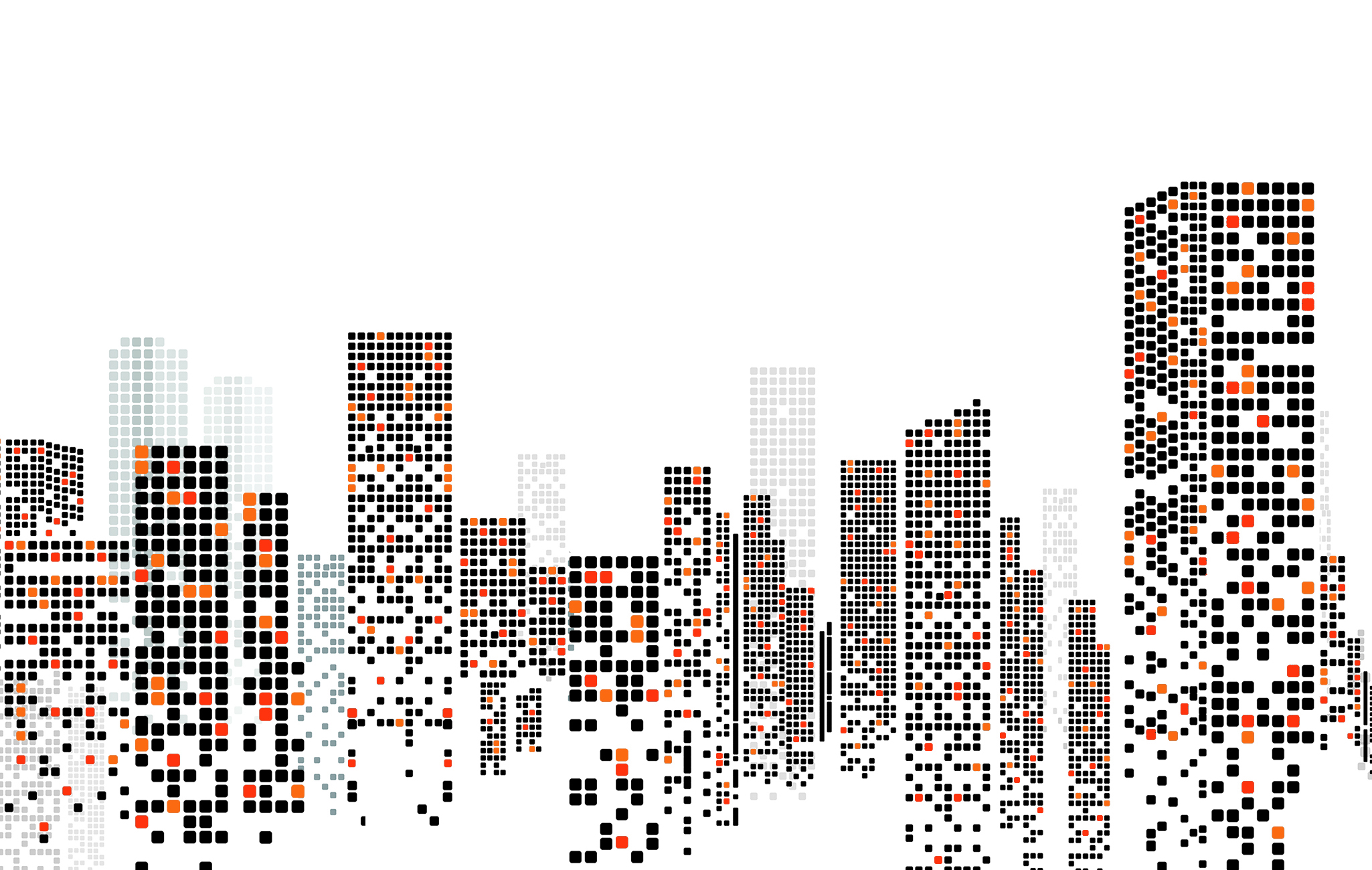
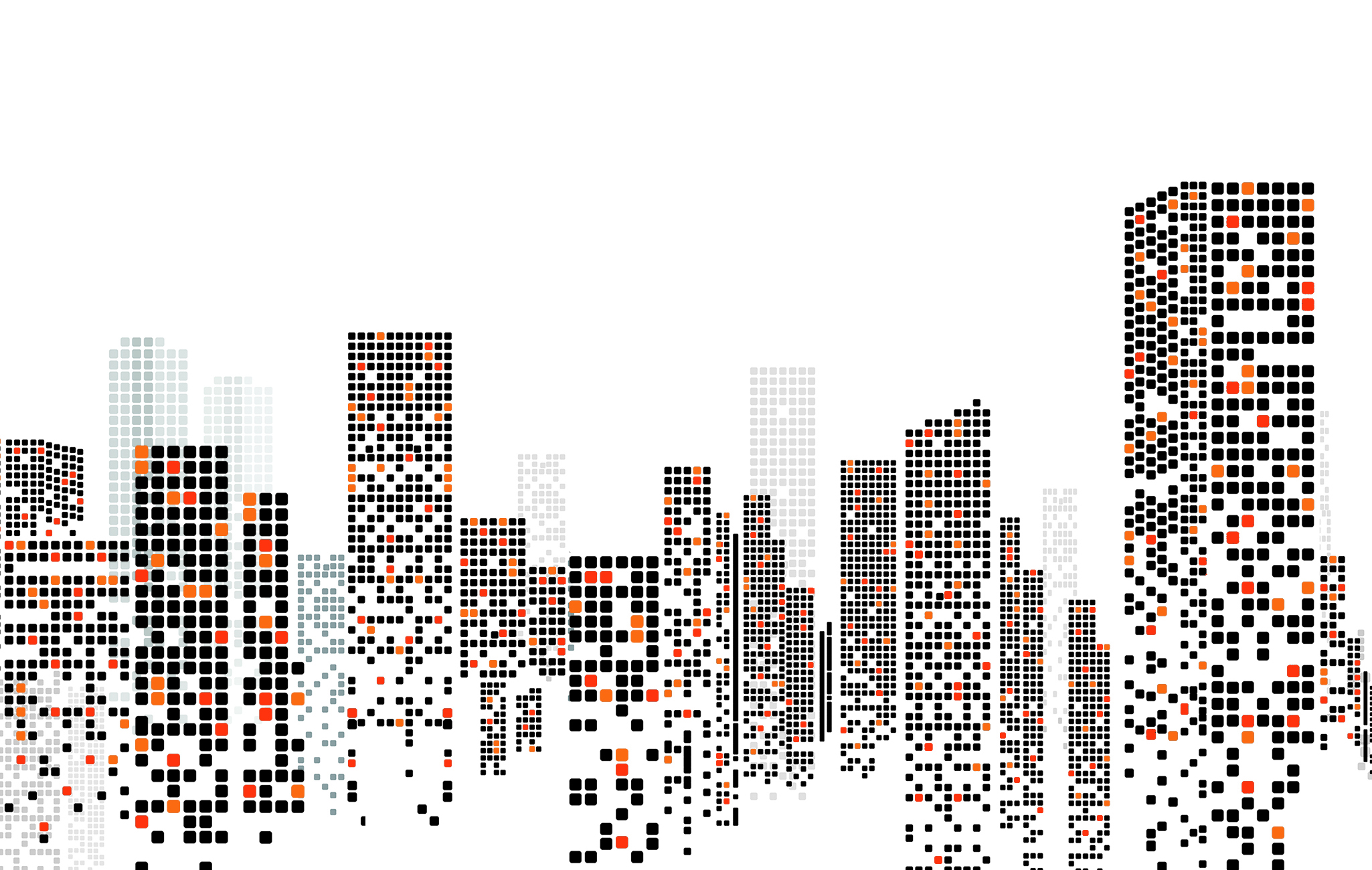
Buildings + Beyond Podcast
Podcast: Play in new window | Download
Charley Stevenson, LFA, LEED AP
Charley Stevenson, Principal, Integrated Eco Strategy (IES), is a sustainability consultant and green building entrepreneur with a particular focus on helping others understand and implement their healthier materials goals. IES is a pioneer in assisting project teams in creating Full Living buildings, specializing in the Living Building Challenge Materials Petal.
Since 2010, Charley’s North Adams, MA, company has managed the green aspects of projects from 1,000 to 500,000 square feet, including the Williams College Environmental Center, Hampshire College’s R.W. Kern Center, Hitchcock Center for the Environment and Yale Divinity School campus. To facilitate materials compliance, IES created Red2Green (R2G), a comprehensive platform for building materials evaluation, selection and management. R2G is available to project teams by subscription and currently in use nationwide.
