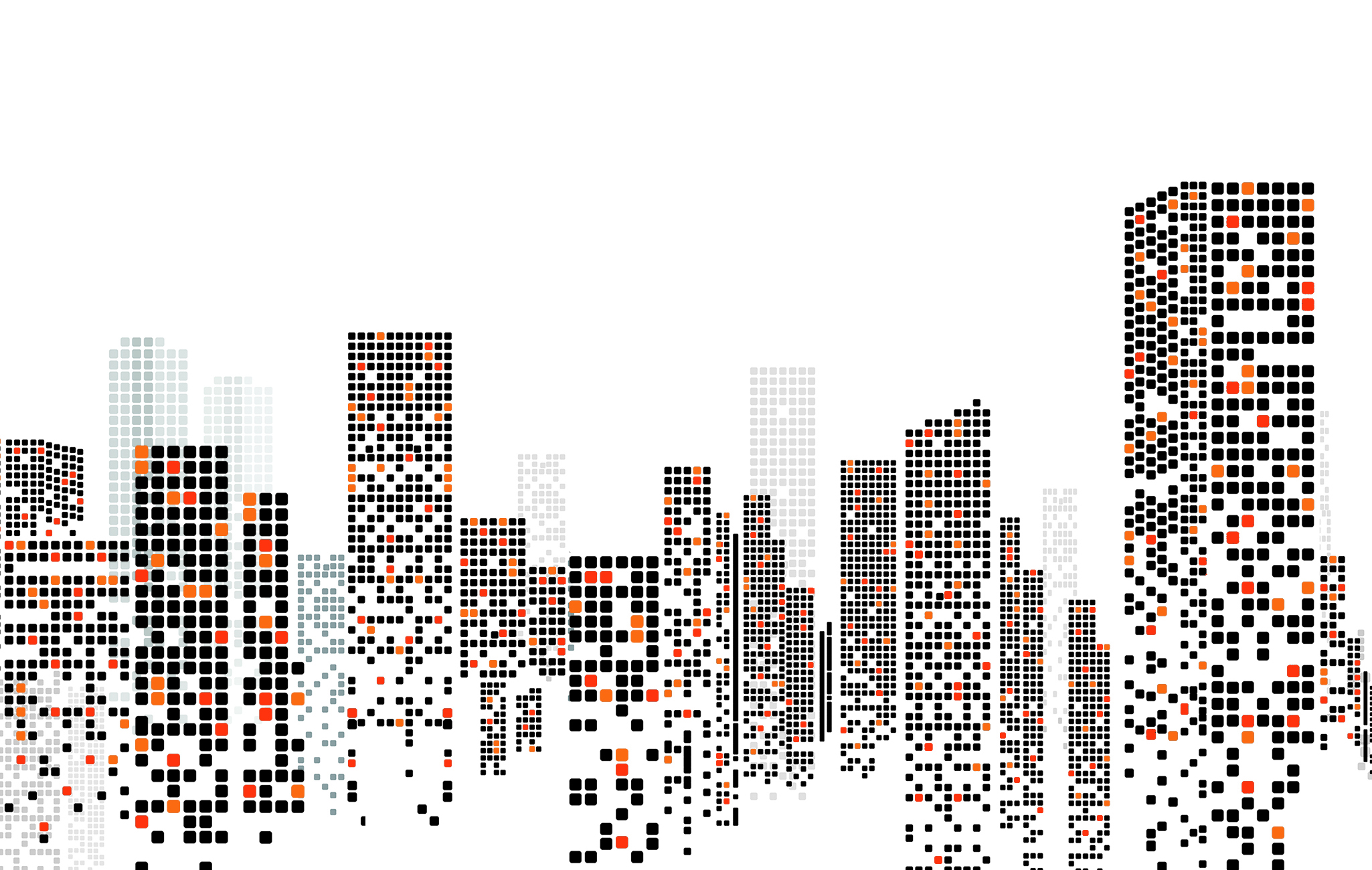
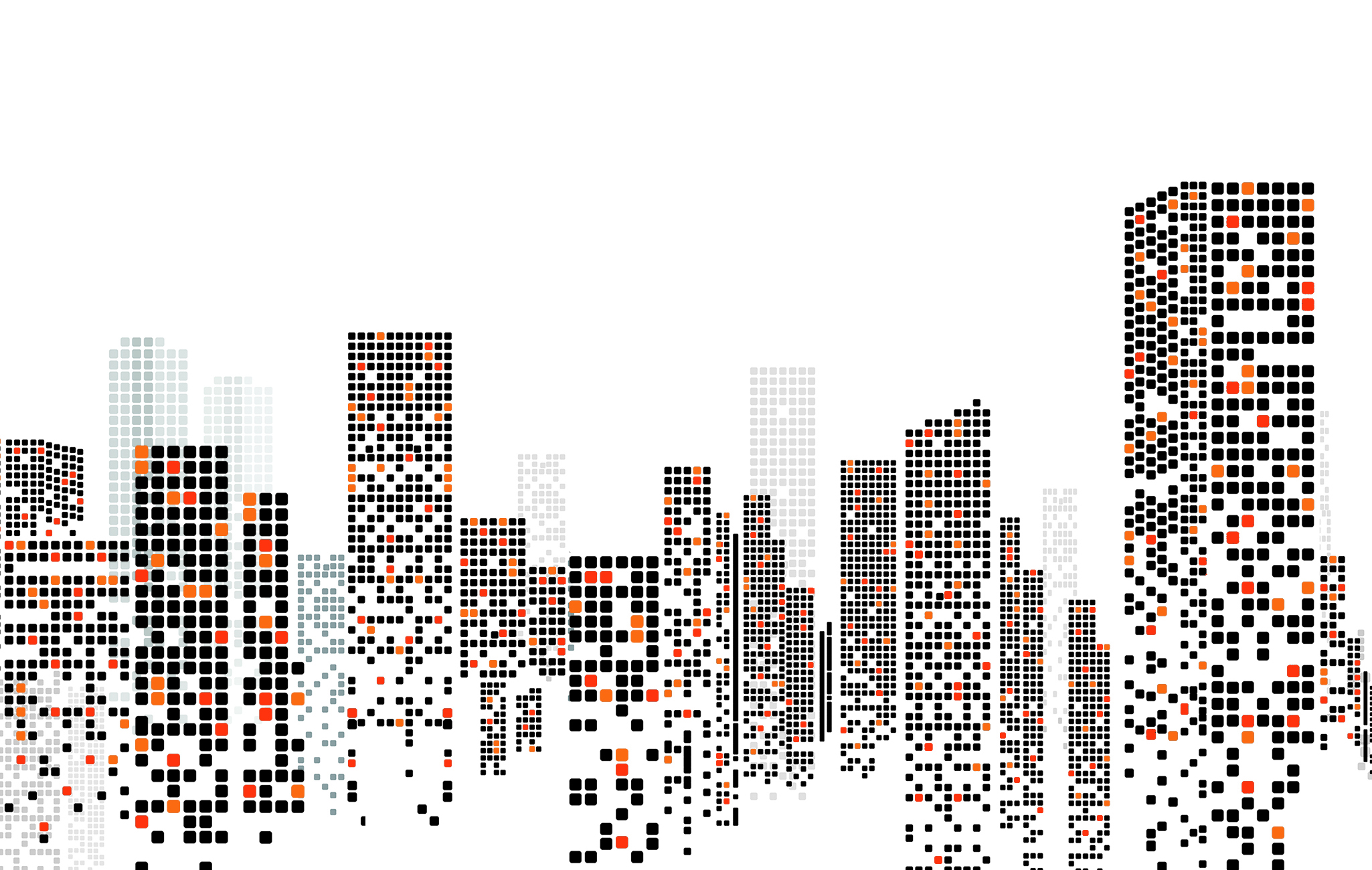
Buildings + Beyond Podcast
Podcast: Play in new window | Download
Steve Klocke, RA
Steve Klocke is a Senior Sustainability Consultant at Steven Winter Associates and a registered architect with 18+ years of experience in architectural design and building science consulting in residential buildings. He provides comprehensive green building certification support for the LEED for Homes, ENERGY STAR and Indoor airPLUS programs with a focus on lowrise multi-unit new construction and gut rehabs.
