/ERV. As Passive House consultants we can attempt to address the system arrangement question with building science; however, in New York City rentable floor space is very valuable, so considering the floor area trade-off is of particular interest to project teams. When a unitized HRV/ERV system cannot be located in a drop-ceiling due to low floor-to-floor height, it is placed in a dedicated mechanical closet. This closet is typically no smaller than 10 ft2 and includes the necessary ductwork connections to the HRV/ERV unit. The alternative solution is to increase the floor-to-floor height to accommodate the HRV/ERV unit and horizontal duct runs in the ceiling. Centralized HRV/ERV systems, however, allow short horizontal duct runs but require floor space to accommodate vertical shafts. With supply and exhaust ducts coupled together the required floor area is about 8-12 ft2. As a result, centralized HRV/ERV systems may actually require more floor area than a unitized system.
Example: In the case of Cornell Tech, vertical supply and exhaust duct work for the centralized HRV/ERV system required 222.5 ft2 per floor, or 13 ft2 per apartment (see image 1 below). Unitized HRV/ERV mechanical closets would have required an estimated 170 ft2 per floor, or 10 ft2 per unit (image 2 on right).
Image 1 & 2: These images compare the amount of floor area required for centralized and unitized HRV/ERV systems. Image 1 on the left, shows the 12ft2 floor area required for vertical shafts servicing the centralized ERV at Cornell Tech. Image 2 on the right is hypothetical, showing the typical location and 10ft2 floor area required for a unitized HRV/ERV mechanical closet.
Read MoreVentilation Idyll
January 8, 2018 | Robb Aldrich
Residential ventilation is really a tricky topic. But if you’re looking for a practical, cost-effective, holistic solution, go somewhere else. This post offers none. Hopefully I can dig into practical solutions in future posts, but I think it’s important to be clear about why we ventilate and what an “ideal” ventilation system might look like in a new, efficient home. My ideal system is similar for both single-family or multi-family (though practical issues can be very, very different). Purpose of ventilation: Remove contaminants that can compromise health, comfort, productivity, durability, etc. I’m sure there are more rigorous definitions out there, but this will work for now. There are other ways to lower contaminant levels:
- Emitting fewer contaminants from materials and activities is obviously good. Do this.
- Actively filtering, adsorbing, or otherwise removing contaminants from indoor air can also be good. There’s talk about doing more of this, but I’m tabling it for this discussion. This may be something to keep an eye on down the road.
Which LEED Rating System Do I Use? NC versus Midrise (Part 2)
December 19, 2017 | Steven Winter Associates
Here’s a question that we’re often asked by our clients: “I’m building a new residential building, should I use LEED for New Construction (NC) or LEED for Multifamily Midrise (MFMR)?” The answer isn’t exactly simple, especially with the introduction of new credit requirements in LEED v4 and the fact that USGBC allows project teams to choose between the two rating systems. Ultimately, it will come down to a difficult decision based on the goals and final design of the project. So, in an effort to help clear up the confusion and possibly make the decision a little easier for you, we decided to break down a few scenarios that highlight key differences between the rating systems that may not be apparent upon first glance.
In our first installment, we took a look at a four story multifamily building and highlighted many of the key differences between the rating systems; you can find that post here. In this edition, we will explore the options for a different building type.
(more…) Read More
Recovering from Heat Recovery Woes
November 16, 2017 | Steven Winter Associates
The International Energy Conservation Code (IECC) has a number of requirements involving energy recovery on ventilation systems. Requirements vary based on climate zone, building type and size, equipment capacity, and equipment operating hours. As a result, many new construction projects must now incorporate energy recovery considerations into their design.
An energy recovery unit (ERU) equipped with a heat wheel can be a great way to satisfy these energy recovery requirements. The ERU can be a roof-mounted air handling unit, or can be an air handling unit located inside a mechanical room with outdoor air and exhaust streams ducted in. The heat wheel is positioned so that half of the wheel sits in the exhaust air duct and the other half sits in the outdoor air intake duct. During cold weather, the wheel spins, transferring heat from the exhaust stream to the outdoor air intake stream. During hot weather, the wheel transfers heat from the outdoor air intake stream to the exhaust stream. In both cases the heat exchange enables the building to take advantage of the more comfortable conditions of the exhaust air, while still allowing fresh air to enter the building. During extreme weather conditions, heat wheels can save energy on space conditioning while still allowing for healthy indoor air quality.