The advancement of building materials has allowed professionals to achieve new heights when designing and constructing high-performance buildings. But, the topic of building materials is not discussed enough, and more consumers are asking important questions. How do we know where these materials come from? What effects do they have on human health and the environment? How are standards for responsible building materials being enforced? The list continues…
This two-part episode features an interview with Charley Stevenson, a sustainability consultant and green building entrepreneur who has devoted his career to helping others understand and implement healthier materials goals. The discussion begins with a look at the Living Building Challenge, a program that pays particular attention to healthy building materials, and continues with a review of some of the resources that are intended to help consumers learn more about materials and their make-up.
Send your feedback and questions to podcast@swinter.com
Buildings and Beyond is the podcast that explores how we can create a more sustainable built environment by focusing on efficiency, accessibility, and health.
Buildings and Beyond is a production of Steven Winter Associates. We provide energy, green building, and accessibility consulting services to improve the built environment. For more information, visit swinter.com.
Hosts: Robb Aldrich | Kelly Westby
Production Team: Heather Breslin | Alex Mirabile | Dylan Martello
Kelly: (00:06)
Welcome to buildings and beyond.
Robb: (00:09)
the podcast that explores how we can create a more sustainable built environment.
Kelly: (00:13)
by focusing on efficiency, accessibility and health.
Robb: (00:18)
I’m Robb Aldrich.
Kelly: (00:19)
and I’m KellyWestby.
Robb: (00:22)
In this episode I talked with CharleyStevenson from integrated eco strategy about sustainable materials and healthy materials. He’s been looking at this for a decade or more- healthy materials and buildings, and I really learned a lot. This is something that I am finding that I’m more and more interested in. We talked for a long time, quite a long time, so long that we had to edit it down and break this up into a couple episodes, but I’d learned tons. I hope you get something from it too. In this episode, for the first 10 or 15 minutes, we talked about mostly about the living building challenge, which is a program that I’ll let Charleydescribe in more detail, but healthy materials is a big piece of the program. And then we talk about how to find out information about materials, what databases are out there, how to source sustainable materials, what to ask manufacturers, who is keeping track of all this info. And listening back to the episode, actually I realized we threw out a few abbreviations that I thought maybe would be good to define up front. HPD is a health product declaration, ILFI by International Living Future Institute, which is in charge of the living building challenge program, and SDS’s or MSDS’s are safety data sheets or materials safety data sheets. I thought those might be helpful if you are not familiar with those, but here is part one my interview with CharleyStevenson.
Robb: (02:03)
Well first of all, thank you for being here. This is an important topic. Healthy materials, sustainable materials. And I know you are very involved with living building challenge projects. Yes?
Charley: (02:17)
Correct. We started our first living building challenge project in early 2011. And that seems like a long time ago.
Robb: (02:30)
Yeah. Right. And I listened to the green architects lounge podcast and they talked about the living building challenge project or two and they mentioned you and they mentioned that the materials pedal, the materials piece, is the toughest. Do you hear that a lot?
Charley: (02:50)
so I would put it this way, the materials pedal is the biggest surprise among the challenging pedals. So you know, in living building challenge there are seven pedals, three of them are highlighted as particularly challenging energy, water and materials. The energy pedal requires net zero or in some cases net positive energy. And I think there are lots of rules of thumb that have evolved over the, over the years. And project teams can look to a pretty substantial set of case studies and understand, you know, generally things are converging toward heat pumps and triple pane windows and you know, certain levels of, of air infiltration. And in so doing they can pretty reliably get to net zero energy. The water petals is a different kind of a challenge simply because it’s a regulatory challenge and an operations challenge. You know, the requirement that a project produce and treat all of its own water on site, by and large from rainwater, theres a way to do it, if youre outside of a city, with groundwater and and a pretty standard septic system. But in places where there’s municipal water and municipal sewer convincing first a client and then later a regulator that it’s a good idea not to use that system water is an effort. So I think the water pedal will remain a challenge for the reason that you’re replacing, you know, small sections of pipe with technical systems that need to be designed well and then really relying upon rainwater, other precipitation and, and then sort of continuous operation issues. And again, there’s practice there and there are precedents there. That’s a bigger lift in terms of scope than net zero energy is at this point are net positive energy is at this point.
Robb: (05:25)
Yeah, that also makes sense. It seems like a bigger, more non traditional systems and approaches.
Charley: (05:32)
right, at the single family level it can be very straightforward. I mean there are a lot of LPC projects in suburban or rural areas where it looks a lot like a conventional drilled well in a conventional septic system and that meets the intent of the living building challenge, presuming that there’s enough rainfall on site to demonstrate aquifer recharge. The materials petal on the other hand sounds simple in principle- avoid carcinogens and endocrine disruptors and biocumulative toxins when possible. That unpacks to be a task that touches 100% of products or very nearly a hundred percent of products that go into a project.