Steve is an integral part of the initial strategic planning sessions and workshops with builders, architects, and homeowners, setting goals and scopes of work for projects. The certification support he provides for project teams includes energy and building systems analysis, architectural design support, and project management. As a HERS Rater and LEED for Homes Green Rater, Steve inspects projects under construction for compliance with energy performance, durability, and health and safety standards. His performance testing expertise includes whole-house infiltration and duct leakage, as well as infrared thermal imaging.
The residential building industry has made incredible progress toward sustainability and energy efficiency goals. At the same time, Senior Sustainability Consultant and Registered Architect Steve Klocke finds many new buildings under-performing because designers continue to make simple, avoidable mistakes.
Based on lessons he’s learned from certifying over 1,200 dwelling units over the past seven years, Steve discusses the top ten multifamily design mistakes being made over and over again – and how to avoid them. On this episode, Steve uncovers mistakes 6-10. Be sure to check out Part 1 of this episode if you haven’t already!
Presentation slides (mostly graphics): Top 10 Multifamily Design Mistakes
Steve’s Top 10 Multifamily Design Mistakes:
Other Resources:
What comes to Robb’s mind when Steve mentions illicit, high-flow shower heads…
Send your feedback and questions to podcast@swinter.com
Buildings and Beyond is the podcast that explores how we can create a more sustainable built environment by focusing on efficiency, accessibility, and health.
Buildings and Beyond is a production of Steven Winter Associates. We provide energy, green building, and accessibility consulting services to improve the built environment. For more information, visit swinter.com.
Hosts: Robb Aldrich | Kelly Westby
Production Team: Heather Breslin | Alex Mirabile | Dylan Martello
Kelly : (00:06)
Welcome to buildings and beyond
Robb: (00:08)
The podcast that explores how we can create a more sustainable built environment
Kelly : (00:13)
By focusing on efficiency, accessibility and health.
Robb: (00:18)
I’m Rob Aldrich
Kelly : (00:19)
And I’m Kelly Westby.
Robb: (00:22)
This week is part two in my conversation with Steve Klocke, architect and rater here at Steven Winter Associates. We were talking about his top 10 frustrations, top 10 multifamily design mistakes. And this week we talk about the second five on his list. We start by talking about lighting controls, which was probably the one that I found most surprising.
Steve: (00:48)
Here’s the deal.
Robb: (00:49)
All right. I was surprised to see this on your list. I was.
Steve: (00:52)
Really? Because this is so often done poorly.
Robb: (00:56)
And again, we’re talking about multifamily buildings. When there are just lights that are on always is that the issue?
Steve: (01:02)
as far as I can tell, the only reasons to have lights on all the time is if you’re growing pot, which is certainly legal for some of you. Or in areas of, you know, Egress, et cetera. The trick is, in areas of egress. So there’s a lot of different parts of the code and lot of different codes that apply to lighting. So here’s the jist. 10 foot candle is the norm for supplying illumination to a space. Let’s focus on Egress, I guess, cause that’s areas that usually get screwed up. But when it’s not, when an ingress area is not in use, you can go down to as low as one foot candle and that a big jump in consumption of energy. So, you know, there’s parts of the energy code that says you have to have occupancy sensors in these, you know, dozen spaces. It doesn’t say you can’t have occupancy sensors in these other spaces, right? And so it’s a misinterpretation of the problem.
Robb: (02:11)
So really, it’s not that people are lazy and don’t care about energy. But sometimes they think the code forbids?
Steve: (02:20)
That’s my impression. Yeah. You know, and the rooms like electrical rooms, for safety reasons, et cetera. I’m not gonna argue with that. But you know, a lot of times you’re going to have these stairs where in some buildings we have, you know, for security reasons they don’t want people to use the stairs. And so they actually kind of make it harder to use the stairs. And yet they’ve got the lights on 24/7 full blast in there and just kills me. And so really what you need to do is put in controls. It’s all about controls. You know this from an engineering standpoint, Rob, it’s all about controls. And now, occupancy sensor, vacancy sensor, what’s the difference? An occupancy sensor will turn on when someone enters the room and it’ll turn off after a certain period afterwards once it stops sensing that person in there. A vacancy sensor, you typically will turn on yourself and then it’ll turn itself off. And there are some spaces where one is appropriate and some of the places where the other is appropriate.