(more…) Read More
When the Rubber Meets the Road
October 24, 2017 | Steven Winter Associates
As the Passive House standard continues to make waves across New York City and the U.S., an entirely new design process has evolved to respond to the challenges of higher insulation levels, balanced mechanical ventilation, and perhaps the most difficult hurdle – an air tightness level that most would think is impossible. For the recently certified Cornell Tech building on Roosevelt Island, the tallest Passive House in the world, a several year-long coordinated effort was required to achieve such a feat. So what is the requirement, how is it measured, and what are the strategies and considerations required to achieve it?
(more…) Read More
Designing Solar for High Density Areas
September 7, 2017 | Steven Winter Associates
As seen in:
Humans have been trying to harness the power of the sun for millennia. The advent and popularization of photovoltaics in the latter half of the twentieth century made doing so accessible to the masses. Today, solar arrays are commonly seen adorning the roofs of suburban homes and “big-box” retailers, as well as on other landscapes including expansive solar farms and capped landfills. Until recently, the common thread amongst these locations has been the employment of open space. Solar applications have historically been reserved for use in areas of low-to-moderate building density. By the end of 2050, solar energy is projected to be the world’s largest source of electricity. While utility-scale solar will comprise the majority of this capacity, there will also be significant growth in the commercial and residential sectors – particularly in cities. Industry influencers are increasingly focused on creating opportunities for solar applications in high-density areas, where much of the demand lies.In their 2014 Technological Roadmaps for solar PV and solar thermal electricity (STE), the International Energy Agency (IEA) predicts Solar PV and STE to represent over 25% of global electricity generation by 2050.
#UnfreezePA: SWA at the Helm of the PA Icehouse Demonstration
June 19, 2017 | Andrea Foss
On Tuesday, June 6, 2017, leaders of Pennsylvania’s clean energy movement took to the steps of the State Capitol Building. The cause? To demonstrate just how much room PA State Energy Codes have to improve. Amidst a cohort of speakers and presenters, USGBC’s Central Pennsylvania chapter erected two sheds, each filled with 1,080 pounds of ice: one built to 2009 Code requirements, currently in place under PA state law; and the other built to Passive House standards. Over the course of the month of June, the public will be able to watch as the respective blocks of ice melt within their structures. Ultimately, the difference in the rate of ice melt between the Code House and the Performance House (Passive House) will illustrate the degree to which current energy laws and codes are lacking, while simultaneously offering a model for advancement. In 2009, the International Energy Code Council (IECC) developed energy-saving standards that were adopted by most U.S. state governments. While the 2009 Code was widely instituted in the period following its publication, several states have since embraced even more efficient requirements that are quickly replacing outdated terms. For instance, the state of Maryland – comparable to Pennsylvania in terms of climate, population, and demographic spectrum – is operating under requirements equivalent to 2015 IECC standards. New York, New Jersey, Massachusetts and Vermont are other states in the same geographic region and general climate zone that have opted towards more energy efficient codes.[1] Passive House, on the other hand, is a set of design principles that aim to attain a “quantifiable and rigorous level of energy efficiency within a specific quantifiable comfort level.[2]” More simply, Passive House projects go above and beyond the statutes of any enforced codes to follow a “maximize your gains, minimize your losses” approach to building design. The Passive House Institute of the United States (PHIUS) provides the following summary of Passive House principles: (more…) Read More
Which LEED Rating System Do I Use? Part 1: NC versus Midrise
May 10, 2017 | Steven Winter Associates
Here’s a question our clients often ask: “I’m building a new residential building, should I use LEED for New Construction (NC) or LEED for Multifamily Midrise?” The answer isn’t exactly simple, especially with the introduction of new credit requirements in LEED v4 and the fact that USGBC allows project teams to choose between the two rating systems. Ultimately, it's often a difficult decision based on the goals and final design of the project. So, in an effort to help clear up the confusion and possibly make the decision a little easier for you, we decided to break down a few scenarios that highlight key differences between the rating systems that may not be apparent upon first glance. In this first installment, we’ll start with a smaller multifamily building to get a sense of the essential differences between the rating systems and begin to understand the critical decision-making points.