Robb: (06:22)
Is that it? Is that like the whole requirement of the pedal that you in that one phrase?
Charley: (06:28)
That’s the, that’s the red list portion of the pedal. So the pedal in living building challenge is the sum of one or more imperatives. So the energy pedal is the single imperative- provide 105% of annual energy needs from onsite renewables without combustion. That’s not verbatim, but, but it boils down to that. The materials pedal has a couple of different facets. One of them is the requirement I just mentioned. To avoid so called Red List Chemicals. These are chemicals of concern, about 800 specific chemical abstract service numbers, on the order of 25 chemical families of concern. So that’s one piece. Another piece is net positive waste. I don’t, I’m not, I’m not reciting these in order. That imperative looks at really four phases of the project. It looks at the design phase. Is it designed to minimize waste? It looks at the construction phase. Are our resources brought to the site, repurposed, and salvaged and diverted from either landfill or incineration to the highest extent possible? The third is the operations phase. Asking the question of sort of responsible resource stewardship. You know, that’s onsite recycling, that’s composting, that’s sort of making sure that as the building is used, it’s not contributing to a waste stream. And then finally end of surface, you know, 50,100, 200 years down the road. What care has been given in the design and construction phase to ensure that the, the materials aren’t destined for landfill or incineration down the road. So some of that’s designed for disassembly, some of that is flexible structures so that if a building is set up to be adapted for future use rather than demolished and replaced. So that’s that’s another piece of the materials kettle.
Robb: (09:09)
So I guess the healthy materials piece is the red list, as you mentioned, but then there are the three others.
Charley: (09:18)
And then there’s him embodied carbon.
Robb: (09:21)
Oh, there’s one more. Ah, I was wondering, I was going to ask you about that. I thought you said that was the last one.
Charley: (09:27)
I’ve learned not to, I’ve learned not to number my lists before I start talking cause I’m always wrong when I do that. You know, embodied carbon at this at this point requires project teams to, using tally within revit or using the Athena tools to calculate embodied carbon for the project and its renewable energy system and then purchase a one time carbon offset at the start of the project effectively to pay back the carbon debt so that embodied carbon is covered. And then the operational carbon is covered by the onsite renewable systems so that the project truly is a carbon neutral in construction and operation.
Robb: (10:23)
And that includes extraction and processing and shipping. That piece of the pedal?
Charley: (10:28)
It does Using libraries. So we’re not studying, you know, how many trucks come to a project on a given day or how many hours are put on an excavator that’s all covered in tons of concrete and square feet of drywall and basically don’t get, you know, in the, in the simplest terms, looking at the assemblies and then using industry standards to assign embodied carbon impacts to the, the volumes of each assembly type.
Robb: (11:03)
That makes sense. That makes sense. And I mean, there’s a lot to it. And this is, correct me if I’m wrong, but this is the most rigorous formal program looking at sustainable materials, Yes?
Charley: (11:21)
It’s the most rigorous one I know of. I’m imagining there’s something out there. I mean, the way I see living building challenge, having evolved, it certainly wouldn’t be possible without USGBC and LEED, if we accept that lead is an evolutionary process and it certainly has evolved, you know, continues to evolve. And in each iteration LEED gets more stringent with the idea that it’s moving toward sustainability. Over time, years, decades, it moves to a place of positive impact that no harm is allowed to be caused by a LEED project. So certainly there are LEED projects that are net zero energy for instance, but if there’s no requirement, so then the notion in LBC is to say what’s the logical extension? What would true sustainability or regenerative design look like? It wouldn’t necessarily be that we stopped at a project that’s 30% better than code energy use or 50% better than grid energy use. Let’s take that to the place that looks truly sustainable or it looks future-proof and that would be net zero energy. So effectively in each sector of green building consideration, we follow that evolutionary curve to the point where it looks neutral or positive and that’s the starting place for the living building challenge.
Robb: (13:01)
Makes Sense. Kind of going all the way. And I personally have been involved very only tangentially in a few living building challenge projects. I know others in our office have been much more deeply involved, but it’s ambitious. It really is. And it’s off putting, I think many of the petals can be off putting, the materials one maybe more than the others.
Charley: (13:33)
Yeah, someone described it as a Trojan horse. It seems really straightforward and then you welcome it in and it starts to unpack inside the gates of a project. And you’ve committed to a lot and you might not even, particularly in the early days, you might not have realized quite how much you committed to.