Robb: (03:21)
And that’s not a timer? You turn it on, and then there is an occupancy sensor that senses you leave
Steve: (03:27)
In this room we’re sitting in right now, It is an occupancy sensor, and it doesn’t matter if the sun is shining bright through the windows, this light comes on, which drives me nuts. And it will eventually shut off, but you know, think of all the startup, you know, wear and tear on the lights, and the consumption, et cetera. And so, you know, an occupancy sensor makes sense in your egress areas where, look, if it’s an emergency, you don’t want someone have to flip the switch and turn the lights on and you know a hundred people plowing over you because you’re the first one through the door.
Robb: (03:59)
I see. So, a vacancy sensor, in this office in which we’re recording, for instance, if someone walked into this office just to empty the trash, or just came in to get some more coffee. You have to turn on the light.
Steve: (04:23)
Yes.
Robb: (04:23)
In a lot of the offices, there’s plenty of natural light. So this would be a great place for a vacancy sensor.
Steve: (04:35)
Agreed, but not in in egress area.
Robb: (04:35)
In multifamily buildings, what places are good for vacancy sensors?
Steve: (04:50)
So offices, closets, exercise rooms, mail rooms, trash rooms. As far as I’m concerned. I suppose you could do an occupancy sensor in there because most of them are internal and don’t have any windows. But you know, in your egress areas, your corridors and all of those places, you definitely want an occupancy sensor for safety. And we’ll never try to pick a fight with a code official. I mean, we know where we stand, but there are nuances that are being missed
Robb: (05:21)
And they’re getting better and cheaper, is that right?
Steve: (05:25)
Yeah, and I guess you have to balance the short term versus long term cost implications. Look, if you’re selling this building and you’re not paying for the utilities or whatever, you’re going to put in whatever’s cheapest. If you’re maintaining the building, keeping it, you know you are going to want something that’s going to minimize your operating costs and so there’s that issue too,
Robb: (05:42)
These are things that don’t come into the ratings a lot of the times.
Steve: (05:44)
They’re required under some certifications and basically what it comes down to is an argument. With me, they’re like, “hey, you can’t do this.” and I’m like, “well no, you can, you just need to try a little harder.” You try to say that without hurting anybody’s feelings or sounding like a jerk, which is not always achieved by yours truly.
Robb: (06:07)
Moving on, I’m going to let you talk about this one: oversized HPAC.
Steve: (06:16)
I’m glad that as the engineer in the room, Robb differs to the architect in the room to talk about oversized HPAC. I think it’s going to be a testament to how well I’ve been trained by the engineers here at Steven winter associates. So the keyword here is short cycling and it doesn’t mean a whole lot of people on bicycles that are short of stature. That’s the slide in my presentation, is my bicycling team from rag rye in Iowa. Anyway, short cycling means that your equipment is typically of a single speed. It turns on hard, runs hard, shuts off, and it does that in rapid succession. And so what you get is, the analogy I use, is a car or like, let’s say you’re in a taxi or something like that, if you’re in a crown Vic with a v8 engine, you get in there, the driver pounds on the gas until he hits a red light and then pounds on the brakes. So not only is he wearing out the vehicle faster, he’s consuming way more gas than should he’s, making you sick in the back seat, et cetera. So if you apply it to HVAC, you know, humidification, or dehumidification I should say, is the hot topic now as we keep getting these warm, wet summers that seem to be warmer and wetter than the past. I’m not going to digress into any sort of questionable theories, don’t want to make any enemies here, but good thing our house is on a hill here in Norwalk. Anyway, so you’re not pulling that latent heat- that ones for your benefit Robb. Which means “moisture” to the rest of the architects out there.
Robb: (07:41)
Thanks for clarifying, cause I wasn’t going to, I was like, yeah, of course, you’re right. That’s I think one of the biggest, probably the biggest issue with oversizing- is not dehumidifying in a warm or humid climate you really don’t get the dehumidification.