(more…) Read More
Solar Photovoltaics and New York Energy Code
March 20, 2017 | Steven Winter Associates
Industry Trends
Over the past decade, the story of solar photovoltaic (PV) power has been one of both accelerating deployment and consistent, significant reductions in cost. This success has been driven by increasingly advantageous economies of scale, and supported by incentives and initiatives at all levels of government. In late 2015, the federal Investment Tax Credit [3], a primary financial incentive for solar PV systems, was extended at its current rate of 30% through 2019, despite a contentious environment in Washington. It is scheduled to be stepped down through 2022, after which the commercial credit will expire and the residential credit [7] will remain at 10% indefinitely. The National Renewable Energy Laboratory’s annual solar benchmarking report [4] shows that over the past seven years, PV system costs have dropped 58.5% in the residential sector, 59.3% in the commercial sector, and 68.2% in the utility-scale sector. As a clear sign of the times, utility-scale solar achieved the U.S. Department of Energy (DOE) SunShot Initiative’s goal of $1.00/W early this year, three years ahead of schedule [9]. According to the U.S. Energy Information Agency (EIA) [8], these trends should continue, leading to solar power’s increasing presence as a key component of the national electrical generation mix. The EIA projects solar to be the fastest growing form of renewable energy, increasing by 44% by the end of 2018 for a total deployed capacity of 31 GW and accounting for 1.4% of utility-scale electricity generation. (more…) Read MoreOh, the Weather Inside is Frightful!
December 9, 2016 | Steven Winter Associates
Winter in the City
Wintertime in New York City: cold wind whips down the avenue and seems to follow you as you leave the frozen street and enter your building. The cold gust pulls the heat out of the lobby and even seems to follow you as you make your way up the building, whistling through the elevator shaft as it goes. The colder it gets outside, the worse it gets inside. Can’t somebody please make it stop? Is it too much to ask to be comfortable in your own lobby? No, it is not too much to ask, and yes, we can help. It is 2016 and we have the technologies and expertise to better manage this all-too-common problem, but first we must examine what forces lay at the heart of the issue.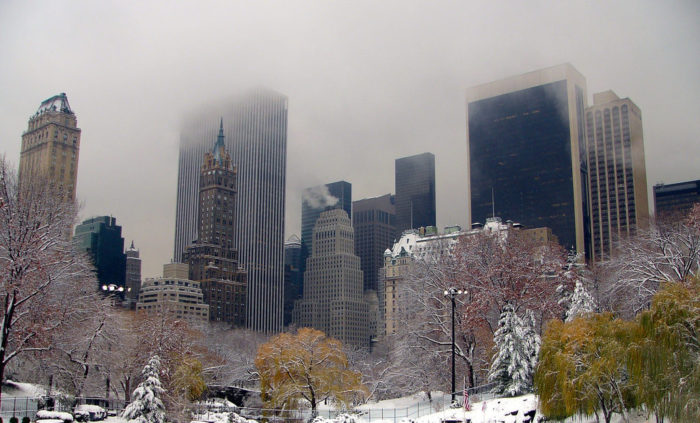
Passive House is Here to Stay and This is Why
September 9, 2016 | Steven Winter Associates
In recent years, the Northeast and Mid-Atlantic regions have seen a tremendous increase in interest in Passive House buildings. It’s not only in the news; here at SWA we have experienced a dramatic increase in requests for Passive House. The Pennsylvania Housing Finance Authority (PHFA) now includes a 10 point incentive within its Qualified Allocation Plan to developers of affordable, low-income tax credit projects that design to Passive House standards. In New York City, public initiatives like SustaiNYC have spurred a mixed-use project that will likely result in the largest Passive House building in the world. Other public initiatives, like the reopening of NYSERDA's MPP program, carve out funding exclusively for Passive House projects. The emergence of singular and iconic Passive House projects, such as Cornell Tech – which, upon completion, will be the largest and tallest building with this certification in the world – have also boosted interest. It is clear that as code is made more stringent across the country, the gap between basic compliance and Passive House certification will shrink, making it more attractive for developers. (more…) Read More
Green Building Targets the Indoor Environment, as Health Becomes Top Priority
May 17, 2016 | Heather Breslin
In SWA's second contribution to Green Energy Times, we examine the certification programs, operational strategies, and occupant behavior trends that contribute to enhanced indoor air quality (IAQ). The full article is featured below, or on page 29 of the April-June edition of Green Energy Times.