Robb: (13:58)
But and this is what we discussed talking about perhaps, the red list and LBC. I think you used the phrase waiting into LBC, not diving into LBC. There are some less heavy lists lifts that can make a big impact to indoor health, to overall carbon and bodied carbon of projects. And I think that some more accessible pieces might be well more accessible.
Charley: (14:30)
Right? So I think that’s, that’s one thing I’m really looking forward to talking about. Another piece is that the market has evolved a tremendous amount since the advent of LBC. So you know, the way projects work most have an LBC projects in particular, they may have a three year five life cycle. So the stories that current projects are telling are quite different than the stories told by projects Five and 10 years ago. Back in 2011 and 2012 we were a smaller operation and there were two of us and we could hear one another in an open office and it generally took five or 10 minutes on the phone to describe to a manufacturer or you know, an engineer, product engineer at a manufacturing firm. Just what the living building challenge was. So if we were on a research task, we had to plan on stopping and giving background. It is no longer the case, or It’s very seldom I should say the case that we call a manufacturer and have to explain LBC. So just that fact alone means that the, you know, the effort required by a particular project team is, is vastly reduced because there’s familiarity. So that’s one thing I would want to make very clear is that while it remains a challenge, a lot of the war stories from early projects are now somewhat outdated in the sense that it has gotten significantly easier. And another piece of that, is that unlike say the water pedal, where it’s a new regulatory lift for each new project, materials can be fairly consistent from project to project. So once a single project team has determined a good drywall or you know, an appropriate non flat interior latex wall paint, that is a really good starting place, if not a good solution for subsequent project teams. So because information can be shared and because there’s the possibility of reuse of compliance information from project to project, the community of practitioners can facilitate future materials, project compliance paths for all subsequent projects. So there’s that, that idea of data reuse and information sharing is I would say much more significant in the materials petal than it is in others.
Robb: (17:36)
And you manage a database. The red to green database I believe, is your product that you have kind of compiled over the years? Is that true?
Charley: (17:47)
Yes. So I think almost all LBC project teams begin with a spreadsheet. So the international living future institute has a template spreadsheet that’s effectively the reporting form that that needs to be submitted for audit at the end of the project. So everyone begins there, there’s certain information that gets tracked and it’s a subset of all of the information that’s collected over the course of researching a product for LBC compliance. So the quick story of red to green is that we had our first living building challenge project at Williams college and then about two years later signed on to do one at Hampshire college just about 40 miles away. And we thought it would be really easy because we had all these answers from the first project. And Lo and behold, we’d fought, forgotten a lot of what we’d learned because we didn’t write it all down. And then we started our third project, the Hitchcock Center also on the Hampshire College campus. And those two projects had the same construction team and were overlapping in design and construction. There again, we ran into the limitations of a spreadsheet. First of all, it didn’t contain all the information that we’d learned. And then on top of that, there weren’t enough dimensions in the spreadsheet to keep track of what was consistent from project to project and what had changed from project to project. So we started a database development process to take advantage of the many dimensions that a database allows. And over time that’s evolved to be a software platform that’s focused on LBC materials compliance that we call red degree.
Robb: (19:37)
I hear quite a few people mention the red list, but the red list is not a list of products. It’s a list of chemicals that are not allowed in any products that you use in an LBC building, is that accurate?
Charley: (19:50)
That’s correct. So the red list is you could say worst in class chemicals. So you’re familiar with some of them asbestos, led, you know, others by name, BPA or p Foss, even something like BPA isn’t a single chemical that’s a chemical family. So I won’t really know the numbers off the top of my head, but there are dozens of BPAs, there are polycarbonate VPAs and so forth and so on. So we sort of start with the idea that we’re going to avoid BPA and then need to delve much deeper to find specifical chemical compounds revealed by manufacturers, which may or may not be BPA. So there’s a lookup process that we do when, when screening a product.
Robb: (20:48)
Gotcha. Basically all the products in that database do not contain any red list chemicals. It’s that accurate?