Steve: (08:33)
Yeah so you’re not achieving the efficiency that your equipment is rated to cause of short cycling, you’re wearing it out, you’re not getting dehumidification on the cooling side and it’s just uncomfortable. You know, like who wants a cold hard blast of air on their necks every 10 minutes, right? You’d rather have sort of a more even, smooth operation, ramp up a little bit, ramp down a little bit, smooth operator is what we aim for.
Robb: (08:56)
It’s interesting. So you can make an argument that some fuel fired heating systems, there’s not a big efficiency to oversizing.
Steve: (09:13)
Sure, especially those that ramp down. Like, you know, boilers for example, can go at a 10th of their…what’s that term Mr. engineer? Modulating but uh, turn down?
Robb: (09:25)
Turn down. Sure.
Steve: (09:26)
Yeah. That’s the term I’m looking for.
Robb: (09:27)
Yeah. If you could modulate down 90%, turn it down 90% that’s pretty good. But I think it’s a comfort issue. It’s a humidity issue and it’s a cost issue. Especially with air conditioning, I mean you put in twice the capacity you need, you pay almost twice as much
Steve: (09:46)
Yeah but Robb what if you’re going to add on some day? You really want that extra capacity man.
Robb: (09:53)
We’re talking about multifamily buildings, who’s going to add on Steve?
Steve: (09:58)
Anyway, next one.
Robb: (10:04)
Next one, and actually, I’ve been dealing with this tons lately on the oversize HVAC with heat pumps, which are really taking over in a lot of things.
Steve: (10:19)
Everybody thinks that “oh, the heat pump is no problem.” Is totally up and down, up and down
Robb: (10:24)
It has some really big efficiency and comfort potential drawbacks when you oversize.
Steve: (10:30)
Oh yeah. Well I was in a townhome in Brooklyn, in Park Slope actually, with millions of dollars of art on the walls and it’s getting ruined because they got these great VRS systems, but they’re just too darn big
Robb: (10:43)
Yeah. No good. We need to do another episode on humidity. Too much. Too much. All right. Moving on for real this time. Antiquated ventilation.
Steve: (10:56)
Yeah, so I start this one off in my presentation with the old school way of dumping a bunch of air into your corridors, undercutting your apartment entry doors and expecting the air to get into the apartments. Not only is it not allowed by mechanical code, it’s not allowed by fire code.
Robb: (11:16)
With an exhaust fan? So we’re talking about an exhaust fan..
Steve: (11:20)
You have exhaust out of your apartment and make up air. Make up air is, I realized, that it’s important in some areas in this area, it’s not applicable. Make up air is coming from the wrong place. You don’t want to be pumping air into the middle of the building and expecting it to get to where it needs to be. You need to control the air. So by antiquated ventilation, we’re basically meaning we’ve got to take it up a couple of notches. And let’s turn the equation backwards. What if we have central exhaust and then we’ve got a trickle vent scenario, there are some things like that. You know, and we unfortunately were pretty guilty of this. We’ve said for a while based on program clarification, that trickled vents are required and I’ve done a few studies, I’m fairly sure you can tell me better, that show that they really don’t work all that well cause you get all kinds of stratification and tall buildings and stack effect and all kinds of funny things are happening. When you take control away from your ventilation system, it needs to be controlled.
Robb: (12:19)
In both the exhaust and supply.
Steve: (12:22)
Exactly. Both sides.
Robb: (12:23)
Okay. You can’t do one and hope the other side works itself out. And for a century that’s been the standard, where you just suck air from the kitchens, you have a big mushroom fan on the roof, a big stack sucks air from bathrooms and kitchens and there you go. You’re all done.
Steve: (12:45)
Well I still get asked why we have to have exhausted in kitchens.
Speaker 2: (12:50)
Kelly’s doing a separate episode on that one.
Steve: (12:53)
Okay we’re just not going to dwell on that one.
Robb: (12:56)
Its a hot topic. Because passive house and IQ people are butting heads over it.
Steve: (13:02)
Yeah, I stay out of that.
Robb: (13:05)
So what would you like to see? Are we talking balanced ventilation. Are we talking HRVs, what’s good?
Steve: (13:12)
Well, it’s a matter of what you can stomach.
Robb: (13:14)
We talking money?