(more…) Read More
Popular Multifamily Retrofits, Pt III
May 5, 2016 |
In the first two entries of this series (Part One | Part Two), we explored advanced controls for electrically heated buildings; combined heat and power systems; upgraded atmospheric boilers and ventilation systems. For the final installment of SWA’s Favorite Multifamily Retrofits, we’ll examine the ins-and-outs of stand-alone energy storage. (more…) Read More
It Can Take Years – A Market Adoption Story
March 31, 2016 | Heather Breslin
Earlier this year, at the AHR Expo in Orlando, the biggest trade show for HVAC professionals, Aeroseal’s duct sealing technology was declared the Product of the Year, the top honor of the Innovation Awards. Aeroseal was recognized as “a groundbreaking solution to an industry-wide problem.” The unique appeal of the Aeroseal technology is that it seals ducts from the inside. Walls and ceilings do not need to be removed or damaged to gain access for traditional mastic sealing. Aerosolized vinyl polymer particles from 2 to 20 micrometers are injected into a pressurized duct system. The particles stay suspended in the air stream until they reach the leaks, where they are deposited and built up at the leak edges until the leaks are sealed. The Aeroseal technology has been around for more than two decades. It was developed at Lawrence Berkeley National Laboratory in the early nineties and patented in 1997. It has received many awards over the years including the Best of What’s New award from Popular Science magazine in 1996 and the Energy 100 award from the U.S. Department of Energy.
So what’s the big deal?
(more…) Read MorePopular Multifamily Retrofits, Part II
March 17, 2016 |
In our first entry of this three-part series, we described advanced controls for electrically heated buildings, combined heat and power systems, and upgraded atmospheric boilers. This time around, we’ll examine the ins-and-outs of exhaust ventilation in multifamily buildings. (more…) Read More
Popular Multifamily Retrofits, Part I
January 14, 2016 |
There is no single retrofit that is a panacea for all multifamily buildings. There are myriad options and permutations for upgrades, the efficacy of which is defined by the operational needs, budget, and goals set by the owner. With that in mind, we will examine six retrofits popular with SWA clients in this three-part blog series. (more…) Read More
Examining Green Building Rating Systems
September 3, 2015 |
Earning a green building certification is a significant achievement for a project as it represents a strong commitment to sustainability principles. When pursuing certification, it is essential to select the rating system best suited to your project type and performance goals.
In this blog piece, we will examine the anatomy of five popular green building rating systems, including their applicability to building type and a brief summation of typical advantages and challenges faced by clients pursuing certification. (more…) Read More
Creating a Healthier Indoor Environment
July 29, 2015 | Steven Winter Associates
When close to 90% of our lives are spent inside, you would expect extensive measures would be taken to ensure our buildings provide healthy environments in which to live and work. Unfortunately, more often than not, tested air quality inside buildings is much worse than outside. Here are some common causes of these indoor pollutants:
- Pesticide use during regular pest control treatments
- Pollutants (asthma triggers) from cleaning products, smoking, pets, pests, fuel use, etc;
- Inadequate ventilation;
- Mold and moisture build up from water leaks and inadequate ventilation; and,
- Carbon monoxide from appliances, heaters or other equipment.
Air Sealing with Open Cell Spray Foam Insulation – Know the Risks
April 29, 2015 |
As the latest versions (2012 and 2015) of the International Energy Conservation Codes (IECC) push for more efficient homes, we are getting more questions from architects on how to achieve the air tightness requirements of 3 ACH50. There is no one correct answer, but it can be often achieved through taping of exterior structural or insulated sheathing, air sealing of wall cavities prior to insulating, and/or the use of insulation that is restrictive of air movement. The most common approach that we are asked about is the use of open cell spray polyurethane foam (ocSPF), as it is air impermeable (required thickness is dependent on the specific product, so check requirements in the ICC Evaluation Services Report), reasonably priced, and theoretically, doesn’t require any changes to standard builder practices. While it is true that ocSPF will provide air sealing cost-effectively, we typically do not recommend it in our cold climate region without additional measures due to risk potential over time. To effectively build a home with ocSPF, thoughtful detailing and a high level of execution is required to ensure that it remains effective 5, 10, 15…25 years from now.