Charley: (21:11)
It’s not quite so simple. So we’ve looked at something over 9,000 products and we sort them into categories. There are a couple of different ways of sorting. Sometimes we know all that we need to know about a product to make a determination and other times we don’t. It’s still the case that not all manufacturers will reveal 100% or anything approaching 100% of the chemicals in their products. And there are a couple of reasons for that. Some valid, some arguably less valid. Sometimes they just don’t know. So I’m sitting in a chair which has, you know, I’d guess 150 parts, you know, they’re the arms and they’re the screws that hold on the arms and they’re the little plastic levers that let me adjust the arms. It’s quite possible that each one of those comes from one different sub supplier. And it’s also possible that like a screw that has a black coating might involve two or three suppliers. So just the act of figuring out what’s in a chair sounds straightforward. It’s nontrivial. Yup. And then sometimes it’s just a data acquisition problem and we’re totally sympathetic when manufacturers face that. Other times we’re also sympathetic, but we when there’s a concern about proprietary information. That’s to say a company has invested significant resources in figuring out how best to make whatever, a flexible coating that could go on a, you know, the arm of a chair in this example. And they, they don’t want to reveal how they made that because understandably if they, if they gave the chemical recipe, someone else would have a shortcut to replicate their high-performing chair arm coating. The trick in all of this is that, you know, as a, as a consumer or as a designer, that’s, that’s recommending products to consumers, we want to begin from a place of information that allows us to make informed decisions. So it’s very different to say, you want me to indicate that you, if we switched to food as an example you know, the difference between, trust me, it’s organic and I have a third party seal from the Oregon tilth saying that this fruit bar was produced organically and it contains only fruit as opposed to, you know, preservatives or other synthetic chemicals. So, you know, I think I take materials health to be a two step process initially. First obtaining disclosure, so that information sharing and then second, a screening process to understand it, judge for myself, using sort of established rules of health and potential health impact to understand if a product screens positively or negatively against those lists of chemicals of concern.
Robb: (24:47)
Yeah. Okay. And so where’s the best place for looking for HPDs, which stands for?
Charley: (24:58)
Health product declarations. It is still early days for getting this information and there isn’t a standard standards. So there are multiple standards for ingredient disclosures, all of which are good and maybe none of which are perfect.
Robb: (25:22)
Yeah, no, it’s, it’s very confusing. There’s all kinds of different sustainable product certifications. It’s a little alphabet soup that I, for one don’t know exactly what to make of them.
Charley: (25:35)
Right. and I wouldn’t claim that I know what to do with them either. I think the, you know, the way we approach it and we talk about waiting into this, potentially overwhelming pool just pick a couple of criteria that seem to make sense. So, you know, on the simplest level, is it good to know what’s in a product? Better, that is, than not knowing. So yes. And then it doesn’t need to be a hundred percent disclosure, is it good to know something rather than nothing? Sure. So if you look at a safety data sheet, for instance that does not reveal 100% of material ingredients now, but it will flag certain chemicals that are known bad actors. So that’s to say there are, there are regulatory requirements to reveal certain things. Now, there are other bad actors that aren’t subject to requirements. So if a product contains Formaldehyde, for instance, it will show on the SDS. Gotcha. If it contains BPA, it may or may not show on the SDS. Someone could choose to put it on the SDS, but they’re not required to put it on the SDS. So that’s a good first screen because a product, or many products are required to have them. So anything that’s any chemical constituent, that’s a proven carcinogen, will be revealed through the safety data sheet. If we move on to something like a health product declaration, that’s a voluntary standard, it’s fantastic because it is a standard. So there is an increasing level of consistency from manufacturer to manufacturer. It’s good that it’s an evolving standard. So, you know, the health product declaration collaborative does tremendous work in industry helping manufacturers understand the benefits that accrue from disclosure.
Charley: (28:00)
And then over time, that standard evolves, you know, moving toward higher levels of disclosure, which is to say you know, moving from say a thousand parts per million as the threshold for disclosure to a hundred parts per million as the threshold for disclosure. So there’s fewer places for chemicals of concern to hide as you move toward a more stringent screen for ingredient disclosure. So all of these resources are tremendous. What they do is they bring information out into the light for review and reflection by project teams. So as we reach higher and higher levels of ingredient disclosure, we now that get to the next question, great, I know what’s in this product, should I use it? And that’s an entirely different question because that we presume some knowledge about chemicals of concern in order to move from the factual question to the, the guiding question. Andagain, there are lots of tools. Something like the red list gives us a way to ask the binary question, does this product have a chemical that someone else has said I should avoid? So in the case of Formaldehyde, it’s a carcinogen I understand intuitively that given a choice, I wouldn’t use that in a building.