Steve: (13:15)
Yeah, basically. Yeah. I mean, the extreme end of the spectrum is balanced ventilation through an ERV/HRV. I feel like that’s the direction that you know, code is going to go eventually as soon the people who have been fighting it thus far run out of gas. And Robb says, no by reading his body language. I just don’t see how with more and more studies that come out about the value of indoor air quality, I just don’t see how we can keep not doing that.
Robb: (13:56)
I don’t disagree. And once again, this is a whole other topic, but so many of the balanced ventilation systems, I see ERVs and HRVs, they may not be installed properly, and that’s a big deal. They may not work from day one and if they do work on day one, they’re maintained so poorly or not at all, that they don’t work even like six, nine months after occupancy. So that’s a big deal. And that I think is one of the more valid arguments against mandating ERVs and HRVs. But you can’t argue with the performance benefits with the health benefits, with the indoor air quality benefits.
Steve: (14:37)
Well, in our house, we renovated LEED Platinum, exhaust only ventilation strategy, meets Ashrae, all the boxes are checked. And then after living in it a year, we were like, no, it’s too stuffy. I feel like I’m physically affected because I don’t have enough fresh air. And so we put the ERV in and it literally was a night and day difference. And so here’s the deal. Do they cost more to install? Yes. Do they cost more to operate? Yes.
Robb: (15:10)
Well the energy savings can certainly make up for it
Steve: (15:15)
Right. Well, in our house at least, we had turned up the flow rate above the exhaust only, what we had for exhaust only. So in our case, that was the case that it costs more to operate and there’s more air to heat and cool basically. And it took up space in the attic, Yada, Yada, Yada. But you know what? I mean when it’s your family and you don’t think you’re as healthy as you should be, I mean, it’s a no brainer. Now as a designer, it’s different, you know, but in my presentation, I say, look, try to think if it was your kid, your family, and if you’re living in these apartments.. I know what the constraints are, but you know, it’s something to consider. I tug at the heartstrings.
Robb: (16:03)
There’s no argument about the benefits. It’ll be interesting to see what happens. And there’s better ways to do it. Maybe there are better products coming.
Steve: (16:14)
Yeah. We’re slow to it here in the U.S. I mean, I guess,
Robb: (16:18)
And in Canada it’s very common. And in a multifamily building with good property managers, with good owners, good maintenance, they can be maintained very well.
Steve: (16:31)
I mean do you buy a car and not change the oil every, you know, 5,000 miles or whatever?
Robb: (16:36)
Most people don’t but on the ERV’s and HRVs, most people do.
Steve: (16:43)
This is the luxury I have of it just being an hour presentation. Say what you’re doing wrong and not worry about the bigger consequences.
Robb: (16:51)
Alright enough about ventilation.
Steve: (16:56)
I know you want to dwell on that, but maybe that’s a whole other podcast
Robb: (16:58)
We could go on and on and on. But we won’t, okay. Domestic hot water.
Steve: (17:04)
Domestic hot water. So I had always wondered before I got into this, how the hotel hot water works. How is it that it’s a big hotel and I can turn on the faucet and I get hot water right away? Scolding hot water. And I wonder how does that work? And now I know, right? There’s hot water coursing through the building 24/7. And so you can’t get around that. I mean, people are going to want their hot water and not have to wait for it. So at this point, the best you can do is make that system as efficient as you can. And that means, this is the most technical part of the presentation, there’s a diagram showing a three pipe domestic hot water re-circulation system and a box design. And basically all it is, is taking the hot water return and shortening those runs instead of taking them back down the risers that they came up. So, in a multifamily building, you’re going to hopefully have your hot water generation on the roof, it’s coming down a shaft in the middle of the building and then getting distributed horizontally and then back up again into the various apartments and it goes back down again over again and then up again. Right? So instead of taking the return water back down to the building, you just take it across the top of the building. You take a shortcut back to where it came from in the first place. And so basically if you can reduce your pipe length, if you can also reduce your pipe diameter, so surface area, right? And if you can insulate them. Well back to pipe diameter, I mean in New York City at least, we have to have low flow fixtures, in any of our green programs, you have to have low flow fixtures, and engineers are still designing their pipes to the higher medium on that ASHRAE chart. Right. And so they should be going no more than the low because unless everybody in the building yanked their shower head on the first day they move in and puts in, you know, nine gallon permit or whatever, you don’t need those big pipes. So bigger pipes, bigger loss. Yeah. So longer pipes, more loss, and insulation, just making sure you’ve got your details in there, keep those things insulated.