- ocSPF is vapor permeable, so there is a greater potential for condensation in the building enclosure than if closed cell spray polyurethane foam (ccSPF) is used. A hybrid approach of ccSPF and an alterative insulation (ocSPF, cellulose, fiberglass, etc.) is often used to keep costs down.
- ocSPF can absorb 40% of water by volume. Therefore, if bulk water from leaks does make it into the building enclosure, the ocSPF will retain the water until saturated. Pinpointing the source of the leak may be difficult as the water can migrate within the foam.
Make-Up Air or “Made-Up” Air?
September 9, 2014 | Heather Breslin
In multifamily buildings, particularly in the Northeast, exhaust ventilation strategies are the norm as a method for meeting both local exhaust and whole-unit mechanical ventilation. We can easily measure that air is exhausted. What we don’t know is where the make-up air is coming from… Is it “fresh” from outside, from the neighboring apartment, from a pressurized corridor, or the parking garage via the elevator shaft? Well-intentioned design teams are providing fresh air in many forms, ranging from fully-ducted systems that deliver air directly to apartments, to more passive systems utilizing designed penetrations in the envelope such as trickle vents or fresh air dampers. With funding from DOE’s Building America program, SWA is conducting field research in several multifamily buildings with different types of mechanical ventilation systems to assess how make-up air is provided under the variable pressure conditions that can occur throughout the year. The Approach Even though it does not comply with fire codes in at least some jurisdictions, SWA‘s approach is to leave a gap under the apartment door to allow make-up air to enter from the corridor. The general strategy is to pressurize the corridor using outside air and depressurize the apartments through local exhaust. This strategy is being assessed in a 3-story, 78 unit building, where the design called for 5,250 CFM of supply air to the corridors and common areas and a total of 4,980 CFM of exhaust from janitor’s closets, and trash rooms, and continuous exhaust (30-50 CFM) from each apartment. Measuring the Airflows In order to extrapolate airflow measurements based on the varying conditions in the building, SWA measured airflows across the apartment door under normal operating conditions for eight apartments. Our team also monitored the pressure differential between the corridor and apartment over a two-week period for five apartments in the building. Here’s a “Snapshot” The measurements in the eight apartments showed that while exhaust fans were measured to continuously exhaust 30-40 CFM, the flow into the apartments through the doors ranged from 0 CFM to only 28 CFM. When bathroom exhaust fans in the apartments were activated to their “high” setting ( ~90 CFM each), the flow through the doors increased to an average of 37 CFM, still indicating that a majority of the make-up air is not from the corridor. The long-term measurements in the five apartments showed airflow across the door into one apartment to max out at 24 CFM. The other four exhibited net airflow from the apartment into the “pressurized” corridor, as much as 40 CFM! Why?! One potential reason: measured supply and exhaust flows in the corridors showed that the supply systems were 25% lower than design and exhaust from the trash rooms was 25% more than design. Stay tuned for a future post on our findings and recommendations. Read More
Can A House Be Too Tight?
July 1, 2013 | Andrea Foss
The Importance of Mechanical Ventilation
During most presentations we give about air sealing and infiltration, like clockwork someone will ask, “but doesn’t the house need to breathe, aren’t we making buildings too tight?” This is a popular green building myth, but people need to breathe, walls don’t. In fact buildings perform best when they’re air tight and we can temper, filter and regulate the amount of fresh air.
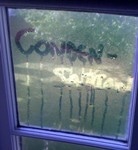
Natural Ventilation Doesn’t Work Anymore
In the past buildings were ventilated with outside air naturally when the wind blew and/or it was cold. If this natural ventilation (or what building professionals call air infiltration) ever worked it doesn’t anymore.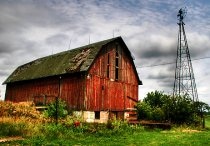
"Did you grow up in a barn?" Most of us learned as children the importance of keeping outside air out during heating and cooling seasons. However natural ventilation through building cracks brings unintended moisture and temperature differences that can cause condensation.
