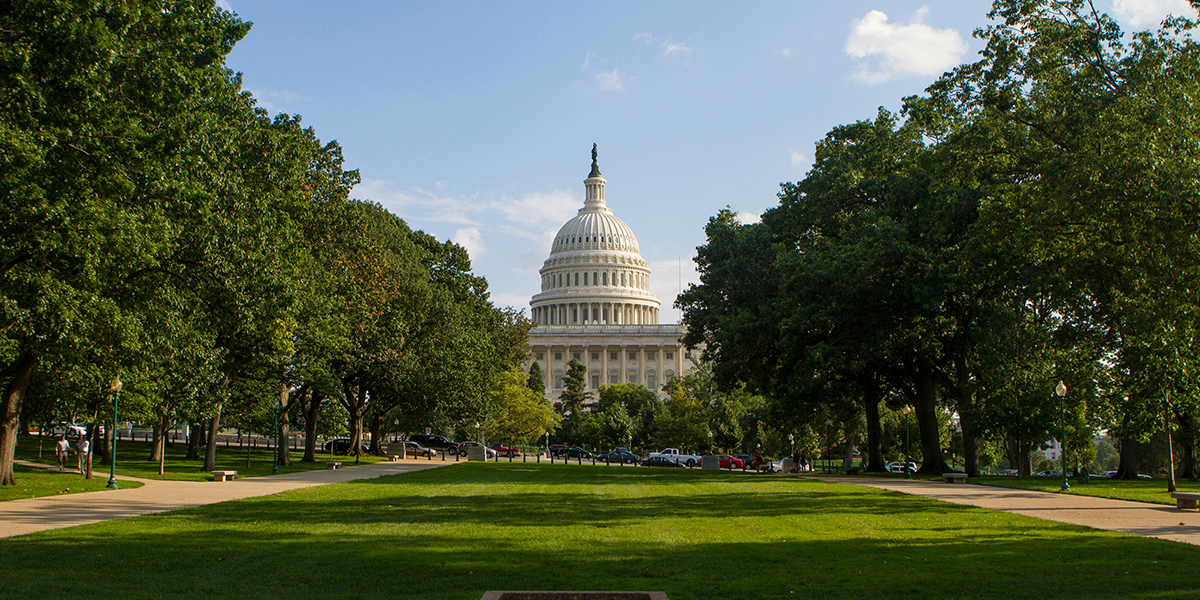
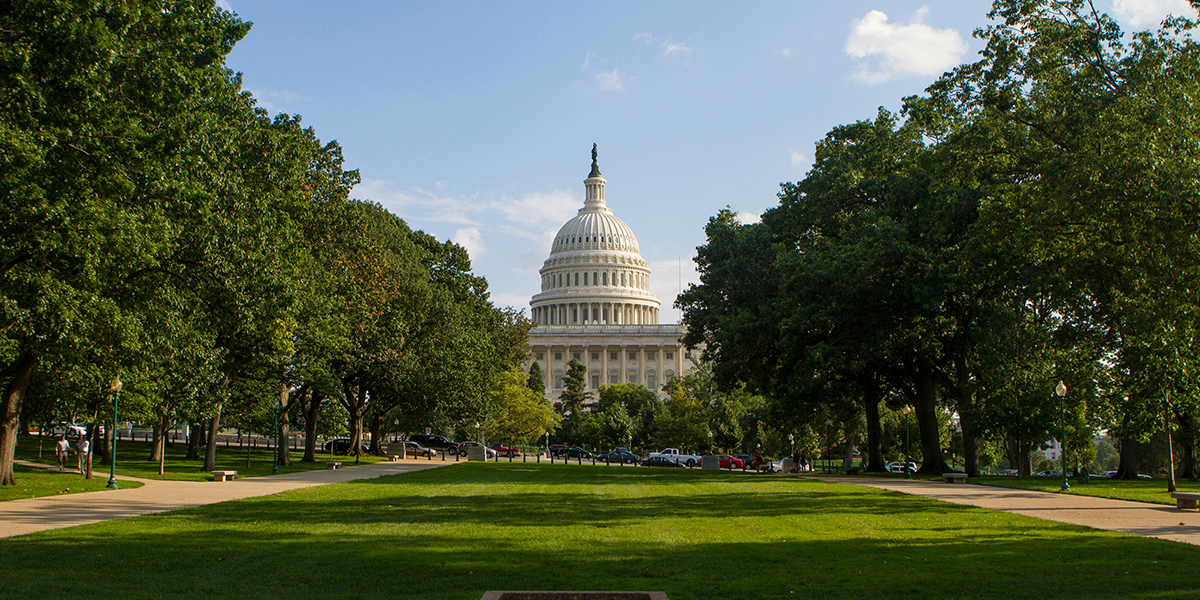
Blog
Across North America, more States, Provinces, and Municipalities are integrating PH into their building standards. One of the more recent adopters is the City of Toronto.
It is clear to see that the Passive House (PH) standard is here to stay! Across North America, more States, Provinces, and Municipalities are integrating PH into their building standards. One of the more recent adopters is the City of Toronto. In the most recent version of the Toronto Green Standard (TGS), the PH standard is offered as an alternative compliance path to TGS Tier 3, and with this alternative compliance path one obvious question comes to mind: What is the major difference in required component efficiency for a multifamily building in Toronto that is looking to meet either the PH standard or TGS Tier 3?