Robb: (19:34)
I will put the link to one of your PowerPoints up on the site. And others here have done some work on this because it’s much easier to get a handle on this when you’re looking at diagrams in my opinion
Steve: (19:46)
Yeah. It’s a very visual thing.
Robb: (19:48)
Yeah. But, but you’re right. I mean it’s the oversizing thing again, it’s overkill, you know? It’s a CYA.
Steve: (19:54)
Yeah. Not throwing engineers under the bus, but you are a conservative lot. I’m just going to say it.
Robb: (20:03)
And good thing. It’s not inappropriate. That’s not a bad thing
Steve: (20:11)
Sometimes.
Robb: (20:13)
Alright. And how about controls for DHW distribution?
Steve: (20:16)
I didn’t get into that. You are welcome to. Robb, tell me about controls.
Robb: (20:16)
So like you said, in hotels, there’s this big loop that’s pumped 24/7. And in hotels and in larger multifamily buildings, that’s pretty much necessary to pump 24/7. In smaller multifamily buildings, I think there’s potential for demand control. So super simply, there’s like a flow switch that senses if anybody is calling for hot water and whenever anybody’s calling for hot water, then a pretty large pump comes on, primes the system very quickly. So people wait, you know, very short amount of time. But then when nobody’s calling for hot water, it shuts off. And you’re not recirculating hot water throughout the building.
Steve: (21:08)
Midnight to 4:00 AM
Robb: (21:11)
You don’t want to discriminate against people on the second shift.
Steve: (21:14)
No, I’m just saying though that you know, instead of running full blast all night. I mean like you said, there’s savings to be had there. Yeah, for sure.
Robb: (21:22)
All right, we’ll move on. Last but not least, poor communication.
Steve: (21:29)
Yeah, so is that a design mistake? And so here’s what I say: yes it is. Because what is your job as an architect or an engineer? What is your product? I should say. Your product is not the building. Your product is not the MEP systems. Your product is the design, is the drawings and specs. That’s your deliverable. And so if you cannot convey what you’re trying to achieve through those drawings and specs, you’re not living up to, you know, your role as designer. And so it’s making sure that you’re getting everything that you need to on paper, but you’re also getting the feedback you need. So architects, are you listening to your engineers or are you just throwing background drawings at them and expecting them to make it work with whatever? You know architects, they got their hands full with all kinds of other things. Right? And so, it’s just one more input to this whole big machine that technically they’re responsible for. But the best projects I’ve seen is where the architects and engineers have a real partnership and they communicate back and forth. And you know, an engineer will tell an architect, “well, why are you drawing it like that? Why don’t you, if you could just do this, this and this, our systems would be that much smaller.” And you know, so it’s got to be a two-way street as far as communication
Robb: (23:02)
And there are more and more people involved like through the raider to the passive house consultant to the sustainability consultant. I mean, if your feedback gets incorporated.
Steve: (23:11)
this might be slightly biased, but yes, one big important point is listen to your consultants and actually have that two way dialogue. We’re not here to just tell you how much your design is not right. We want the building to be better. We’ve been improving the built environment since 1972 fairly sure. Six years before I was born. I was thinking about it. But anyway, it’s also construction, I mean, I was up in an attic out in long island on a Tuesday this week and we’re up there and I’m like, I’m sorry guys, you just got sort of backed into a corner here. Like, I couldn’t have done this any better than you did, but it’s still not where it needs to be because of the limitations that were placed on you by the design. And so, you know, the good architects will get out there and they’ll get their boots dirty and they’ll talk to the people who are actually building their buildings and they’ll learn from it.
Robb: (24:12)
Oh, absolutely. Yeah. I mean, you learn so much being on the field and seeing the screw ups more than anything else.