Old buildings had no insulation or air sealing, so structural failures caused by condensation within a wall assembly rarely occurred. Building codes now require insulation and air sealing which helps lower our energy bills and keep us comfortable inside. But when infiltration happens in a wall full of insulation, condensation can occur on the cool side of the wall assembly, which over time can rot the framing and cause structural issues. This is why it’s critical to prevent air leaks and better understand the thermal boundary. Americans spend more time in our homes than ever, almost 15 hours per day by some estimates, and humans give off a lot of moisture. While home we tend to keep the windows closed. We’re also seeing increasing amounts of Volatile Organic Compounds (VOCs) emitted from our paints, furniture and household products that are made with chemical compounds that we know little about. For example, solid-wood furniture does not offgass, but plywood, particle board and foam sure do. How much solid wood furniture do you have in your house? Taken together this means there is more moisture, odors and pollutants added to our homes each day than was the case 30 years ago. The EPA estimates indoor pollutants to be 2 to 5 times higher inside homes than outside.Because of all these indoor pollutants, we clearly need to bring fresh outdoor air into the house. However, the unintentional natural ventilation air our buildings do get rarely comes directly from outside. In the best-case scenario it creeps in through the various cracks in the exterior walls and windows, but most often comes from the least desirable locations shown in the image below: crawlspaces, garages and attics. Leakage from those locations is certainly not “fresh” air. Do you want to breathe in hot dusty attic air, or damp air from your crawlspace? You just might be.Moreover, unintentional natural ventilation (infiltration) is unreliable and poorly distributed. Infiltration is primarily driven by wind speed and the temperature difference between outdoors and indoors. These weather variables vary day-by-day and season-to-season. For instance, the chart below shows the average conditions for Lancaster, PA. Note the weather fluctuations throughout the year:
- During summer wind speeds are almost 50% lower
- The temperature difference is 6-8 times greater during winter

These erratic conditions cause the building to be over-ventilated half the time and under-ventilated the other half. Also, infiltration is poorly distributed throughout the house. A room with a couple exterior walls and leaky windows will get far more outside air than an interior kitchen or bathroom. Wind and temperature differences drive ‘natural ventilation’ in the form of infiltration in homes. However these factors are highly variable and unreliable.
To summarize the need for mechanical ventilation:
- There are more pollutants in our homes than ever, requiring more ventilation air
- Homes are better insulated and air sealed than they used to be
- Much of the infiltration that does occur comes from undesirable locations
- Even the portion of infiltration that can be considered “fresh air” varies sporadically based on weather conditions
- Having air leaks in an insulated wall, attic or floor assembly can cause condensation and create structural failures.
Build It Tight, Ventilate It Right
The better approach is to provide controlled mechanical ventilation by providing enough air to meet ASHRAE 62.2 and air seal the house to prevent moisture issues, high energy bills, and air from the attic and crawlspace or basement from polluting our indoor air. As the mantra goes, “build it tight, ventilate it right!” A well-designed ventilation system brings several advantages.- It allows control over exactly how much fresh air is delivered and when.
- You can adjust the amount of ventilation air if the occupancy changes (e.g. kids go off to college) or shut it down altogether while on vacation, or when windows are open.
- It delivers a consistent amount of air year-round, no matter what the weather conditions.
- It draws air directly from outside, so the air is guaranteed to be fresh.
Mechanical Ventilation Case Study
Consider the following single family detached home renovation project in Lancaster, Pennsylvania. Before renovation, the house had no mechanical ventilation, and much of the infiltration air came from the attic and basement, providing dirty air to the house. The house was leaky enough to meet ASHRAE 62.2 levels for natural ventilation. But with an infiltration rate of 1.1 air changes per hour, the house was replacing all its indoor air every hour, leading to huge heating bills. During the renovation air sealing brought the infiltration down by 70% and mechanical ventilation was added to deliver the recommended ventilation rate, which in this case was 0.20 ACHn.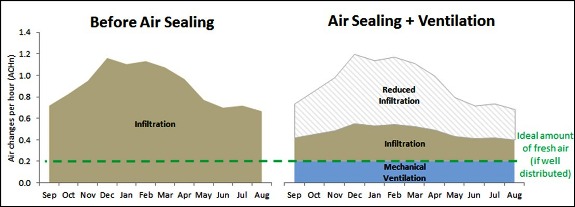
Looking at the annual utility bills, in the original house it cost almost $600 per year to heat the infiltration air. After air sealing this was cut to $217. Heating the ventilation air cost $174, and running the fan cost an additional $14 per year. Not only is the house now less drafty and more comfortable, the indoor air quality is substantially better AND the homeowner is saving $194 per year.