Robb: (29:59)
Yeah. I ran across something in an article that was a pretty general article or paper that advised avoiding mastic for duct sealing, use tape instead of mastic for duct sealing because mastics contain many chemicals of concern and they were talking about just generally. And so this kind of floored me because mastics are so much better at duck ceiling then tapes usually, that I was a little concerned. So I went through, I looked up a few SDSs from some mastics that I had used that I knew about. And you know the compounds list on the SDSs accounted for something like 17% of the volume or the weight of the product. And then, so I dug a little more, tried to find some duct mastic with product declarations. HBDs and did not find any. So it’s frustrating.
Charley: (31:00)
Right. Well, I mean, you can’t unthink these thoughts. You know, we might change our diet if someone said to us, what do you have for breakfast every day? I can only tell you 17% of what’s in it. And that leads to that question well what’s the other 83%? And if someone were unwilling to tell you, you might go looking for a different breakfast. And it’s possible that the other 83% is a nerd, but wouldn’t you feel more comfortable if you knew that? Absolutely. And it gets to a really good point, robb. That A consideration in design is to avoid single variable optimization. So it is absolutely true that mastic produces, you know, duct leakage with a higher effectiveness rate. Lower duct leakage at a known installed cost. Right. if you asked the question, what’s the most cost effective way to reduce duct leakage? The answer is mastic. If you’ve asked the question, what’s the most effective way to deliver uncontaminated air to building occupants? You’re introducing a new variable in the discussion and that’s uncontaminated. Leakage reduction is great, but If it comes at the expense of a contaminant load it may be less great. And noq you know what the optimal solution focused on leakage alone might be mastic. We may be willing to accept a higher leakage rate in exchange for our production and in chemical load. And now we’re really asking a different question.
Robb: (33:37)
Or somebody can step up and make a mastic without any red list chemicals.
Charley: (33:41)
Exactly. And that’s really, you know, the entire premise of the living building challenge is precisely that- no one stepped up and delivered a red list free. If someone hasn’t delivered a mastic mastic that’s free of red list chemicals, it’s probably because no one has asked them to yet. So what we end up doing as practitioners in this realm is just asking the question, Hey, what’s in your product? I’d really prefer a mastic that contains no red list chemicals and that does a couple of things. First of all, it alerts the manufacturers that there’s an interest, you know, that there’s a market here for a red list free product. It alerts them to something that they can act upon. So it’s not just that I want a healthy product, it’s that I want a product that doesn’t contain anything in these 25 chemical families. Some of them are going to be easy. Yeah, we don’t put asbestos in our mastic. though it might be legal, we don’t put led. But there may be some plasticizers that we’d have to look at and come to a better understanding internally speaking as the mastic manufacturer, to know, do we have it now and can we reformulate without. And to a topic you touched on a little bit ago, there may not be a perfect mastic and then a design team is left with the question, are they better off with a leaky duct or a duct that uses mastic to achieve a certain level of sealing and that decision left to the design team. So I don’t think in terms of absolutes, but rather think in terms of the best that we can do for a particular design problem. So when we’ve finished an LBC project, as much as we’d love to say it’s red list free, really what we’re saying is that use of red list compounds has been minimized. So we’re using them in known places for known purposes. So an example of that is a fire alarm. We have not found a red list free fire alarm annunciator, but we believe there’s very good reason to have fire alarms in buildings, and code officials agree. So what we’ll do in that case is we’ll advocate to the manufacturer and say, you know, we have this red box. You didn’t tell us what the, what the coding was on that box. And we can deduce that it contains led. That’s fine. We accept that this is the state of the market for now. And to have a safe building, we want a fire alarm system, and to have a fire alarm system, we accept these shortcomings and current disclosure and compliance. Please know that when you or one of your peers has a product that does better than this from a chemical perspective, we’ll shift our purchasing there. So we’re engaged with the market as it exists, but we’re telegraphing what we want the market to be in the future, in an effort to tip the market toward optimization. And the idea there really is the living, building challenge teams individually may or may not have a lot of power, but collectively they define the terms red list, red list free. And they commit in the abstract toward buying better products in the future. So whoever’s making the case for better paints or better coatings or better what have you, can be accumulating this information to say, boy we’d own market share, if only we had a red list free solution in this particular building product sector.
Robb: (38:03)
It makes sense. And we’ve seen the market change in this way and in other and other aspects. Our accessibility group I know has had issues with high tech windows and doors, not having the proper clearance to get into in and out of buildings and working with manufacturers to get products that satisfy everybody. And if there’s big enough demand, it’s worth their while.