The PH standard is performance-based and is focused on decreasing whole building energy demand, improving building durability, providing optimal occupant thermal comfort, improving indoor air quality, and reducing carbon emissions. The PH standard reduces building operation costs, decreases carbon emissions, and supports an improved indoor environmental quality for building occupants. The TGS has similar goals and benefits when compared to the PH standard, and there are some obvious synergies in the program design between TGS and PH. The tiered energy category in the TGS takes a similar approach to PH by offering an annual budget for three different categories. For PH you must comply with a total energy budget for annual heating demand, annual cooling demand, and total source energy use intensity. Similarly, but slightly differently, the TGS offers a budget for total site energy use intensity (TEUI), annual heating demand or Thermal Energy Demand Intensity (TEDI), and the additional category of Greenhouse Gas Intensity (GHGI). In both standards, the path to compliance is non-prescriptive and designers can implement a variety of component efficiencies and system options. See table 1 and 2 below:
At a glance, the TGS Tier 3 and the PH standard have a similar performance-based approach. However, there are differences in energy budgets, modeling software, and other program protocols. We wanted to understand the major differences in required component efficiency for a multifamily building trying to meet either the PH standard or TGS Tier 3. Research and comparative normalized energy modeling indicate that there is considerable overlap between the TGS Tier 3 standard and the PH standard, see figure 1 below.
Both the TGS Tier 3 and PH compliant buildings may need VRF heating and cooling, heat/energy recovery ventilation with common area demand controls, common area LED lighting with sensors, and a selection of high efficiency motors and pumps. However, to meet PH over TGS Tier 3, the building may need a slightly improved envelope system. A modest jump from an R-20 wall and R-30 roof to an R-30 wall and R-40 roof may be needed for PH in Toronto. Additionally, the PH building will need an improved tripe glazed window system with a high-performance window frame. The jump into a triple glazed high performance windows represents a component cost increase over TGS Tier 3. However, this cost increase can be controlled by selecting a lower cost uPVC PH window frame option over an aluminum PH window frame. Overall, it seems that the PH standard will require some improvements to component efficiency when compared to TGS Tier 3. However, there are additional benefits of PH over TGS Tier 3 that should be considered in this comparison. These benefits relate to envelope durability, thermal comfort, indoor air quality, acoustics, and quality assurance.
The PH standard requires a robust building envelope design and does not allow any condensation or potential mold issues. In the PH design process, the wall assemblies and major connections are analyzed for cavity and surface condensation potential using 2-dimensional and 3-dimensional heat transfer software. All analyses of major building connections are then submitted to a third-party PH certifier for review and approval. This is an additional quality assurance check on the building envelope design beyond TGS Tier 3 that promotes long-term building envelope durability. Further, the PH standard recommends an air infiltration rate that is more stringent than TGS Tier 3. The PH standard recommends an infiltration rate of 0.033 CFM/ ft² of envelope area for large buildings. This low air infiltration rate reduces the amount of air infiltrating/exfiltrating the building assemblies, decreasing condensation risk and improving durability.
The PH standard has very rigorous pass/fail comfort criteria that are analyzed in detail during the design process. For PH compliance the design must maintain a low window u-value and surface temperature difference of ≤ 4°C to ensure thermal comfort. Additionally, all major building connections are analyzed in detail to ensure that interior surface temperatures are maintained at/or above 16°C. The benefit of these thermal comfort criteria is that consistent surface temperatures are maintained inside. As a result, convective drafts near the windows and walls are decreased. Simply put, this improves occupant experience.
To promote improved indoor air quality, the PH standard recommends an air infiltration rate of 0.033 CFM/ft² of envelope area. This is allied with a balanced ventilation system wherein total supply and exhaust air flow rates must be balanced within 10% of each other, and design air flow rates are maintained during building operation by volume regulators. The balanced ventilation system, combined with a very low air infiltration rate ensures that the breathing air is not coming from unknown locations, such as through the building assembly where it may pick up pollutants. In addition, the supply air to occupied spaces is typically filtered with a MERV 8 to MERV 13 air filter. This balanced ventilation system is developed as part of the PH design and mechanical review process, where unique attention is paid to flow rates, supply and exhaust locations, balancing components, duct sealing, and air filtration. The PH balanced ventilation system design promotes a high level of indoor air quality for occupants.
The PH design concept emphasizes air sealing details, continuous exterior over-insulation, and triple pane air tight windows. When these systems and components are combined, an acoustic barrier is produced that dramatically reduces the interior ambient noise level, along with street level noises being reduced. When compared to a TGS Tier 3 building the PH building should provide a quieter indoor environment.
The PH design is typically completed with a third-party PH Field Verifier to provide both initial on-site contractor training and oversight through construction. The PH Field Verification process gives ownership an additional layer of quality assurance and control during construction by protecting the design details from poor installation. The PH Field Verifier and standard provide an additional level of construction quality assurance beyond the TGS Tier 3.
There is considerable overlap between the envelope components and systems that are needed for both PH and TGS Tier 3. However, it is anticipated that the PH standard would require improved component efficiencies over TGS Tier 3 for a multifamily building in Toronto, Canada. Namely the PH standard would require slightly higher R-value opaque components, and triple glazed high-performance fenestration. Moreover, there is additional value in the PH standard over TGS tier 3 that should be considered as it relates to envelope durability, indoor environmental quality, and construction quality assurance.
Contributor: Thomas Moore, Building Systems Analyst
Steven Winter Associates