Not every case follows this same savings ratio. If the original house was tighter to begin with there may not have been any theoretical savings. If the mechanical ventilation system were more efficient, there could be more savings. But remember that mechanical ventilation puts the control in the hands of the occupant, not mother nature. If there seems to be too much ventilation, the occupant can dial it back. If there are indoor air concerns the occupant can increase the rate.Designing an Effective Mechanical Ventilation System
There are several strategies for designing a good mechanical ventilation system, and there isn’t a one-size fits all approach for homes, multifamily buildings and commercial spaces. It’s important to keep occupants in mind and install the proper controls to make the system work for them. Everyday Green has helped MEPs and HVAC contractors select and size mechanical ventilation systems for all budgets and size buildings, homes and unit spaces. But one thing is clear: relying on air leaks to provide fresh air is no longer an effective strategy. Contact us today with your mechanical ventilation questions.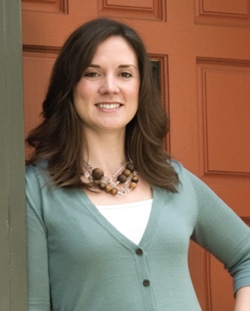
Getting it Right – HVAC System Sizing in Multifamily Buildings
May 22, 2013 | Andrea Foss
Properly Sizing Mechanical Systems in Multifamily Buildings
Multifamily buildings can be a unique challenge when it comes to selecting effective heating and cooling systems. In the Washington, DC region’s mixed-humid climate, humidity control becomes a central challenge because of a couple inescapable realities.- There is a lot of moisture added per square foot from cooking, bathing and even just breathing due to the dense occupancy.
- The small exterior envelope areas mean the air conditioner won’t kick on very often, and thus won’t have a chance to remove moisture.
Steps to Right-Sizing Mechanical Equipment
- Perform accurate calculations using the Manual J process to estimate peak heating and cooling loads
- Consult the manufacturer’s performance data at design conditions, and
- Select the smallest piece of equipment that will meet the load.
Common Problems When Sizing Mechanical Systems
“Can’t I just use the worst-case orientation?”
“Can I use commercial software?”
Yes, but you have to be careful. Commercial load software like Train TRACE and Carrier’s HAP are primarily geared towards non-residential space types that have very different use profiles. For instance, in an office setting you would expect lighting and equipment to be 100% on during the peak afternoon cooling hours. However, in a residential setting few if any lights are on during the day. The commercial programs also like to include more outdoor air than you actually see in apartments. A reasonably well-sealed apartment will have very little natural outdoor air infiltration (remember only 1 or 2 sides of the apartment “box” are actually exposed to outside) and mechanical ventilation should only be about 20-35 CFM depending on the size of the unit. It is not uncommon for loads to drop by half once those inputs are corrected.“Will small systems have enough power to get the air to all the rooms?”
“Doesn’t each room need 100 CFM of airflow for comfort?”
Well, maybe. Is 100 CFM what the load calculations show is needed? There is no such thing as a minimum airflow threshold for each room. The amount of air required is in direct proportion to that room’s heating and cooling load. If the calculations show a small load and only 40 CFM required you should supply 40 CFM. In fact, oversupplying 100 CFM will actually cause discomfort since that room will always be a few degrees off from the rest of the apartment. Sitting under an oversupplied register could be loud and drafty as well.“But can’t I just size by bedroom count?”
No, rules of thumb don’t cut it anymore. For buildings built to 2009 or 2012 code in our climate zone (CZ4), most apartment units will have loads less than 1.5 tons, no matter how many bedrooms. There may be a few 2-ton or (rarely) 2.5-ton systems for larger apartments on the corner or top floor, but those are the exception. If your mechanical plans show 1.5 tons for all 1 bedrooms and 2 tons for all 2 bedrooms it probably means- Accurate sizing procedures were not followed, and
- A lot of those 2 bedrooms actually only need 1.5 ton systems