Charley: (38:36)
Right. Absolutely. We internally track what we call success stories, which are these breakthroughs with manufacturers. And you know, many go to great lengths and we appreciate, you know, their their knowledge of their products, their knowledge of the manufacturing process, and they alone can pinpoint the shortcomings and then work within their supply chain and work to innovate in ways that addresses these concerns. And it moves either in large steps or incrementally toward better products. Where in this case better is holding the line on all of the other performance criteria, durability, what have you, and increasing awareness of health impacts and really making efforts to reduce those.
Robb: (39:34)
Yeah. If anybody knows of a good mastic with HPD, let me know. I’d be very keen to find one.
Charley: (39:42)
So that’s effectively what we do, is we’re just cataloging what we find. So when I go back to those 9,000 products, you know, some, we have full disclosure, some we don’t, you know, in every case if we’re trying to ratchet toward fuller disclosure and then certain products are red list free, certain products or Red List compliant, certain products or red list unknown and certain products are red list noncompliant. So that gradation, red list free I think is obvious. Red List compliant, you know, there are what ILFI calls temporary exceptions. So exterior sheathing, so plywood sheathing, It needs to be weatherproof for a few months and no one has yet come up with a resin that let’s you know, cdx plywood, weather for a few months without delaminating, without using fetal formaldehyde. So if we want buildings to be durable, they have to stand up through the construction process and they need to tolerate a certain amount of moisture.
Charley: (41:03)
So the chemistry, the green chemistry isn’t there to give us exterior grade plywoods without fenal formaldehyde. So we’d love one, but for right now, ILFI has given us permission to use that chemical of concern in this limited application until the market has transformed.
Robb: (41:24)
All right. So that’s an explicit quote exception for now. That’s something that design teams have to judge, right? But ILFI themselves have given stated permission.
Charley: (41:37)
So there’s dozens of exceptions that reflect temporary market limitations. So part of what we’re doing is we’re attaching that exception to a particular product so that the next project team that comes along can see it’s okay to use this. There’s nothing better than this product in this particular market segment for the time being. And then, you know, further down the list of the products about which we’ve not gotten enough information to make a judgment, there’s something that’s called the due diligence case. So if we reach out within the bounds of a particular project to three manufacturers, none of whom will answer our questions, and we know of nothing else that can be used to meet the project’s requirements, we can go ahead and use one of those products of uncertain compliance, because the work can’t stop either in design or construction to wait for the market to transform. And that’s equally true for noncompliant products. So, you know, back to the fire alarm, they contain lead. We wish they didn’t contain lead. But we, we need them. So, you know, as we look at the library, it’s about a third products that are compliant. A third products that are unknown, and a third products that are noncompliant. And where it gets interesting is when you have a particular design need or performance need that can be met either by a compliant product or a noncompliant product. Now you really feel yourself pushing the market or moving the market to say, no, we’re not going to buy this thing that is noncompliant. We’re going to favor this thing that’s compliant. And I think back to your mastic example, you know, this is where, you know, it, it’s an interesting process for designers to ask what products are necessary in a building. Is that the case that mastics are necessary? Maybe, or there may be a creative solution that says we can achieve an adequate level of duct sealing without mastic. And now we’re asking the question, well, what would replace mastic to achieve the desired performance level? So a lot of what we end up doing is, we feel most impactful at the beginning of design where we’re able to broaden the question, you know, to steer away from say, spray foam solutions into bat or loosefill solutions. Because you know, these are places where you can make a huge step away from chemicals of concern. You can also make a huge step away from embodied carbon. And now, we’re focusing on the performance and the abstract rather than the particular performance characteristics of a material. So it may be those are different air barrier solution. It may be that there’s a whole different wall assembly. But with openness in the early days you can often move toward products that meet multiple at the optimized and multiple criteria.
Robb: (45:21)
That’ll do it for part one of my interview with Charley. Next time we’ll talk about where to start with healthy products or sustainable products. If you’re not going to go whole hog with living building challenge, where does it make sense to start spending effort to look at healthy materials and buildings? I also wanted to mention Charley’s website materiallybetter.com there’s links to that on our show notes, but I wanted to give you a shout out for that website too. Thanks and I hope you tune in next week.
Speaker 4: (45:54)
Thank you for listening to buildings and beyond. For more information about the topics discussed today, visit www.swinter.com/podcast and check out the episode show notes buildings and beyond is brought to you by Steven Winter Associates. We provide energy, green building and accessibility consulting services to improve the built environment. Our professionals have led the way since 1972 and the development of best practices to achieve high performance buildings. Our production team for today’s episode includes Dylan Martello, Alex [inaudible], and myself. Heather Breslin, thank you for listening and we’ll see you next week.