Steve: (24:22)
Learning from mistakes. Yeah. Well and not even necessarily mistakes, but maybe just things that could have been done better. If you can get out there and communicate with the guys and Gals who are actually making it happen, they have a lot they could teach you. And I learn every time I go out, I learned something from just some random plumber, like, oh, I’m going to put that in my toolbox and contribute that in the future because I would’ve never known.
Robb: (24:52)
And it goes both ways. I’ve explained to various trades, the importance of an air barrier, what we’re trying to accomplish. And it’s not necessarily straightforward.
Steve: (25:06)
No. And I get a lot of good suggestions there. They’re like “what if we did it like this?” And I’m like, “yeah, you could do it like that,” you know? Yeah. So just as designers, I don’t know if the siloing is the right term, but don’t put yourself in a place where you’re not willing to take feedback, basically. So communication is making sure what you’re putting out there is good in the first place. And then, you know, being willing to hear feedback on it and the other thing, and it actually feathers back into number two, which is designer regularities. You know, engineers are really good at having a pile of stock details that they’ll apply depending on what kind of system they’re working with. Architects not so much. Some are. I don’t think, at least personally. I don’t feel, I mean, and it’s not like if here’s dealing a window detail from scratch every time you’re, you’re doing exactly. If you redrawing the same detail two or three times, it’s a bad detail from the beginning. So what you do is, you learn from good designs, you put them in your own little virtual toolbox, right? You say, for wood construction, this is how we do it. For steel construction, this is how we do it. You’ve got those stock details, use Them. Instead of wasting your time trying to redesign the wheel a little bit every time, build yourself a good stable of details, and then either a. charge your clients less. There you go. There’s one thing. Make the project affordable overall, b. spend your extra time on making the building better in other ways or c. just go golfing, spend some time with your kids, be happy. whatever. Right? Like why are we spending our time with these cutesy, wootsy little details. You know, I’ve got a builder in New Jersey, who does affordable senior living developments. And in an 80 unit building, there are three unique designs, three. Guess what? He can’t build these things fast enough. People love them. They’re relatively efficient. And so it’s like, are they winning any design awards? Not necessarily. But is he providing affordable, healthy, efficient places for elderly people who need that sort of thing? Yeah. I mean, it’s nice to have a design trophy on your shelf, but gosh, I don’t know. I would sleep pretty good if I was saying that I was providing that, you know?
Robb: (27:51)
Right on. That’s 10. We did pretty good. Less than an hour. Yeah. Anything, any other concluding comments? Anything to wrap up?
Steve: (28:04)
Yeah so basically, at the beginning of the presentation, here’s where it starts. Designed decisions made in the office have a snowball effect throughout both the design process, the construction process and the life of the building. Right? And the earlier you can make good decisions, the better off your building’s going to be in perpetuity. And so someone asked me, as I was asking around the office, you know, like for suggestions on design mistakes, and what I should incorporate in this thing, and he said, “well, have you thought about why people keep making these bad design mistakes?” And you know, that’s a good question. It’s very meta or whatever you want to say. But I thought about it and it’s like, you know, design is just decisions. It is decision after decision after decision after decision, its endless. I mean, that’s really all design is, is you’re deciding to do one thing or another, right? So here’s the thing. If you don’t know, that’s what design is, how can you actually make good decisions, right? How can you move your design forward if you don’t realize that every time you put that pencil down to paper, which nobody does anymore obviously, but every time you click that mouse you’re making a decision. So you know, valuing those decisions is important and super hard to keep in mind and also very fluffy. But really that’s where it’s at. I mean, because who else is going to do it? I mean all these buildings keep popping up. Do they happen spontaneously? No. People are drawing them. People are developing them.
Robb: (29:37)
Right. So being mindful, being conscious, learning.
Steve: (29:42)
Yup. There it is.
Robb: (29:46)
Thank you very much Steve.
Speaker 4: (29:52)
Thank you for listening to buildings and beyond. For more information about the topics discussed today, visit www.swinter.com/podcast and check out the episode show notes buildings and beyond is brought to you by Steven Winter Associates. We provide energy, green building and accessibility consulting services to improve the built environment. Our professionals have led the way since 1972 and the development of best practices to achieve high performance buildings. The production team for today’s episode includes Dylan Martello, Alex Mirabile, and myself. Heather Breslin, thank you for listening and we’ll see you next week.